Find the dominant fouling mechanism
In this series of articles we will look at how heat exchangers foul, how to understand the root causes of fouling, and how to mitigate the impact of fouling. The material presented is based entirely on the author’s experience and analysis of operating situations in the Oil & Gas industry. However, many theories and varied experiences exist across the industry and amongst researchers.
By Himanshu Joshi – Heat exchanger specialist
In this third article of the series we will take the information from Parts 1 and 2 and see how to combine it with process conditions and feed testing to determine the dominant (or most likely) fouling mechanism. Once we know the mechanism, we will take the next step of determining the best mitigation strategy.
Single phase liquids and gases
Fouling in these services occurs from deposition of particles. Some don’t undergo any chemical change after deposition (inorganics, already-formed coke), others will be subject to a conversion – typically, organic particles which will form coke-like material. Deposit analysis tells us if the particles are of the former or latter variety. If one type dominates (>80% of the deposit, say) then we look for its source and try to address the issue there, if both types are present we have two or more sources to contend with. The feed (fluid coming into the heat exchanger) can be tested for unexpected material, especially inorganic compounds which are not part of the process.
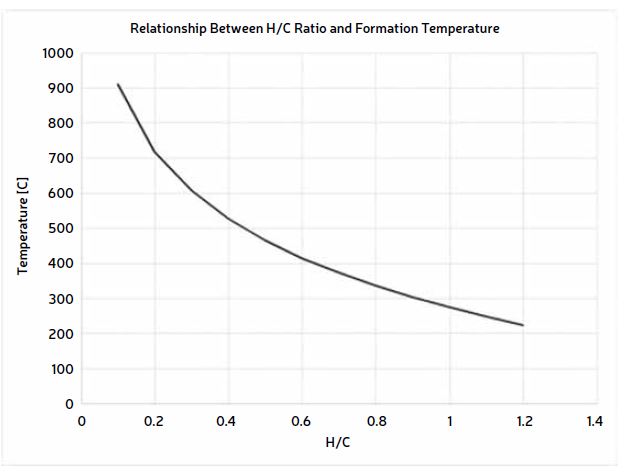
As examples: Iron sulfide implies that corrosion, somewhere in the flow circuit, is responsible; Catalyst particles are carried over from an upstream reactor; Coke (H/C < 0.70) comes from an upstream high temperature source such as a fired heater or a hot distillation column; Salts could be inherent parts of the process or could imply an inefficient desalting process. For organic material with H/C between 0.80 and 0.95, the mechanism is that of deposition plus conversion in the heat exchanger itself.
The deposition process is part of the fouling mechanism and it is controlled by the fluid shear stress at the wall. Thus, the typical mechanism is that of the presence of particles, their deposition at a rate determined by the shear stress, and thermal conversion of some of those particles.
Boiling/reboilers
Deposit analysis will confirm whether the fouling is due to the most common mechanism of a wet-dry wall (in which case the deposit will be largely organic), or due to deposition of carryover material (expected to be inorganic).
If organic, there are several ways to understand the mechanism: (1) Test the feed for precursors which typically will be polymeric material or precursors to polymeric material (e.g., dienes). (2) Simulate the operating conditions with a good heat exchanger software tool to determine if the wall temperatures are high enough to have film boiling and enhance the fouling mechanism. This information should be combined with an understanding of the feed material – does it tend to polymerize in a certain temperature range? (3) Visually inspect the fouled tube bundle which may show that fouling is localized in certain zones, especially areas where the wall temperature is the hottest. This is easier to see on the shell side.
A similar approach applies to heat exchangers that are not classified as reboilers but vaporize the feed to a process unit. These feeds may contain organic precursors which form polymers which deposit and convert to coke-like material. A deposit analysis confirming whether the fouling is organic, a test of the feed for the suspected precursors, and verification using the H/C ratio (see later in this article), helps to understand the fouling mechanism
Overhead condensers
Here again, deposit analysis will confirm whether the foulant is precipitated salts or other inorganics, such as corrosion products, carried over from the top of the distillation column. It is possible to have some organics mixed in with this material, but that is not what usually drives the fouling.
Once the material is identified, a simulation can help to know whether the right wall temperature conditions exist for salt precipitation, and if such conditions are localized. A visual inspection of the tube bundle will also identify areas where deposits preferentially accumulate. If an aid such as a water wash is used to try to dissolve salts, localized fouling will indicate that the water isn’t able to get to those areas.
Sometimes vapor phase effluent from a reactor is condensed in heat exchangers. A similar mechanism of salt precipitation (depending on the cold tube wall temperature) is usually applicable in these cases.
Use of the H/c ratio
In Part 1 of this series we defined “Coke” and “Coke-Like” material based on the atomic H/C ratio. The significance of this indicator is that it can be used to identify the temperature to which the organic portion of the deposit was exposed, and to relate that to the fouling mechanism. Referring to Fig. 1, if the H/C ratio of the deposit is 0.40 the coke was formed at a temperature of approximately 520 C.
Since the temperatures in heat exchangers are much lower, we know that the coke came from an upstream furnace, reactor, or column. On the other hand, if H/C=0.83 (as in the example in Part 2) then the corresponding temperature is about 320 C, and if the heat exchanger operates in that temperature range, we know that the coke-like material was formed in the heat exchanger (deposition of organic precursors followed by thermal conversion).
Summary
A combination of deposit analysis, knowledge of what is in the feed, and heat exchanger operating conditions can be used to determine why and how a heat exchanger fouls. Precursors in the feed, the higher tendency to deposit due to low wall fluid shear, temperature conditions which favor film boiling or salt precipitation, localized high temperatures and low velocities, all contribute to the fouling mechanism. Once we identify the responsible conditions and the source of precursors, we can think of what steps can be taken to mitigate the fouling and to minimize its economic impact.
Catch up on fouling focus!
Have you missed the earlier installments of this multi-part series? All articles are available in our online archive:
Catch up on Fouling Focus!
Have you missed the earlier installments of this multi-part series? All articles are available in our online archive:
Part 1 – https://heat-exchanger-world.com/heat-exchanger-fouling-in-practice-understand-mitigate-1/
Part 2 – https://heat-exchanger-world.com/heat-exchanger-fouling-in-practice-understand-and-mitigate-part-2/
Part 4 – https://heat-exchanger-world.com/heat-exchanger-fouling-in-practice-understand-and-mitigate-part-4/
Part 5 – https://heat-exchanger-world.com/heat-exchanger-fouling-in-practice-understand-mitigate-part-5
Upcoming in parts 4 & 5
In the next two articles we will look at different fouling mitigation techniques – hardware solutions and good design practices.
About the author
Himanshu Joshi retired from Shell in 2021 after 34 combined years with ExxonMobil and Shell, during which he specialized in heat exchangers and fouling. He was part of a team that was granted a patent related to fouling deposit analysis at ExxonMobil, and led applied fouling R&D projects at both companies. He has made several presentations about the field aspects of fouling and fouling mitigation, and deployed many mitigation technologies in the field. He can be reached by email at alph.hmj@gmail.com.