Image above: New Funke safety shell and tube heat exchangers, Model SWF-HE with compensators in the safety space. The compensator protects the safety space from the effects of excessive temperature differences between the jacket and tube sides.
Safety shell-and-tube heat exchangers were developed and patented back in the 80s by FUNKE Wärmeaustauscher Apparatebau GmbH (hereafter, Funke), with its registered office in Gronau/Leine, as a solution for the highest plant safety standards. Now Funke is bringing an innovative and efficient product upgrade to the market.
Text and images courtesy of FUNKE Wärmeaustauscher Apparatebau GmbH
With the SWF-HE, double-walled tubes and a safety space with leak monitoring guarantee plant safety and thus improve plant efficiency as any unplanned down-time can be avoided. Moreover, the SWF-HE saves space and may be used for high operating pressures of up to 100 bar and temperatures of up to 300 degrees Celsius.
Safety is the bottom line
The top priority with the development of this new product was the combination of absolutely reliable medium separation and optimum heat transfer without the use of an additional medium in the safety space. In this technical solution, two individual tubes made of steel or stainless steel – one placed inside the other – are used, with the inner tube of the pair having a fine pyramidal structure on the outside. The two tubes are connected to each other, metal to metal, by hydraulic expansion at extreme pressures, creating a double-walled safety tube at the end.
If a tube fails during operation of the heat exchanger, the medium first finds its way into the safety space between the two tubes. This is linked to a sensor that shows the change in pressure in the safety space and triggers an alarm on the plant control device. Whether the pipe is breached from the sleeve or pipe side can be determined via the pressure in the safety space, as this always corresponds to the respective operating pressure. As the second pipe wall is not damaged, the heat exchanger can be operated without any problems until the next scheduled service. Leaks will be identified in good time allowing repairs and replacement purchases to be planned over the long term. Safe operation of the heat exchanger is still guaranteed.
Current applications
This heat exchanger is already being used in large-scale facilities for producing polysilicon. Silicon and silicon compounds have diverse uses, including photovoltaics and micro-electronics. Individual components are often subject to extreme conditions with regard to climate and environment, due to changing operating conditions as well as initial and final circumstances. Different loads due to various pressure and temperature conditions are associated with this. This not only places the highest demands on the quality of the hydraulically expanded double tube system and the tube-to-tube sheet connection, but also in each heat exchanger’s individual chamber with regard to the relevant prevalent temperatures. In order to offset varying expansion due to different temperatures between the shell and tube space, the use of a compensator may be necessary not only in the shell space but also the safety space. The various demands on welds and tube-to-tube sheet connection can also be absorbed by compensators.
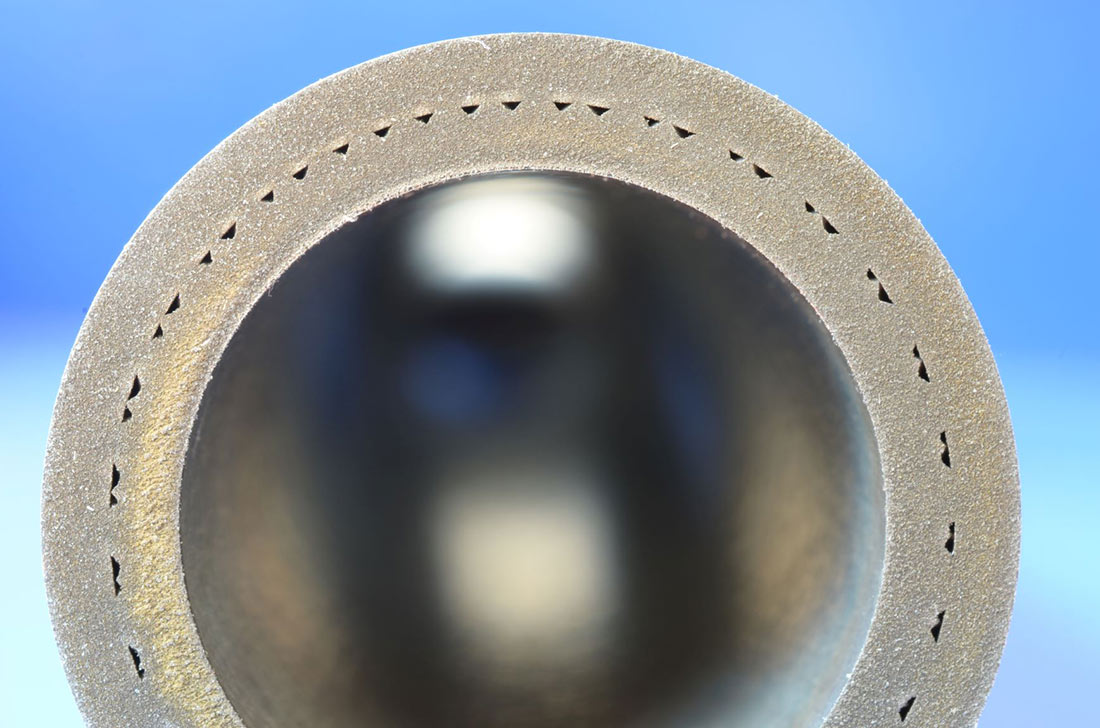
Under no circumstances may silicon alloys be allowed to come into contact with water or similar materials. When manufacturing polysilicon and in other chemical processes with high medium reactivity, us of the SWF-HE is the perfect solution as it guarantees heat transfer even without media in the safety space.
The safety shell-and-tube heat exchanger is often used when avoiding mixing the media is absolutely imperative, for instance when using river water as the coolant. In this event, working with an intermediate circuit is common-place, which makes the use of two separate heat exchangers and additional pumps necessary. Only one heat exchanger is necessary when using the new safety heat exchanger as the undetected mixing of the two media is excluded by monitoring the safety space. In addition, you will save space for the second heat exchanger, thus lowering overall investment and running costs.
Natural gas applications

Another significant practical example of the successful use of the SWF-HE is the preheating of natural gas. Pre-heating natural gas increases the efficiency of combustion. Boiler feed water or steam is usually used for preheating the natural gas. Where only one safety heat exchanger is used, the heating medium reaching downstream system components such as compressors or turbines, is even impossible in the event of a pipe failure. These components would be damaged on contact with liquid.
SWF-HE safety heat exchangers are also used in electrolysis systems. Hydrogen created during electrolysis will be condensed for subsequent processing, storage or transport. Safety heat exchangers are preferred for reducing the temperature as required.
A solution for diverse needs
The highest demands of quality are also required in the food and pharmaceutical sectors. In this case, hygiene regulations must be meticulously complied with and the medium’s temperature controlled precisely. Even in this field, Funke’s new safety heat exchangers are perfectly designed for efficiently and reliably resolving the many challenges faced in practice. In addition, Funke continually develops individual bespoke solutions in conjunction with the customer.
About FUNKE
FUNKE Wärmeaustauscher Apparatebau GmbH was founded in 1974 and is one of the world’s leading developers and manufacturers of quality heat exchangers. FUNKE offers optimum
thermodynamically designed shell-and-tube heat exchangers, plate heat exchangers, oil air coolers and electronically controlled oil pre-heaters for the most varied of sectors and almost every application.
To find out more about the new Funke safety shell-and-tube heat exchanger,
see: www.funke.de/sicherheit.html
About this Featured Story
This Featured Story was first published in the February 2022 issue of Heat Exchanger World Magazine. To read more Featured Stories and many other articles, subscribe to our print magazine.
Featured Stories are regularly shared with our Heat Exchanger World community. Join us and share your own Featured Story on Heat Exchanger World online and in print.