Cleaning methods and economics
In this series of articles we will look at how heat exchangers foul, how to understand the root causes of fouling, and how to mitigate the impact of fouling. The material presented is based entirely on the author’s experience and analysis of operating situations in the Oil & Gas industry. However, many theories and varied experiences exist across the industry and amongst researchers.
By Himanshu Joshi, Heat Exchanger Specialist
Cleaning of fouled heat exchangers is an important action in minimizing the cost of fouling. Many cleaning methods are available and there is a large difference in their costs and cleaning effectiveness. When the heat duty loss due to fouling is large and has high economic impact or when the cleaning itself is relatively expensive, a consideration of the total cleaning cost, including the cost of an ineffective cleaning, will aid in selecting the optimum method. This article will provide an overview of three cleaning methods, all the costs involved, and an example of the cost of ineffective cleaning.
Cleaning Methods
Hydroblasting: This is the traditional method of using high pressure water to dislodge foulant off the tube surface. It requires the extraction of the tube bundle from the shell and disposal of the used, contaminated water. One major disadvantage of this method is that it may not be able to get a heat exchanger to a zero-fouling condition, often because the water may not reach all the fouled surfaces with a sufficient force.
Chemical Cleaning: This method uses circulation of chemicals, oil or water based, to remove foulant partly by dissolution and partly by mechanical force. It has a few advantages over hydroblasting – the bundle doesn’t need to be removed from the shell, multiple heat exchangers can be in the circulation loop, and the tube and shell sides can be cleaned concurrently with the same circulation. However, there is a large variation possible in the cleaning procedure, from a low-cost, short duration, low flow process to a high flow, long duration and correspondingly high-cost procedure. Experience shows that the high-end chemical cleaning matches the cleaning effectiveness of hydroblasting and costs about the same per heat exchanger if multiple heat exchangers are cleaned. This method requires piping work and external equipment (such as pumps, filters) to manage the circulation, and the disposal of the used chemical waste.
Ultrasonic Cleaning: The tube bundle is put in a water bath, with added chemicals, and cleaned using the force generated by ultrasonic bubbles on the tube surface [Ref. 1]. It combines the advantages of hydroblasting and chemical cleaning but with a shorter duration in the cleaning bath. This method results in a higher cleaning effectiveness compared to the other two, as will be shown later in this article. Table 1 shows a summary of the important aspects of the three methods. The Cleaning Effectiveness is expressed as a percentage of the heat duty right after cleaning compared to what it should be for a zero fouled heat exchanger (100% reflects a fully clean or zero-fouled condition); the Relative Total Cost includes all the costs associated with cleaning (see Table 2); and the Cleaning Duration shows the time of the actual cleaning operation – time of chemical circulation, time of hydroblasting, or time in the ultrasonic cleaning bath.
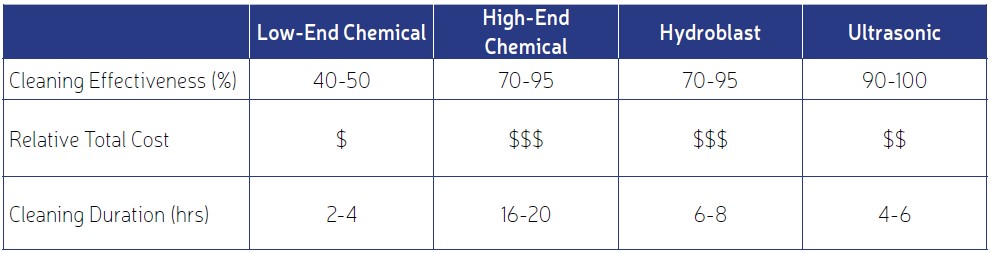
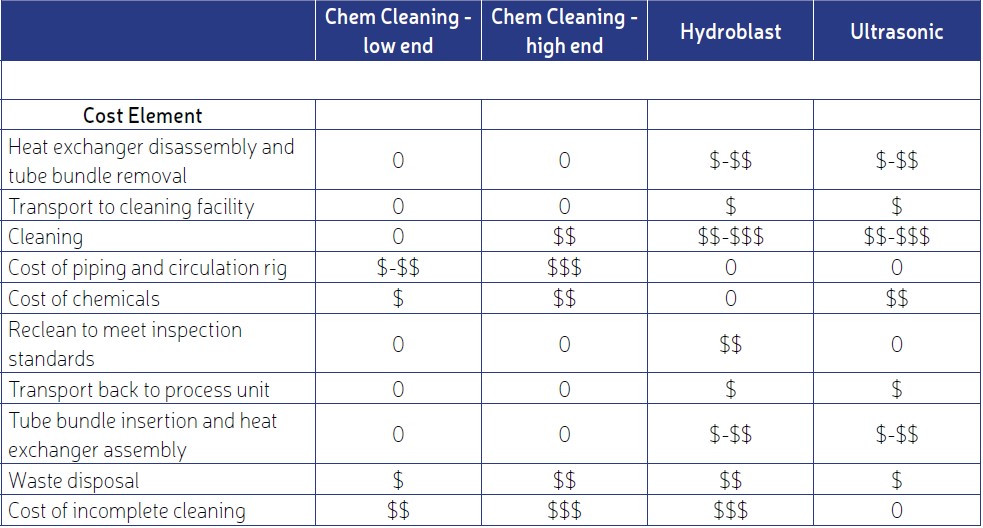
Cleaning Costs
Besides the cost of what the cleaning contractor gets paid, there are several other components that must be considered to arrive at the total cost of cleaning. Table 2 lists the different costs and their relative magnitudes, with a zero indicating that cost is not applicable for that method. Note that costs vary with time and especially with location. This table can be used as a guide to ensure no costs are missed when making decisions about when to clean and how to clean – two which might escape attention most often are the cost of incomplete cleaning, and the cost required for a repeat cleaning to meet inspection cleanliness requirements. Also, chemical cleaning can be used on more than one heat exchanger simultaneously which results in a lower per heat exchanger cost. We see that chemical cleaning has no costs for tube added costs for making piping connections and for the chemicals. It is also possible that chemical cleaning may cost less than shown on a per heat exchanger basis depending on the equipment and procedures used. We also see that recleaning costs on average can be high for hydroblasting but zero for the other methods, and the cost of waste disposal is low for Ultrasonic cleaning because it reduces the waste produced by about 75%. Most importantly, note that the cost of incomplete cleaning can be high for hydroblasting and chemical cleaning, but is zero for Ultrasonic.
Table 3. Data for cleaning effectiveness.
Cost of Incomplete Cleanings
An incomplete cleaning is where the performance of the cleaned heat exchanger falls short of a 100% clean state. In terms of heat duty this means that the actual heat duty right after cleaning (Qa) is less than what you would expect from a heat exchanger with zero fouling (Qc), so (Qa/Qc) < 1.0. Table 3 [Ref. 1] shows analysis results from operating heat exchangers after a hydroblast and after an Ultrasonic cleaning. Each row is for the same heat exchanger, with operating data simulated after each type of cleaning. The average cleanliness is higher by about 15% for ultrasonic cleaning. The economic impact of that deficit is shown below.
Simulations of two heat exchangers, assuming a high fouling crude as the fouling fluid, were performed to evaluate the impact of incomplete cleaning. Fig. 1 is for a heat exchanger with a surface area of 500 m2, and Fig. 2 for 875 m2. The figures show the heat duty degradation due to fouling over a one-year period. Qa is the heat duty starting with 100% clean, Qa’ is starting at 85% clean, and the area between the two curves is the loss due to incomplete cleaning. The loss in Fig. 2 equals 3,250 MWh and in Fig. 3 it is 11,620 MWh. Using $2.84/GJ for energy and $8.40/ton for CO2, the MWh values give costs of $40k and $140k for the two heat exchangers. These results were presented in detail in [Ref. 2]
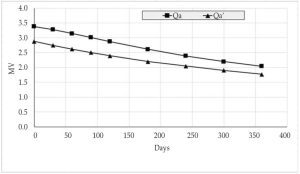
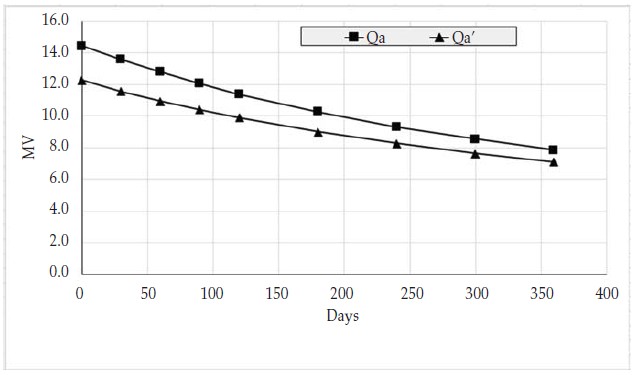
Summary
Heat exchanger cleaning can be accomplished using various methods and with a range of costs and effectiveness. To minimize the cost of cleaning requires accounting for all related costs, not just what is paid for the cleaning activity. One cost which may often be overlooked but can be quite significant is that resulting from decreased performance due to an incomplete cleaning.
Upcoming in Part 7
In the next article we will take a detailed look at the mitigation methods for the best return.
References
[1] Kieser, B. N., et. al., The Economic Impact of Better Heat Exchanger Cleaning on an Oil Refinery – Theoretical, Expected and Actual Results, Heat Exchanger Fouling & Cleaning Conference, Wagrain, Austria 2022.
[2] Joshi, H. M. et. al., The Economics of Heat Exchanger Cleaning and the Cost of Incomplete Cleaning, Heat Exchanger World Conference & Expo, Pasadena TX USA, October 2023
Catch up on Fouling Focus!
Have you missed the earlier installments of this multi-part series? All articles are available in our online archive:
Part 1 – https://heat-exchanger-world.com/heat-exchanger-fouling-in-practice-understand-mitigate-1/
Part 2 – https://heat-exchanger-world.com/heat-exchanger-fouling-in-practice-understand-and-mitigate-part-2/
Part 3 – https://heat-exchanger-world.com/heat-exchanger-fouling-in-practice-understand-and-mitigate-part-3/
Part 4 – https://heat-exchanger-world.com/heat-exchanger-fouling-in-practice-understand-and-mitigate-part-4/
Part 5 – https://heat-exchanger-world.com/heat-exchanger-fouling-in-practice-understand-mitigate-part-5/
About the authors
Himanshu Joshi retired from Shell in 2021 after 34 combined years with ExxonMobil and Shell, during which he specialized in heat exchangers and fouling. He was part of a team that was granted a patent related to fouling deposit analysis at ExxonMobil, and led applied fouling R&D projects at both companies. He has made several presentations about the field aspects of fouling and fouling mitigation, and deployed many mitigation technologies in the field. He can be reached by email at alph.hmj@gmail.com.
About this Technical Story
This Technical Story was first published in Heat Exchanger World Magazine in March 2024. To read more Technical Stories and many other articles, subscribe to our print magazine.
Technical Stories are regularly shared with our Heat Exchanger World community. Join us and share your own Technical Story on Heat Exchanger World online and in print.