Brazed plate heat exchanger LE400 brazed in vacuum furnace. Soon to be installed in a heat substation of a furniture factory in Poland. Hexonic BPHEs enable high thermal performance at low operating costs.
Polish heat exchanger manufacturer, Hexonic (formerly SECESPOL), has been active in the global market for over 30 years. Drawing from an experienced team and a strong company culture, the success stories over the past 18 months have been numerous – from new product launches, to large scale projects, to exciting news for the future, the Hexonic team has proven that their ambition is limitless. At the end of January 2022, the company announced its new name – Hexonic – and presented its strategy for the next 5 years.
By Ellie Pritchard
Hexonic refers to the mindset, concept and scope of operation:
HEX – heat exchange;
ON – innovation;
IC – intercontinental.
According to the company’s ambitious new strategy, the freshly renamed Hexonic aims to become one of the 5 most recognisable heat exchanger brands within the next 10 years. An iconic brand name at the forefront of heat exchanger designers and operators. And it is no accident that the ‘ON’ in Hexonic refers to the company’s innovation, its ability to move onwards and upwards. “It is the ability to design innovative technical solutions and their implementation in production, plus subsequent implementation in the markets, that prove our advantage in the professional field,” says Bartłomiej Siemieńczuk, Hexonic CEO. “For over three decades we have been known as the SECESPOL brand, but our intensive growth in interna-tional markets has led us to adopt a new name – Hexonic. Our new visual identity better refl ects our position, values and passion for what we do. The strategy adopted many years ago is working. We are constantly close to our customers; we speak their language and help them solve their problems. Over 350 Hexonic employees are committed to ensuring that our customers are fully satisfied with working with us. We want them to recommend us to others and for us to be seen by them as reliable and professional. Business means for us healthy relations, so it is no less important that our business partners associate us with being people who are simply good to work with,” Bartłomiej Siemieńczuk explained during the strategic meeting with the employees, in which the rebrand was announced.
A company’s ability to refresh its image in order to prove its growth to customers and client base is a luxury afforded to hard-working teams and strong, stable leadership. SECESPOL had both, and Hexonic has grown from this.
System solution providers
Hexonic is present in Europe, North and South America, Asia and in over 500 international commercial agencies. Despite its size, it remains a 100% second generation family-owned company, with a belief in good leadership at its core.
Heat Exchanger World spoke with Christian Huhn, Managing Director for the German subsidiary now based in Cologne, about Hexonic’s impressive year and the philosophy behind it.
“We are one of the only system solution providers when it comes to heat exchangers,” Christian begins.
“We have an extensive standard product portfolio rang-ing from plate and shell, brazed plate, shell and tube, gasketed heat exchangers, and so on. But we also offer customised industrial exchangers, from small sized units to very large. Besides this we also have dry coolers.” For almost all applications, Hexonic is able to provide a high-quality product sure to be the best fit. The company supplies equipment for sectors such as food and beverage, (hydraulic) oils, chemical, pharmaceutical, simple HVAC applications and also more demanding HVAC applications which require a precise final product specific to thermal requirements.
Numerous international awards and patents as well as certificates, such as ASME (U&UM), PED 2014/68 / EU, EAC, China ML, 3-A, ISO 9001, and ISO 3834-2, illustrate the company’s high-quality standards.
Standard +
The company’s standard product range spans from brazed and screwed plate heat exchangers to shell and tube, but Hexonic also offers what it refers to as “Standard +”. The Standard+ is a service which enables a customer to request bespoke equipment specific to their needs, with the company’s extensive standard range as a strong foundation.
“We begin with one of our standard products because, even for pharmaceutical applications, we still have a wide range”, explains Christian. “When we discover that there is something unique or special requested, then we try to find a solution for it by adjusting our product – that is Standard+.”
Hexonic tailors its service and works alongside the customer to ensure the most efficient solution. The company is built upon an experienced team of development engineers who support the planning and design of complex special designs, and its use of modern industrial technology as well as an in-house production team guarantee the best quality.
“But this is really one of our strengths, working together with the customer,” says Christian. “We collaborate because we understand the importance of a quality product for their needs.”
Leading by example
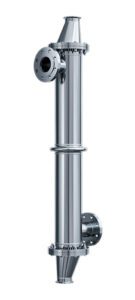
Since Christian began at Hexonic’s German subsidiary in 2019, he has seen a growth in RFQs (requests for quotation) for geothermal applications, such as heat recovery of wastewater in combination with a heat pump, or using river water for free-cooling applications. He also acknowledges hydrogen as a future market for Hexonic Germany. “We carry out market investigation and analysis, both to understand what we can do better but also to understand future technology and application trends.”
What he has also noticed is the industry’s attention to so-called “energy saving” solutions.
“‘Energy saving’ has become a kind of slogan, unfortunately,” he states. “Thinner materials may sound like a good environmental option at the start but making a part that survives its warranty period and then fails is irresponsible. What then happens to that part? Perhaps it is recycled but perhaps it is not. More resources are used, more energy is wasted in then creating a replacement product.” Christian acknowledges the aftermarket benefit that this creates for some manufacturers, but this is not the Hexonic way.
“Hexonic offers the optimal solution,” he says. “It is our job to offer alternatives – we listen to what the customer wants and, if they are not aware of the inefficiency of their proposal, we try to improve that.” With a nod to November’s COP26 in Glasgow, the company is aware of its ability to be a part of the solution and Christian anticipates a stronger global focus on efficiency in heat transfer equipment in the near future.
Company culture
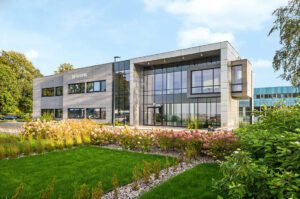
“To sell volume, we need to do it in a way that means we are recognised as heat exchanger experts that you can talk with and expect a very good technical response,” he explains. “It is very important for us to have this open conversation with the customer and say we could do something similar to the cheaper product, but in the end it is up to them if they would like to take this risk.” Christian has over 25 years of experience in the heat exchanger, HVAC and refrigeration sectors. Having worked for some large corporations in his time, Christian shares that Hexonic stands out: “This is a really great place to work, and I truly do believe that. Even from my first interview, I have been aware that there is something different about this company: a healthy culture, good teamwork, borderless working, customer- and solution-focused.” Hexonic invests in the knowledge and skill-sharing of its team, acknowledging that personal development encourages a happy and progressive mindset. The company’s R&D department, based in the Polish headquarters in Nowy Dwor Gdanski (near Gdansk), is constantly working on higher efficiency in its product range, intending to meet today’s markets and those of the future.
JAG and JAG Shield
It is from this R&D dept that the company’s two 2021 product launches were borne: JAG and JAG Shield. The JAG Plate Heat Exchanger is named after the heating plate’s inventive jagged pattern. Breaking new ground, the solution offers not only enhanced flow turbulence but also increased heat exchange area. The design results in a lighter, more compact, durable, and more efficient product which can be customised to individual requirements.
“The JAG Plate Heat Exchanger will become a long-life, dependable solution for many applications,” says Chris-tian. “We were searching for optimal strength and thermal characteristics of the JAG geometry, and so a series of computational fluid dynamic analyses were performed by our research engineers. Together with other calculations and prototype tests, they determined the precise channel performance in a plate heat exchanger.”
Tests have proven that the JAG PHE delivers up to 10% higher efficiency than a standard plate heat exchanger, reduces general pressure drop levels, and is less susceptible to fouling.
The JAG Shield is the version developed for plate and shell heat exchangers. The unique shape of the plate provides excellent thermal efficiency while maintaining low flow resistance; the flow directors are not needed as the medium is distributed evenly between the plates. Side cuts provide enough space for the shell medium entering the exchanger to properly fill the entire internal space. It also significantly reduces the local flow resistance. Optimised use of the exchanger’s volume allows for its compact construction. Additional circumferential corrugation of the heating plates stabilizes the package and optimises stresses, ensuring a longer service life.
What also distinguishes this product is the fact that instead of typical laser circumferential welding, Hexonic uses vacuum brazing to ensure a very high level of dependability and outstanding fatigue strength.
Hexonic JAG Shield (left) and JAG PHE (right).
CAIRO Online
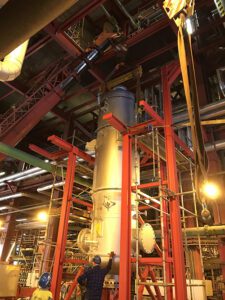
Not long after the release of JAG and JAG Shield, Hexonic announced another of its innovations: CAIRO – an online selection software.
“CAIRO is our selection software tool,” Christian explains. “In the past, we worked with an older system requiring certain software. With this latest version, users simply need internet access to use it.”
The intention is that a user could be stood in front of any equipment experiencing an issue and search for a solution using CAIRO via a standard web browser. The system conveys the entire range of Hexonic standard products, relevant to HVAC, refrigeration, oils, dairy, pool applications, and beyond. Also reinforced by the company’s R&D department, CAIRO offers a complete service, for example in the event of a sizing issue due to the safety constraints of the tool:
“If the system is not showing the solution required, then we can contact our research team. They have access to the information via CAIRO and can suggest solutions.”
Taken from the company’s website, CAIRO means that the team can preview a customer’s projects in real time, facilitating excellent communication and guaranteeing the accuracy of equipment selection. In addition to this, the system offers:
• Advanced project management
• Preview of the technical base of Hexonic products
• Insight into the properties of the fluids used in heat exchanger selection
• Application based on calculations allowing the right choice of products for specific usage.
Highlights
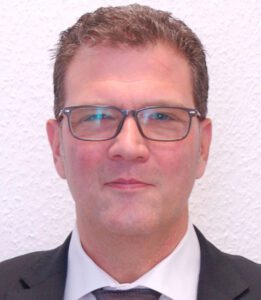
Despite a challenging year in which Christian acknowledges difficulties in reaching customers and meeting people in person, Hexonic’s momentum endured the effects of the Covid-19 pandemic well. To conclude, we discuss another highlight for the company’s German team; the Stadtwerke Munich project.
Hexonic was awarded the design, manufacture and delivery of a vast shell and tube unit to be used for circulating water system. The heat exchanger will use river water in the tubes to cool down circulating water. The build consisted of 7600 straight austenitic stainless steel tubes at 6300mm long, which were connected to a carbon steel tube sheet 2500mm in diameter. The total heat exchange area is 2911m2 and the finished product was delivered in November 2021, weighing almost 47 tonnes. Hexonic will also keep all tubes clean for better heat transfer and performance.
“This is the biggest unit we have produced so far,” Christian confirms. “This project has made the entire team here in Germany – and this extends to our Polish headquarters – very proud. Our appetite for success has grown and grown, and we are already working on more projects on a similar scale.”
About this Featured Story
This Featured Story was first published in the January/February 2022 issue of Heat Exchanger World Magazine. To read more Featured Stories and many other articles, subscribe to our print magazine.
Featured Stories are regularly shared with our Heat Exchanger World community. Join us and share your own Featured Story on Heat Exchanger World online and in print.