The following article focuses on the question of whether the use of organic heat transfer fluids creates the stringent necessity to classify an explosion zone around the heat transfer system. It is based on our long experience in designing, manufacturing, and carrying out maintenance, repair and technical service work on a huge variety of different heat transfer fluid (HTF) systems as well as on our knowledge of explosion protection regulations.
Dr.-Ing. Andreas Glück – Co-founder & Managing Partner, heat11 GmbH & Co. KG
Directives and regulations
Standards
Generally heat transfer systems for organic heat transfer fluids should be designed and manufactured according the following directives and standards:
• EU machinery directive 2006/42/EC, annex II B
• Pressure Equipment Directive 2014/68/EC
• EN ISO 12100 Safety of Machinery
• DIN 4754 Heat transfer systems operating with organic heat transfer fluids – Safety requirements, test
If installed in foreign countries outside Germany, ad-ditional local standards may have to be considered.
Classifications and criteria
The classification of explosion zones is based on the probability and the duration of the occurrence of an explosive atmosphere in certain areas:
• Zone 0: Continuously, for long periods or frequently
• Zone 1: Occasionally in normal operation
• Zone 2: Not likely in normal operation, but if so, only for a short period
In order to create an explosion, the following criteria have to be fulfilled at the same time:
• Concentration of combustible substances within their explosion limits
• Hazardous quantity of an explosive atmosphere
• Presence of an effective ignition source
If one (or more) of those criteria can be certainly avoided an effective explosion protection will be achieved.
Flash point and auto ignition
In this context, it seems to be important to distinguish between two expressions that are used for organic heat transfer fluids:
Flashpoint
• Lowest temperature at which a volatile substance can vaporize to form an ignitable mixture in air
• An additional source of ignition is required to start burning. When the source of ignition is removed the burning normally ceases
• Most commonly organic heat transfer fluids are op-erated at temperatures above their flash point (i.e. flash point Marlotherm SH: 200°C acc. DIN 22719)
Auto ignition point
Lowest temperature at which a volatile substance will spontaneously ignite in normal atmosphere without the necessity of an ignition source. Most commonly, organic heat transfer fluids are operated at temperatures below their auto ignition point (i.e. auto iginition point Marlotherm SH: 450°C acc. DIN 51794)
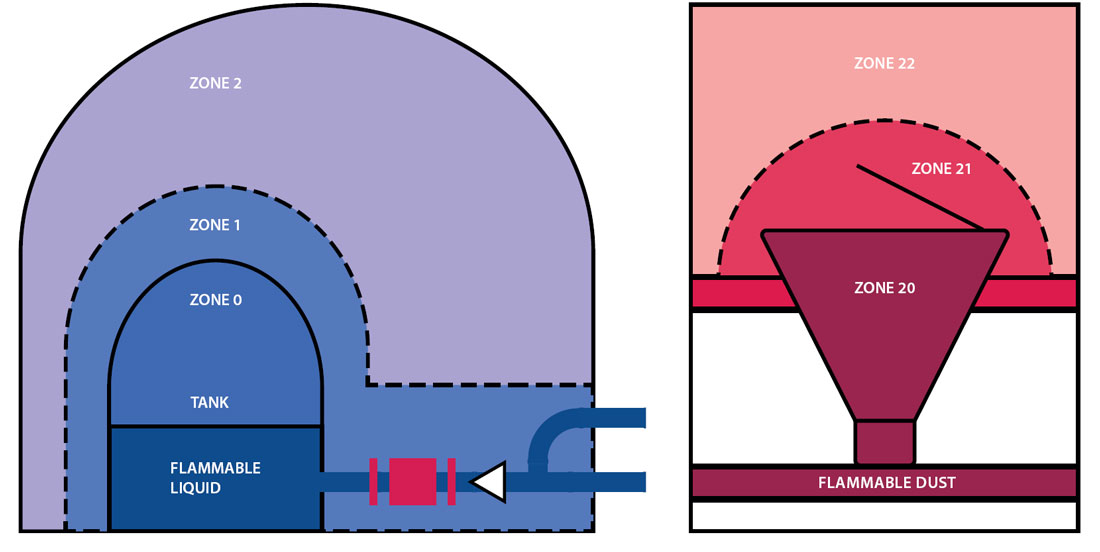
Avoidance of explosive atmospheres
Basic considerations
According to the regulations TRBS 2152 (Technical Rules for Operational Safety) and TRGS 720 (Technical Rules for Hazardous Substances) published by the responsible German committees, the occurrence of hazardous explosive atmospheres outside of systems can be avoided or effectively restricted by the tightness of the system. Basically, it will be distinguished between permanently technical tightness, technical tightness and not-guaranteed tightness.
• Permanently technical tight: (either by design and/or by inspection and maintenance): no or only negligible release of combustible substance and hence no explosion hazardous areas to be classified
• Technically tight: (no release in normal operation, only in case of rare malfunctions): only secondary release in areas (zone 2)
• Tightness not guaranteed: primary release (zone 1)
According to the explosion protection guidelines published by BG Chemie (ZH 1/10 published June 1988, now changed to BGR 104), there is no requirement for explosion protected design of electrical equipment used in heat transfer systems that are technically tight (by construction). At areas where a hazardous quantity of an explosive atmosphere can occur due to leakages, a classification of zone 2 in a 3m radius around such release area should be defined.
The basic considerations for the explosion hazard of a heat transfer system depend on its design. The DIN 4754 describes the design and safety requirements of a heat transfer system. The crucial criterion is the concept of “technical tightness” of a heat transfer system, designed and built according to that standard. Such heat transfer systems shall be permanently technically tight due to the design.
Potential hazard areas
Potential hazard areas in a heat transfer system are seals (gaskets on flanges as well as pump seals), safety relief valves, vent lines, sample valves and tanks (drain tank and expansion tank).
Seals and gaskets
Generally, the number of flange gaskets in a heat transfer system should be minimized by design. The use of weld-in valves and fittings is a possible way to achieve this. Where unavoidable or at least not recommendable due to maintenance and repair work (for example pumps, control valves, safety relief valves), only approved flange gaskets should be used and the installation should strictly follow the installation guidelines of the manufacturer.
Pump seals
Still, most of the heat transfer fluid pumps in operation worldwide are designed with mechanical shaft seals and therefore very small leakages are possible at this point. Due to the special design of these pumps the temperature of the leaking fluid is generally below the flash point. Nevertheless mechanically sealed pumps require a high attention of the operating personnel. The use of hermetically sealed pumps as pumps using a magnetic coupling or canned motor pumps is therefore recommended.
Safety relief valves and vent lines
The potential of a hazardous explosive atmosphere around those points has to be evaluated and a zone classification around those areas may be required depending on location, construction and operating procedures. It is common practice and recommended by DIN 4754 to lead such “emission points” to a safe place at the outside of buildings by welded piping. As a consequence, the classification of the rest of the heat transfer plant is not influenced.
Sample valves
In a properly designed heat transfer plant, special oil sample drafting devices should be installed. The representative oil sample is cooled down to temperatures below 50°C before drafted.
Tanks
For tanks that might contain organic heat transfer fluids above their flash point, a zone classification for the interior of the tank may be required. This can be avoided when the tank is covered by an inert gas like nitrogen.
Emergency shutdown
For the emergency shutdown of all electrical equipment, an emergency switch has to be installed in the power supply line. This switch has to be installed in a safe area; usually outside the heat transfer systems room. Equipment which has to be operational after emergency shut-down, like escape route lighting, shall be safeguarded against explosion hazards.
Conclusion
Finally, it can be concluded that if all the above mentioned standards and design criteria are considered and state-of-the-art equipment is used, it is good practice to operate heat transfer fluid systems without any classification of explosion areas deriving from the presence of the organic heat transfer fluid itself.
We hope that these statements contribute to your efforts to find a technically feasible solution and get a clear and objective picture on the basis of technical arguments.
All statements are made to the best of our technical judgement and shall not have prescriptive status as from technical or Third Party authorities. If there are different or newer regulations or guidelines applicable we can’t guarantee the completeness and validity of these statements in a legal sense.
About the author
Dr.-Ing. Andreas Glück studied general mechanical engineering at the University of Stuttgart from 1983 to 1989 and completed his doctorate at DLRin 1996 on the subject of high-temperature thermal energy storage systems. He then worked in plant engineering in the field of process heat supply/temperature control with a focus on plants with organic heat carriers, so-called “thermal oils”. He is co-founder and managing partner of heat11 GmbH & Co. KG in Bielefeld, a specialist in de-signing and manufacturing of process heat plants in the temperature range from -100°C to +480°C.
About this Featured Story
This Featured Story was first published in Heat Exchanger World Magazine in November 2022. To read more Featured Stories and many other articles, subscribe to our print magazine.
Featured Stories are regularly shared with our Heat Exchanger World community. Join us and share your own Featured Story on Heat Exchanger World online and in print.