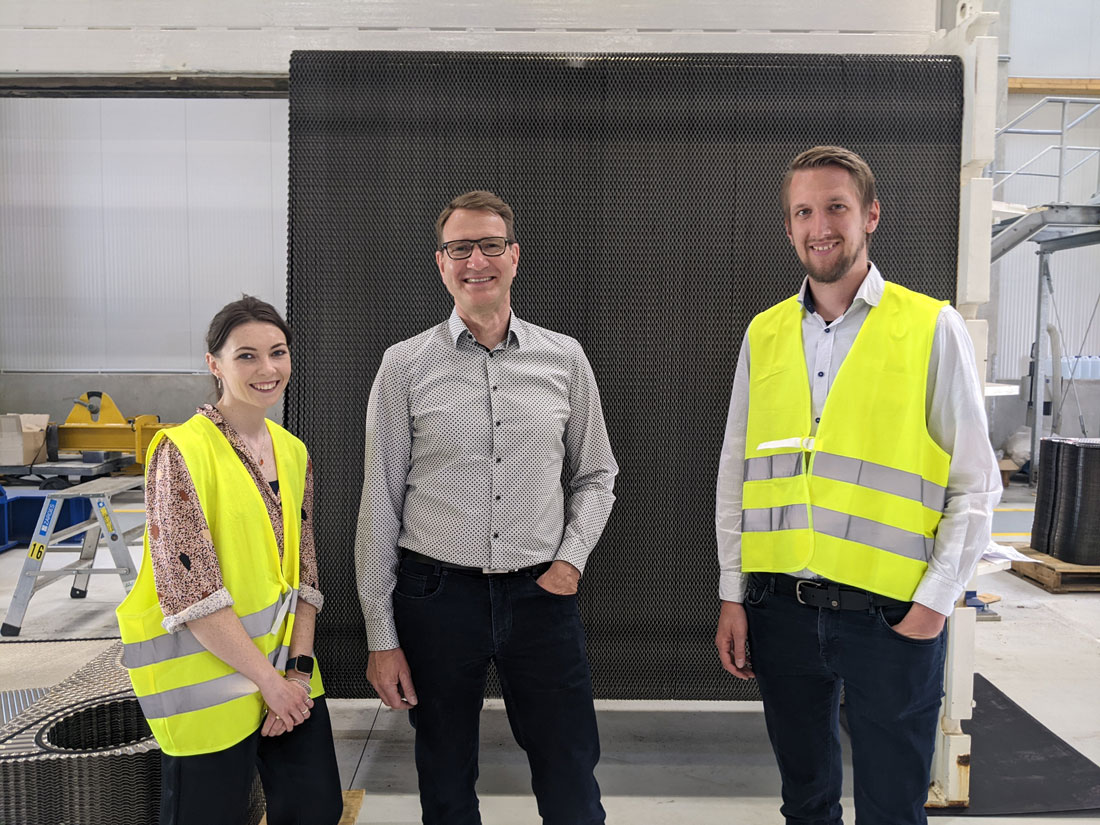
The Heat Exchanger World team was invited to the new Alfa Laval Service Centre in Frechen, Germany, last month. We spoke with Head of Global Service Operations, Mr. Jens Pulczynski, about the company’s dedication to customer experience and sustainability, its innovations in plate heat exchanger servicing, and its ambitions for the future.
By Ellie Pritchard
The Frechen Service Centre officially opened in September 2021. One of the largest in the world, this service centre is dedicated to the cleaning, repair, and maintenance of plate heat exchangers, and boasts an almost fully automated system. “We were looking to modernise and expand our service offering for customers and so we needed a large facility that was strategically located,” Mr. Pulczynski explains. “Frechen is ideal due to its proximity to the Netherlands, Luxembourg, and Belgium, even France, so it is the perfect location for serving our customers in these countries as well as Germany, Switzerland, and Austria.”
Pilot project
Alfa Laval aims to use its Frechen facility as a pilot project to test new cleaning systems before replicating them in its other centres, such as its Houston facility in the US. The fully automated chemical cleaning system enables plates to be washed even through the night with minimal staff presence, thus providing a bigger cleaning capacity and a faster service for customers. Most equipment is returned to customers within a maximum of 3 weeks, which results in significantly reduced downtime, another huge benefit. The 5,200 square metre facility is capable of cleaning plate heat exchangers up to 3,5 metres tall and 32 tons in weight.
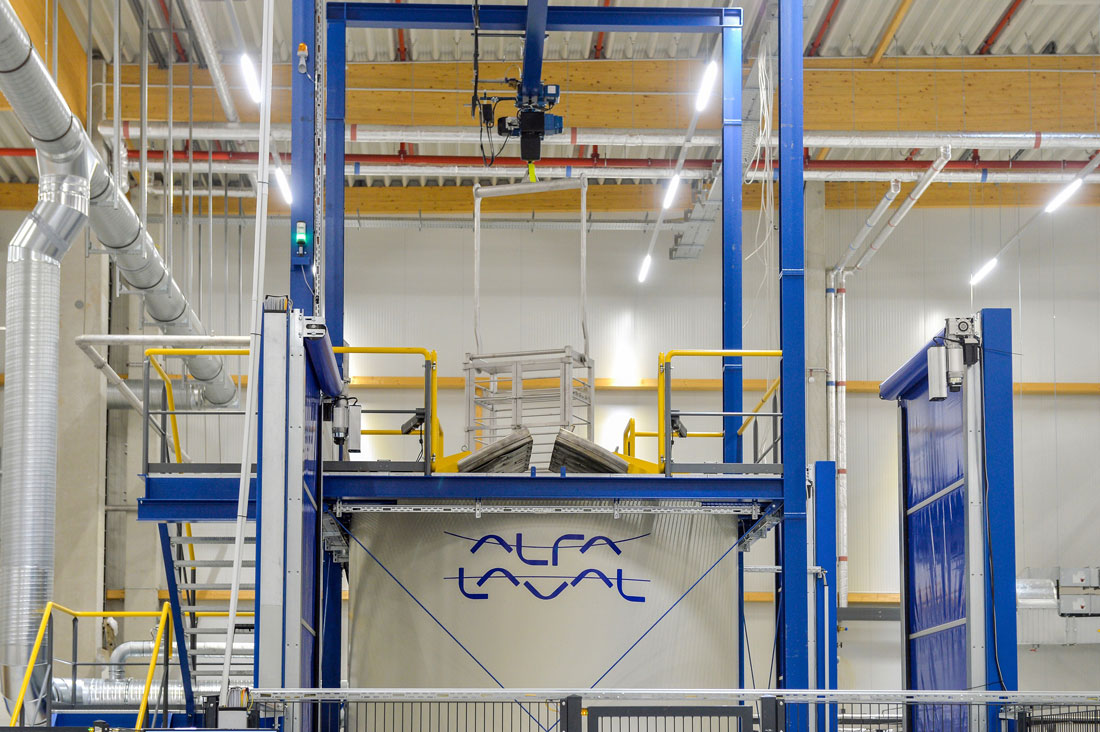
Full service
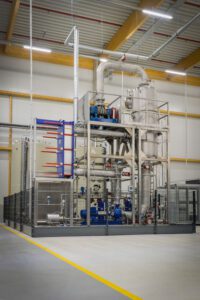
The service offered at Frechen begins with an initial consideration of the equipment to assess if any parts need to be replaced, and all plates are inspected for corrosion, erosion, and distortion. This helps to reduce costs and pollution as it avoids unnecessary work further down the line.
The plates must then be prepped for the automated cleaning system by having all gaskets removed. Those plates with glued gaskets are put through a semi-automated nitrogen tank system. Within these tanks, gaskets and adhesives are frozen at -196°C meaning that they can be removed in a cleaner and more efficient way than other methods. For glueless gaskets, experts remove these by hand.
The plates are then pre-cleaned – the method for this is high volume but low pressure, meaning heavily fouled plates can be cleaned without potential for damage which can come from high pressure cleaning. This pre-cleaning tunnel is equipped with 112 nozzles (spray heads) and uses a low pressure of 8 bar to set in motion 700 to 1,400 litres of water per minute for plate pre-cleaning. The system is highly efficient, taking only 2 minutes per plate.
From here, plates are added to the fully automated ultrasonic chemical cleaning system which can operate 24/7 – increasing efficiency even further. Plates are submerged in chemical baths, consisting of seven tanks in total. The ultrasonic feature of this system reduces process time by 70% which in turn reduces the amount of chemicals used.
Arguably the most vital element in the process is the non-destructive crack testing, which detects cracks and holes in plates, even those too small for the naked eye to see. The service centre has a large darkroom where panels sprayed with a UV coating by an automated system are inspected under UV light by experts. Plates that are found to have deformations or pores are discarded and replaced, ensuring the integrity of the final plate pack when the heat exchanger is reassembled.
The Alfa Laval team then applies new gaskets to the plates, of the company’s own design, and the exchanger is reassembled. A water pressure test is carried out to ensure there are no leaks at all, before returning the equipment to the customer. The customer is also provided with a detailed report covering the service, including process documentation and recommendations based on the results. The Service Centre is not exclusively for Alfa Laval heat exchangers as the team has the knowledge and experience to service plate heat exchangers from any brand. The Frechen facility was in fact designed to welcome PHEs from all brands and any kind and reliably service the equipment to the high standard associated with the Alfa Laval brand.
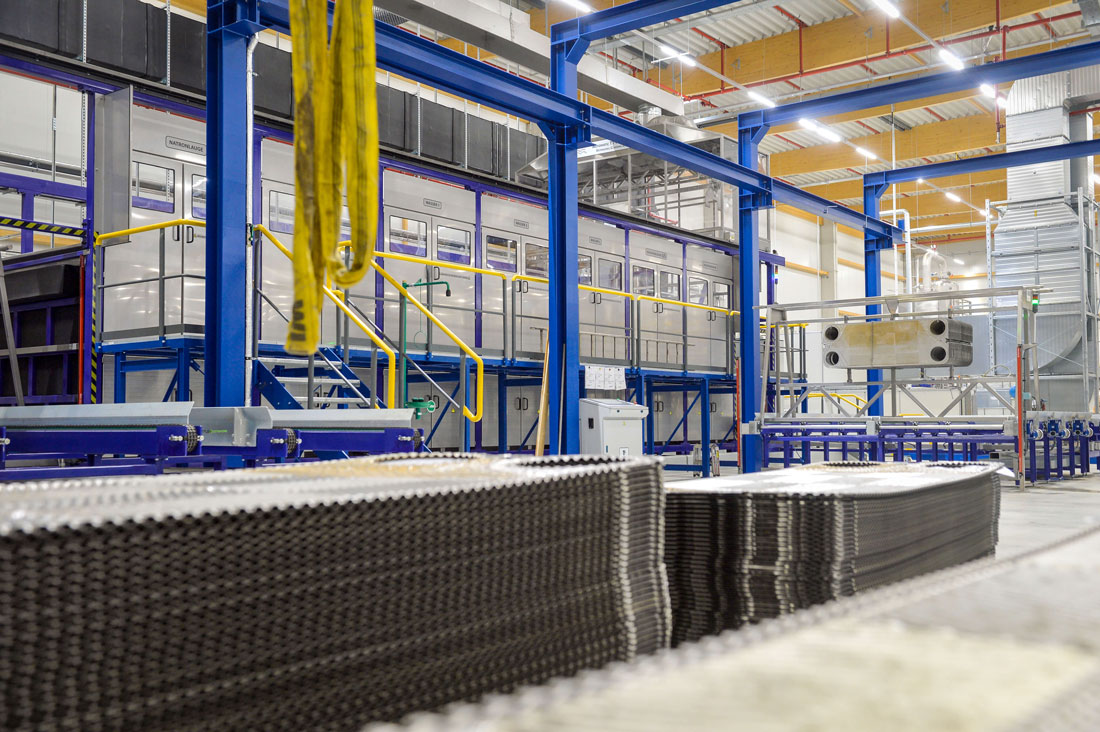
Sustainable practice
The Service Centre is essentially a one-stop-shop for a full plate heat exchanger ‘health check’. “Proper cleaning is important for a heat exchanger because, once returned to an almost original state, it can run efficiently and save energy again. Rather than retiring equipment and manufacturing new exchangers, a system such as this lengthens the lifetime of the equipment.”
Mr. Pulczynski stated that Alfa Laval has one main focus in every aspect of its business: sustainability.
“This is very important to us,” he explains. “This service centre, for example, recycles almost 100% of its wastewater as we use a closed loop filter system: aiming for zero liquid discharge, the water used for cleaning is evaporated, condensed, and all the solid debris is filtered out. The water is sent to a water treatment unit which returns it to the system to be used again. No water is wasted in this process.” When asked to explain the motivation behind this, Mr. Pulczynski said: “Simply, water-use reduction. This part of the world fortunately doesn’t struggle with water availability at the moment, but there are many places that do or soon will; this kind of system will be very much needed in areas where water is a scarce commodity.”
Alfa Laval is vocal about its sustainability targets, and aims to recycle all water in its operations by 2030. Also, the professional, regular servicing of plate heat exchangers makes an important contribution to decarbonization: according to the company website “estimates show that around 1-2.5% of the world’s CO2 emissions could be prevented if heat exchangers installed in industrial processes were cleaned and maintained properly”.