Klaren International, based in The Netherlands, is the inventor and developer of the proprietary self-cleaning shell and tube heat exchanger technology for operation up to zero-fouling. The technology applies continuous circulation of solid particles through the tubes of the heat exchangers to remove fouling deposits from the tube wall. Any type of fouling can be effectively handled. Any combination of hard or soft, biological, or chemical, fibrous or protein, or any organic type, or a combination of these can be removed. The company employs a team of specialists that designs and commissions new heat exchanger systems or the retrofit of existing systems into this self-cleaning configuration.
All text and images courtesy of Klaren International
Self-cleaning fluidized bed heat exchanger technology
The operating principle of the self-cleaning fluidized bed heat exchangers is based on the circulation of cleaning particles made of ceramic or stainless steel and with a size between 1.5 and 4 mm through the vertical tubes as illustrated in Figure 1. A fouling liquid flows upwards through the tube bundle of the heat exchanger that incorporates specially designed inlet and outlet channels. In the inlet channel the solid particles are fed to the fluid using a proprietary distribution system to ensure a uniform division of particles over all the tubes. The particles are fluidized by the upward flow of liquid where they create a mild scouring effect on the wall of the heat exchanger tubes, thereby removing any deposit at an early stage of fouling formation. Since the fluid velocity is higher than the falling velocity of the particles, they are lifted to the top of the heat exchanger where they are collected in the outlet channel and brought into a separator where they disengage from the liquid and are returned to the inlet channel through a downcomer pipe. To control the amount of particles fed to the inlet, a part of the inlet flow to the heat exchanger is used to push the particles from the downcomer into the inlet channel. Then the cycle is repeated.
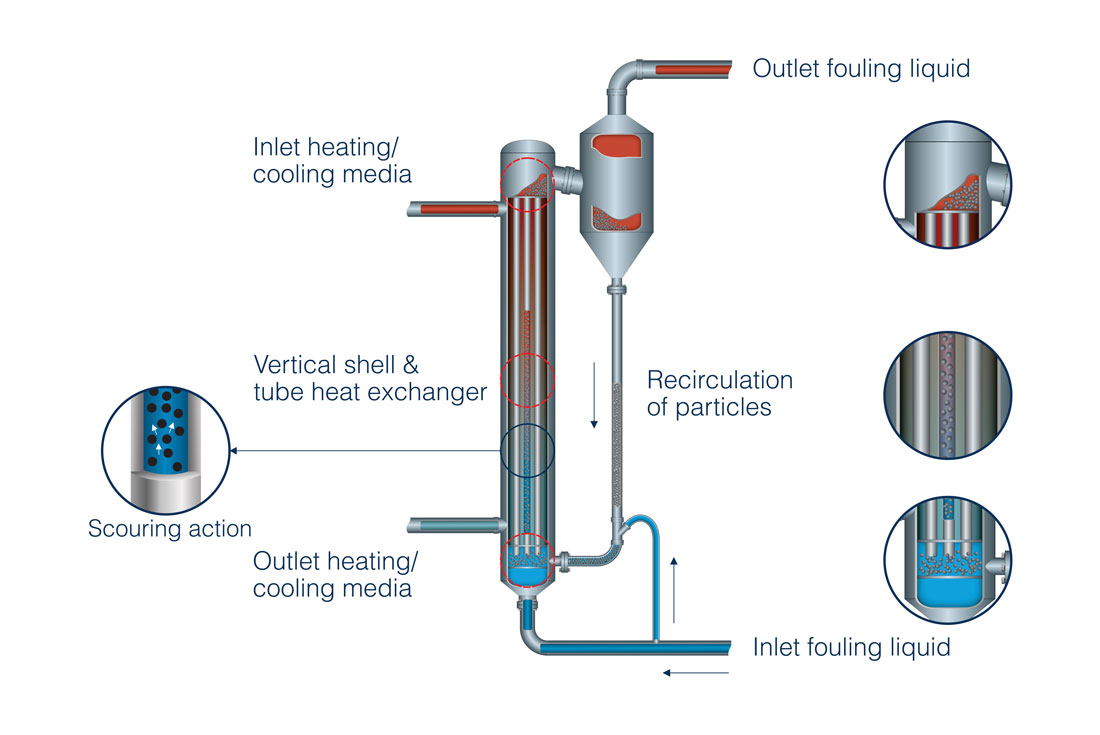
Non-Newtonian fluids
A non-Newtonian fluid is one in which the viscosity is dependent on the shear rate or equivalently the velocity gradient with which the fluid is deformed. Thus, the fluid will become either more liquid (shear thinning) or more solid (shear thickening) when subjected to a shear stress. For Newtonian fluids the viscosity is independent of shear rate. For shear thinning fluids the viscosity decreases with increasing shear rate. Some of the many examples are polymer solutions, colloidal suspensions, paper pulp in water, latex paint, blood plasma, syrup, and molasses. The typical case is paint, which does not drip from the brush because the shear rate is small, and the viscosity is high. However, it flows smoothly onto the wall because the thin layer of paint between the wall and the brush causes a large shear rate and a low viscosity.
Shear thinning effect by fluidized bed
In addition to the mitigation of fouling, the fluidized bed in a self-cleaning heat exchanger causes another important benefit for heating non-Newtonian high viscous fluids. Namely, the fluidized bed creates an internal shear in the fluid thereby reducing its viscosity. The reduced viscosity will improve the heat transfer characteristics. This improvement is on top of the effect that the fluidized bed has in any liquid where the chaotic motion of the particles near the tube results in a reduced boundary layer thickness and therefore an increased local heat transfer coefficient. Besides an increase in heat transfer and a reduction of viscosity, the pressure drop also reduces over the heat exchanger which will result in a lower energy consumption.
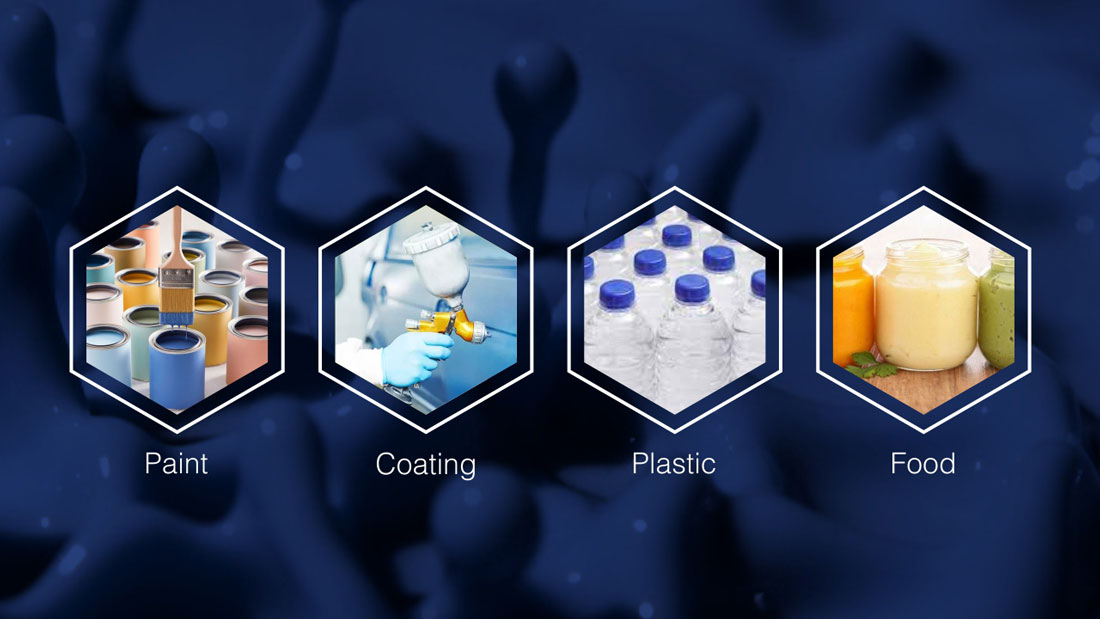
Experiences with shear-thinning effect
The first experiences with shear thinning effect by the fluidized bed on a very viscous non-Newtonian fluid was gained when a forced circulation effect evaporator in an al-cohol plant was equipped with a self-cleaning fluidized bed and the installation did not perform as expected. Opera-tion of the installation showed that the viscosity specified by the Customer, as approximately 200 cP (200 times water), did not correspond with the viscosity of the liquid experienced by the fluidized bed in the heat exchanger tubes, which was recalculated at only 20 cP. It became clear that the fluidized bed created an ‘internal’ shear rate in the flowing liquid thereby affecting the ‘apparent’ viscosity. So, it was learned that the shear-thinning effect needs to be considered when designing a self-cleaning heat exchanger. Another experience is related to a mining slurry. The effect on the heat transfer coefficient by the effect of
the fluidized alone and the combination with a reduced viscosity resulted in an increase in heat transfer of 100%. The heat transfer coefficient for a conventional shell and tube heat exchanger for a slurry with a solid percentage of approx. 32% and a velocity in the tubes of 1.40 m/s having condensing steam in the shell was found to be between 700 to 1,000 W/m2K. In this conventional heat exchanger, the slurry behaved as a fluid with a viscosity somewhere be-tween 50 and 75 cP. When applying the self-cleaning heat exchanger with a fluidized bed the heat transfer coefficient was between 1,800 to 2,000 W/m2K. In the self-cleaning heat exchanger, the slurry velocity in the tubes was only 35 cm/s. In the self-cleaning heat exchanger, the slurry behaved as a fluid with a viscosity of only 15 cP, which is a factor 5 less than in the conventional heat exchanger.
So, the heat transfer coefficient for the conventional heat exchanger in clean conditions was only half of the one for the self-cleaning heat exchanger. Both, in clean condi-tions. The conventional heat exchanger was also fouling which finally before the monthly cleaning reduced the heat transfer coefficient to 350 W/m2K. When comparing the heat transfer coefficient in a fouled condition with the one for the self-cleaning heat exchanger, the difference is at least a factor of 4. This means that the self-cleaning heat exchanger can be designed with only 25% of the area of the conventional one.
Recently, the shear-thinning behaviour of a non-Newtonian viscous liquid has been verified in a fluidized bed expan-sion experiment using a high viscous paste with almost 60 volume percentage of solids. As shown in the graph of figure 3, the lower the porosity, which corresponds with a higher volume fraction of particles, the lower the appar-ent viscosity in the heat exchanger. So, a higher volume fraction of solids increases the shear rate and lowers the apparent viscosity which improves heat transfer. Assuming a factor 4 on viscosity between no shear and a maximum volume fraction, the tube side film coefficient as derived from the equations for pure liquid flow goes up by 75%.
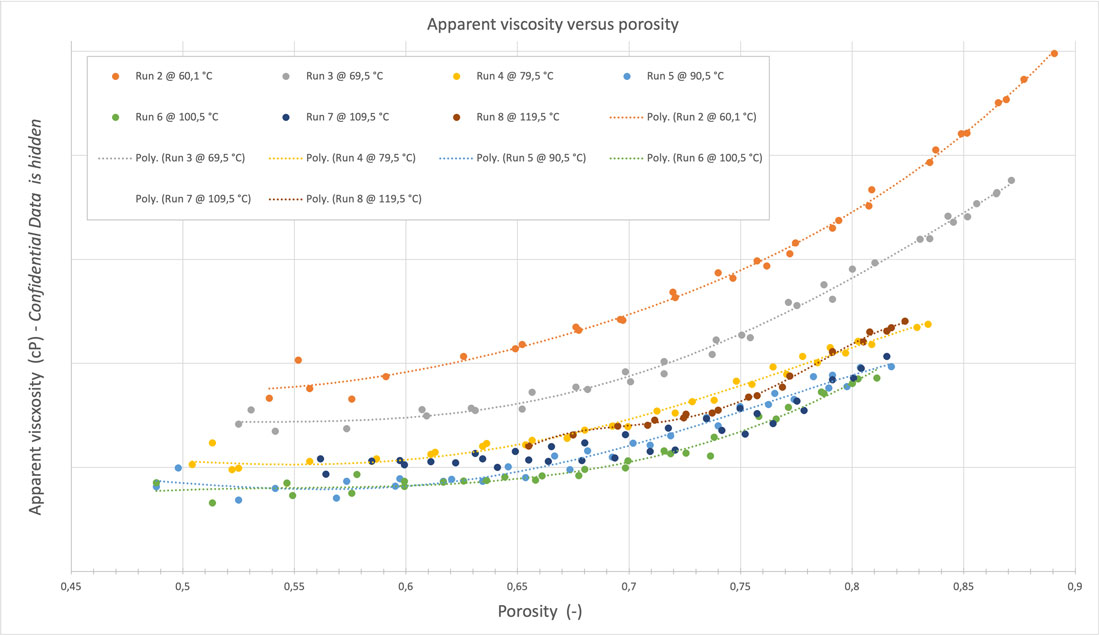
Conclusion
Overall, it can be concluded that the fluidized bed besides the reduction of fouling and improving heat transfer also can reduce the apparent viscosity of high viscous liquids with a factor between 5 and 10. This improves heat transfer even more and reduces the pressure drop and as such the required pumping power, and hence is energy saving. Concentrated (or dense) suspensions are utilized in a multitude of natural and industrially relevant products and processes such as mining (slurries), petrochemical, paint, coating, plastics and food industries.
Klaren’s technology is now proven with industrial trials in recent years with the desired results.