Calculation of shell-and-tube heat exchangers
By Dipl.Ing. D. Fischer, Managing Partner – Lauterbach Verfahrenstechnik GmbH
Can software replace the expert engineer?
“Do what I mean”: this demand for calculation software sounds tempting. It means the minimization of the default values by standardized default values; but be careful! Is this not the hidden lack of expertise of the user? Unconditional trust in a calculation left to “others” should not lead to uncritical acceptance of the results, as this would bypass the important “four eyes principle”. Every engineer must know that HE is the interface to the program and must assess the result with his expertise, but can also influence it in any direction. A wide variety of software is offered for the calculation of tube bundle heat exchangers. The hydraulic and thermal relationships are known and published e.g. in the VDI Heat Atlas. The heat transfer equations for the tube and shell side based on measured data describe the heat transfer quite accurately. The accuracy of the hydraulic and thermal calculation of a complete shell-and-tube exchanger is given as +- 15%, which is also valid for the LV Design Atlas 10. By checking the input values by the program and messages indicating limit values, the user always obtains a functional exchanger. But is it at the optimum? However, warnings such as “window size too small” should definitely be taken into account in the first step. Only experience allows to optimize the interpretation of indications and results.
There are things for which the user is solely responsible
Fouling factors
Heat exchangers where fouling occurs are designed with a fouling factor. This factor is chosen in such a way that the exchanger provides the necessary power at the end of the minimum running time. Fouling factors have a great influence on heat transfer and can cause an increase in area of up to 50%. This far exceeds the accuracy of the thermal calculation. In many cases, the operator has determined these factors for their applications themselves from operational data and does not leave it up to the provider.
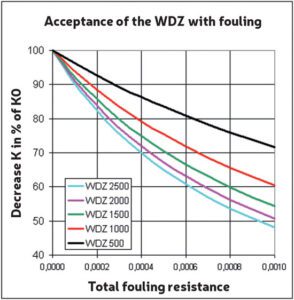
Physical Properties
The greatest influence is exerted by the viscosity, especially when cooling higher viscous media. If a shell-side heavy oil is cooled with relatively cold cooling water, a region may form in the bundle where the viscosity is so high that the medium is displaced from the bundle and flows across the gap between the bundle and the shell and no longer participates in heat exchange. You should only know this.
As calculated – this is how it must be built
If the calculated dimensions are not adopted in the fi nal design, the exchanger may, in the worst case, not perform as desired. This applies especially to the dimensions of the shell side, such as the design of the tubesheet and the baf-fl es. The shell side often determines the exchanger size due to the greater resistance.
Vibrations
The hydraulic design is associated with the tendency to vibrations that can occur on the bundle of the exchanger and lead to damage cases. Here, the engineer’s decision
is doubly challenged, because the avoidance of vibrations interferes with the geometry of the shell side and thus infl uences the heat transfer. The LV Design Atlas10 verifi es a pending need for action by rigorously considering all bundle areas, the engineer must incorporate the necessary changes into the design.
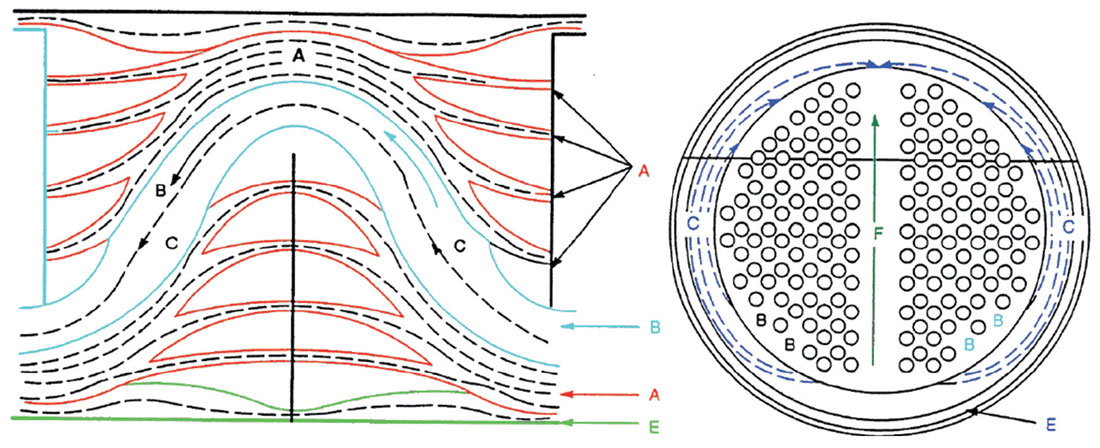
About the company
Lauterbach Verfahrenstechnik GmbH has been developing software for pressure vessel design and heat exchanger design since 1978. The company’s goal is to support the user with suitable software tools. The correct handling of the freedoms offered by versatile software, which can optimally influence the result, requires experience; this experience can be gained through many projects or through practical seminars.