AVA district heating transfer station in Germany, owned by Stadtwerke Augsburg, was retrofitted with two hybrid tubular heating condensers for district heating hot water generation. In this article, Manfred Hermanns explains how the power output increased from 36 to 48 megawatts with only minor infrastructural adjustments.
By Manfred Hermanns, CTO VAU Thermotech GmbH & Co. KG
AVA (Abfallverwertung Augsburg – i.e. municipal waste utility Augsburg) was founded in 1991 and is owned by the city and the district of Augsburg and the district of Aichach-Friedberg. It operates a cogeneration waste incineration plant with three incineration lines, which produces approximately 100 gigawatt hours of electricity and 200 gigawatt hours of district heating per year for private households and industrial companies. The residential and commercial waste is collected in the city of Augsburg and surrounding districts.
As usual in the combined heat and power production (CHP), the steam is fed into a power generating turbine and then decoupled for district heating. This steam releases its heat via the heating condensers to the district heating water. In CHP, district heating is a by-product of electricity generation, but directly increases the efficiency of the combined heat and power plant and reduces its CO2 emissions.
Increasing performance despite limited footprint
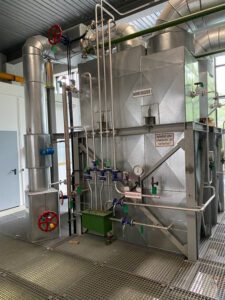
Until recently, two parallel operated heating condensers for decoupling of district heating were used, each with a heat output of 18 megawatts. “Due to the modernization of the power plant, we needed a retrofit of the two already existing heating condensers as well. The main target was to increase the output of the district heating transfer station by around 33 percent”, says Heinrich Lenort, head of peripheral heating plants at Stadtwerke Augsburg Energie GmbH. “Due to our positive experiences with the existing heating condensers, we decided to tender for vessels of the same design.”
The existing system with an output of 2 x 18 megawatts was designed with two very compact, fully welded hybrid tubular plate heat exchangers, which had been mounted in 1996 and still work to the complete satisfaction of AVA and Stadtwerke Augsburg. To increase the power output, it was initially planned to supplement the two already existing heating condensers by a third vessel mounted right beside the others, which would have been feasible considering the dimensions of the building.
During a site visit it became apparent that adding a third heating condenser would have entailed extensive changes to steel construction, platforms and pipelines. Finally, the recommendation was to replace the two heat exchangers with two modified and even compact new hybrid tubular plate heat exchangers.
Vessel construction considering structural conditions
During the design process of the vessels, important aspects had to be considered: first, increasing of the heat output according to the new specifications; second, customization of the pressure vessel housing according to the given space in the building; third, limitation of the construction height due to the indoor crane; and fourth, if possible, using the existing steel construction.
The constructive approach was twofold and proved the high design flexibility of the hybrid tubular plate heat exchanger. Since its heating surfaces made from fully welded stainless steel plate packs are variably and modularly adjustable in length, width and height, the heating condensers could be easily adapted to the given room size, pipes, ports etc.
Also, compared to standard welded plate heat exchangers, an outstanding feature of the hybrid tubular plate heat exchanger is that the ports are welded onto the hoods only and not onto the plates. Therefore, the plates used in the freely definable pressure-bearing housings are completely variable regarding length, shaping depth and the number of plate packs. Thus, a suitable design can be found for almost all given geometries.
The outlet nozzles for the district heating hot water of the old heating condensers were welded vertically upwards on the water hood and connected to the district heating inlet via a pipe bend. Due to a design change of the upper water hood the district heating nozzle could be led out directly to the side. The result was an additional gain in height that was used to add more length to the plate packs. This design change had a direct impact on the height of the steam inlet nozzle resulting from the lengthening of the plate pack. Normally, the steam side of the heating condenser is provided with a straight connection on the steam inlet hood. In this case, the steam inlet port was welded directly into the steam chamber with a 90° bend. With this constructive measure, the new heating condensers could be connected to the steam distributor with only minor infrastructural changes. And due to the design changes of the water hoods on the district heating side and the port rearrangement on both sides, only minor adjustments to the existing pipe system were necessary.
Designing plate packs based on performance parameters
After the maximum dimensions of the housing had been defined, the heating output had to be dimensioned accordingly: “Our specification demanded an output increase from 36 to 48 megawatts with the same parameters and integration into the existing system”, says Heinrich Lenort. The desired performance increase of the vessels was achieved by reducing the plate shaping depth and increasing the number of plates. Additionally, the plates were slightly longer and the inlet hoods were slightly modified. These changes enabled an optimization of the heating surfaces as desired.
The specific plate design of the hybrid tubular plate heat exchanger creates on the corrugated side optimal flow areas for the water to be heated and on the tube side an enlarged cross-section for the more voluminous vapor. Due to the adjustable shaping depth and compared to other fully welded plate heat exchangers only the hybrid tubular plate heat exchanger offers such a huge and variable flow area. And compared to a shell-and-tube heat exchanger, the hybrid tubular heat exchanger still has a specific heating surface density that is about three times higher per m³ of space. Essentially, the VAU Thermotech plate design is absolutely variable regarding shaping depth offering interesting options for design adaptation.
Finally, the pressure-retaining housing of the new vessels had very similar dimensions to the old heat exchangers. With the new hybrid tubular heat exchangers, a 33 percent higher yield could be achieved compared to the previously used vessels. A total of 48 megawatts of power has now been achieved – 24 megawatts per vessel.
Stadtwerke Augsburg case study
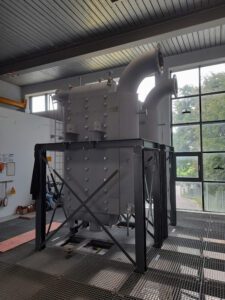
The new hybrid tubular heating condensers built for Stadtwerke Augsburg district heating transfer station have a height of 3.5 meters, a width of 2.2 meters and a depth of 0.6 meters. The vessels have a heating area of 203 m² and an empty weight of 4,600 kilogram.
The hot water generation occurs in cross flow: Steam enters the inlet header from above via a DN 400 port, flows horizontally through the tube side, heats the water that is pumped over the corrugated side and condenses in the process. On the tube side the condensate collecting at the bottom of the vessel is forcibly guided by baffle plates to the condensate outlet nozzle via several passes. In this way a precise subcooling to a specific target temperature is achieved.
Heinrich Lenort comments: “VAU Thermotech delivered the new heating condensers by truck from Thuringia to Augsburg precisely on time. In Augsburg, the vessels were hoisted using an indoor crane. Previously, we had redesigned and adjusted all pipelines and the steel construction in the power plant for the higher output. The old vessels were removed and are now being used at a different location.”
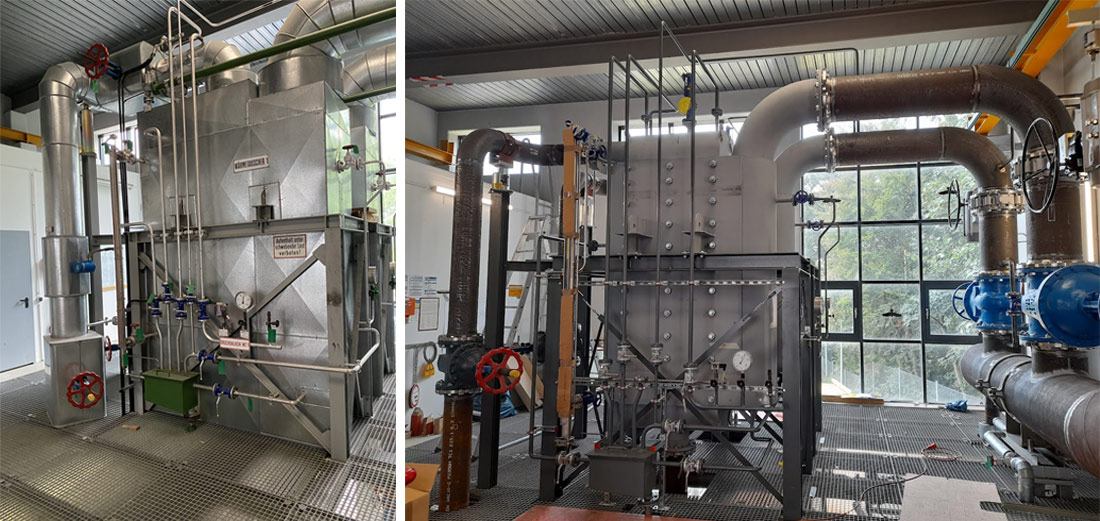
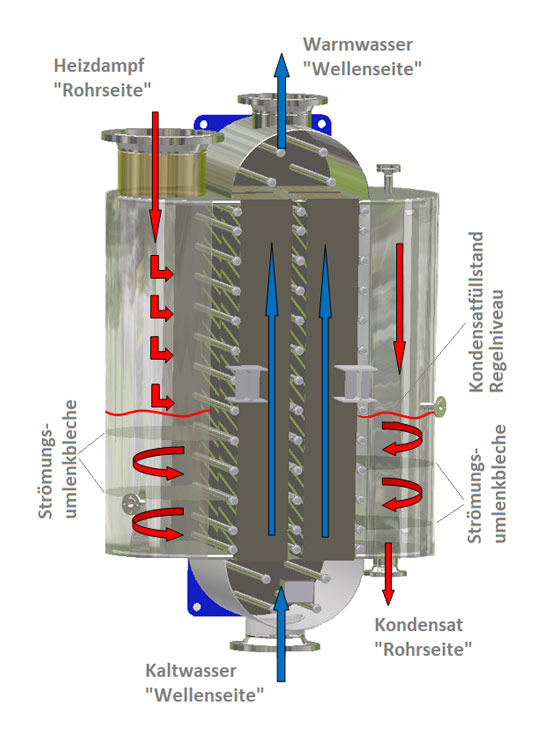
Heat capacity available as needed
Heinrich Lenort explains: “The preparation of hot water for district heating varies seasonally. In the summer when heating is not necessary, the power plant is mainly used to prepare hot water for private households and to supply the industry with process heat. So, we use a flow temperature at 95°C and a return flow temperature of around 65°C. To provide the households with district heating in winter, the flow temperature must be 130°C. Therefore, additional power in the form of steam and a larger heating surface are required.”
The heating capacity of a hybrid tubular plate heat exchanger is comfortably adjustable between 0 and 100 percent by minimizing or maximizing the area of the plate pack through which the steam flows. This is achieved using the “condensate level control” principle: The heating capacity is controlled via the condensate drain valve, that regulates the amount of condensate drained. A reduction in the valve cross-section increases the condensate level on the tube side. This reduces the available condensation area and the transmitted capacity. If, on the other hand, a larger heating surface is required again, simply open the condensate drain valve to release a higher heat transfer capacity. If the condenser has to be shut down, the steam room needs to be completely flooded with condensate. Positive side effect: the condensate protects the device against corrosion known as ‘wet preservation’.
Retrofit successfully accomplished
Heinrich Lenort is satisfied: “Since October 2021 the system is in operation without any issues. What was important to us was a compact design, less maintenance and absolute tightness, even at changing operating conditions. After the initial commissioning and optimization of the control circuits, all load points including full load with a maximum of approx. 46 megawatts were approached and tested without any problems during the trial run. Overall, it can be stated that all expectations and specifications of Stadtwerke Augsburg have been met by 100 percent. We therefore recommend the concept of hybrid tubular plate heating condensers.”
About the Company
The independent and owner-managed VAU Thermotech GmbH & Co. KG was formed in 2008 by the takeover of VAU Werkzeug- und Gerätebau GmbH & Co. KG, which was founded in 1977. The owner and CEO is Osama Nasser and the headquarters and production are located in Northern Thuringia, Germany; the branch office in Munich is an innovation hotspot for the development of new products.
About this Featured Story
This Featured Story was first published in Heat Exchanger World Magazine in July 2022. To read more Featured Stories and many other articles, subscribe to our print magazine.
Featured Stories are regularly shared with our Heat Exchanger World community. Join us and share your own Featured Story on Heat Exchanger World online and in print.