
In this article, global leader in heat transfer solutions, Kelvion, demonstrates the benefits of modular heat exchangers across a range of applications. With its innovation K°Flex as an example, the company proves how modular systems improve efficiency, enable lower heat temperatures, and offer flexibility during the design process.
Text and images courtesy of Kelvion
Increase process efficiency
When it comes to return on investment, modular heat exchangers are generally superior to custom-made solutions. The K°Flex type from Kelvion Thermal Solutions is a good example of how they can also convince in terms of efficiency and versatility. The product is based on plate packs whose geometry combines the advantages of shell-and-tube and plate heat exchangers. It offers advantages for standard tasks as well as for retrofit projects or the extraction of low-temperature heat. And it can even be used for multi-fl uid systems.
The K°Flex heat exchanger is a modular design based on embossed plates fully welded to plate pairs. Typical applications for this type of heat exchanger are condensation or evaporation and heat transfer between single-phase media. The embossed plates form asymmetric channels, shaped like tubes on one side and waves on the other side. They combine the advantages of shell-and-tube and plate heat exchangers in one unit. From one side, the medium flows through tubes of 6 or 9 mm diameter. The other medium flows through a compact plate structure whose embossing induces better turbulences – in other words, very good heat transfer.
Large cross-section for low pressure losses
The medium flowing through the straight tubes passes through the heat exchanger over a short distance without any obstacles, which allows high volume flow rates with low pressure losses and is also advantageous for two-phase media. The large tube diameter not only has a positive effect on condensation under vacuum, but also makes it possible to use more viscous media or media contaminated with particles without fear of rapid fouling or clogging of the heat exchanger. Typical cleaning-in-place systems are sufficient for cleaning.
The embossed plates are welded together to form plate pairs, which are then assembled into standardized, rectangular modules. In the next step all modules are connected to bigger plate packs, whereby a plate pack can have several rows and layers. Even multiple plate packs can be arranged in bigger so-called plate pack towers. Thanks to the option of arranging several layers in a plate pack, flow directions such as cross-and-counterfl ow are also feasible, in addition to the simple crossflow configuration. In this way, the respective thermodynamic requirements can be considered.
Multi-fluid systems
Since the layers of the plate packs are hydraulically separated from each other, the K°Flex can also be used to construct multi-fluid heat exchangers, such as those used in the oil and gas industry. For example, a medium that needs to be cooled or heated over a wide temperature range can transfer heat step by step within the same heat exchanger, against different media adapted to the respective temperature levels.
For example, hot exhaust gas could be run against two different cooling media to bring it to the desired target temperature. A cascade of several heat exchang-ers would thus be unnecessary, reducing investment costs. Another multi-fluid application would be to use a hot product to simultaneously heat different process fluids.
A complete, ready-to-connect heat exchanger consists of a plate pack, or a tower formed from several packs in a compact housing or in a circular vessel. In this way, heat exchangers with an effective area of up to 12,000 m² can be implemented in a single unit. Theoretically, units up to 40 meters in height are possible; the highest solution manufactured by Kelvion to date reached a height of about 20 meters. For occasional manual cleaning and inspections, the large housings are provided with openings or manholes.
Depending on the material and design, K°Flex is suitable for temperatures up to 550 °C, and even higher for special designs, as well as for pressures on the corrugated plate side up to 100 bar. The standard K°Flex modules can be used for media at temperatures of up to 300 °C and pressures of up to 30 bar, which are often desired in green energy applications or the petrochemical industry.
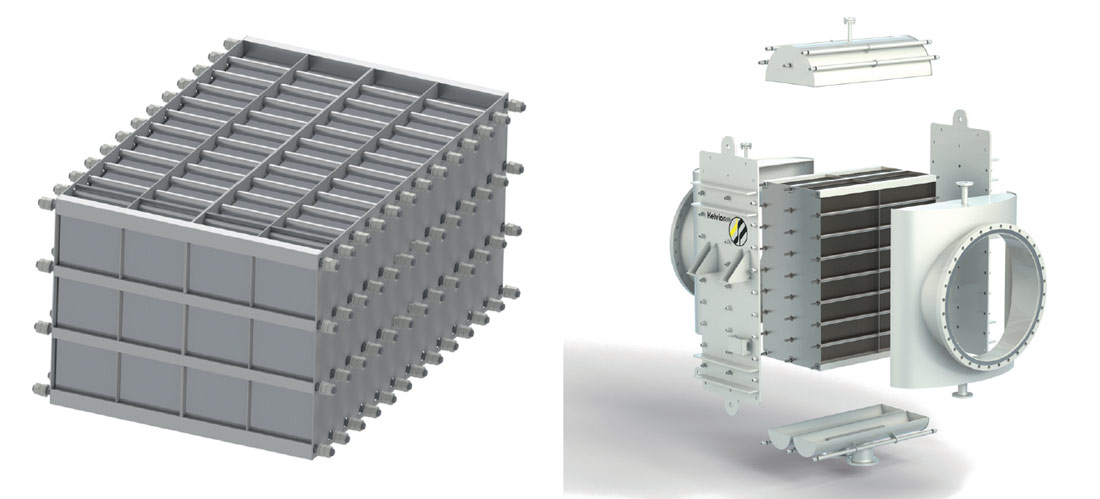
Performance gain during refurbishment
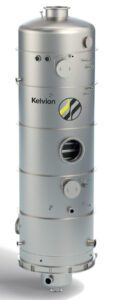
Modular solutions are also suitable for revamping: existing older tubular heat exchangers are often replaced by new, more compact solutions due to their wear or for the purpose of increasing capacity or efficiency. This has proven successful, for example, with Robert evaporators or tubular falling film evaporators, such as those used in the sugar industry. When the heat exchanger is replaced by K°Flex plate packs, the outer vessels can continue to be used, so that only the heat transfer surfaces and other internals need to be replaced.
Thanks to the use of the plate packs, the heat transfer surface can be increased significantly without changing the dimensions of the outer vessel. Depending on the vessel diameter, the surface area can be increased by 200% – 300%. Added to this is the higher heat transfer coefficient of the new solution. Depending on the initial situation, improvements in heat transfer of 50 %, sometimes even a doubling, are possible. Together with the increase in surface area, this leads to a multiplication of the thermal performance – and this with identical external dimensions and lower overall weight of the new heat exchanger. In the case of a cascade of heat exchangers, such as a multi-effect evaporator station, it is therefore often possible to increase the number of effects after refurbishment while maintain-ing the same initial conditions, thus achieving significantly greater efficiency – and thus lower steam demand – of the overall system.
High efficiency enables low-temperature heat
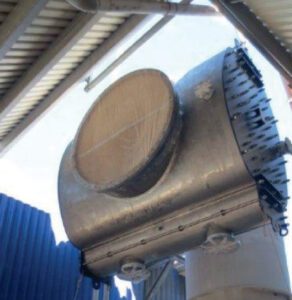
In the past, low-temperature heat that could not be used economically was often discharged to the environment. However, with modern and efficient heat exchangers, high heat transfer rates and low differential temperatures between the media are feasible, making heat recovery and utilization at a much lower temperature level more economical than in the past. An example of this is the use of residual heat in a waste incineration plant. In this plant, residual heat is generated from vacuum vapors that were previously removed with air-cooled condensers. In a Kelvion retrofit project, this waste heat was harnessed to heat tomato greenhouses.
With very limited space available in the waste incineration plant, the compactness of the K°Flex heat exchanger proved to be a significant advantage. The vacuum condenser installed under the roof of the plant has an overall height of not quite 2.5 m and provides a heat transfer surface of more than 1000 m². Similar solutions are also conceivable for processes in chemical plants where, for example, water vapor or process steam is generated under vacuum conditions and can be used by vacuum condensers to recover residual heat.
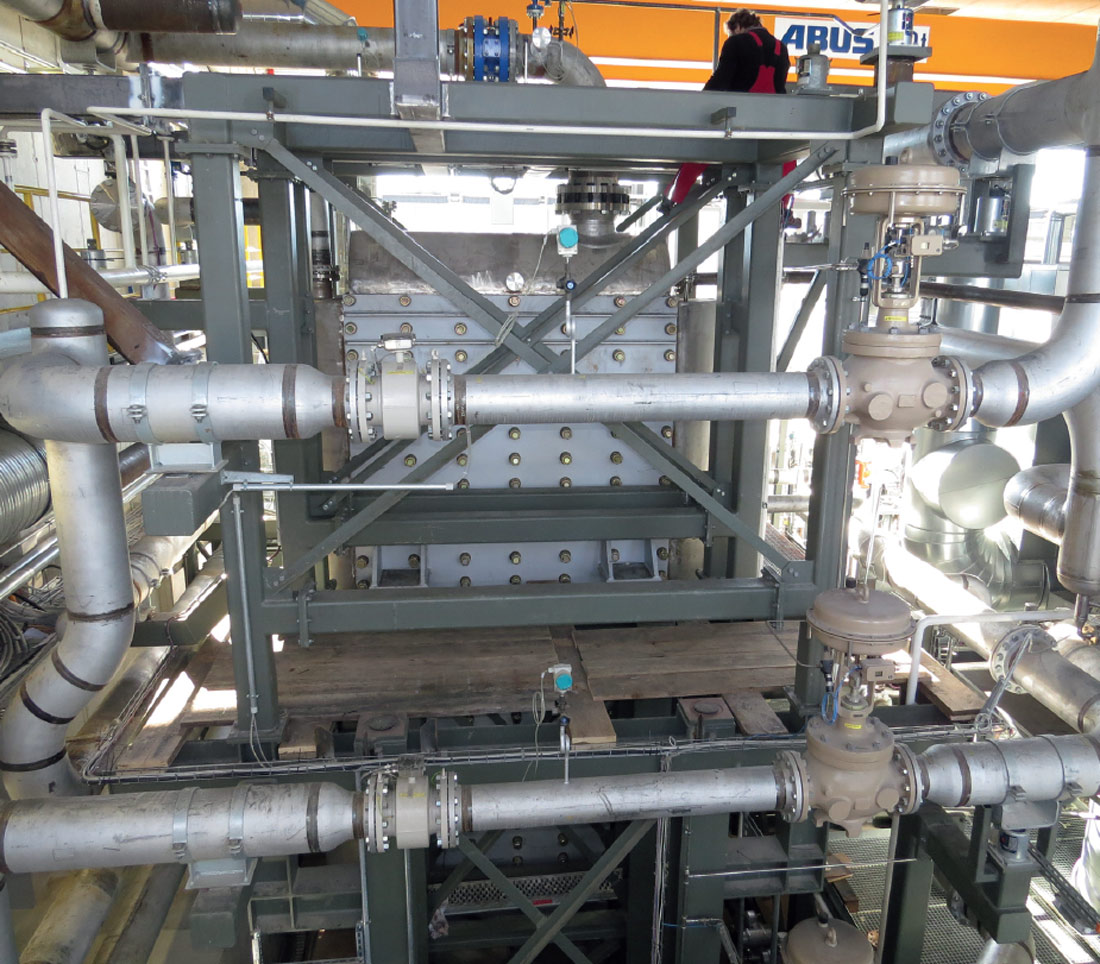
Combination of different thermal zones
For many fully standardized heat exchanger types it will become very difficult to integrate different thermal requirements in a single heat exchanger. As a consequence, a series of heat exchangers with different thermal functions based on different design parameters are often installed. Another option is to combine different thermal functions into one single heat exchanger, consisting of different thermal zones, either for the hot or cold side. In the K°Flex heat exchanger installed as an evaporator in the Kalina Cycle within a geothermal power plant in Germany, different zones are considered to fulfill several thermal functions. In the bottom zone a subcooled liquid is heated up following a partial evaporation zone. In the top zone the maximum evaporation duty is reached, and fluid phases can be separated, if required. Following a non-linear evaporation curve with smallest temperature differences, a multipass arrangement on the hot side is required and adjusted to the evaporation curve to gain the best temperature approach. One K°Flex heat exchanger is separated into the different thermal zones. The demand for higher thermal duty with smallest temperature approach requires a larger heat exchange surface, which is spread over several modules.
Conclusion
K°Flex from Kelvion Thermal Solution is a fully welded plate heat exchanger. The modular design concept allows the fabrication of large sized heat exchangers from modules. This makes the design approach much more flexible for all kinds of thermal applications, especially for condensation and evaporation duties. Even the biggest units are operating as plate falling film evaporators. The concept of the plate packs and housing is flexible and can be adjusted to limited space requirements and individual client demands. Thus K°Flex offers the advantages of a fully welded plate heat exchanger with a flexible design approach proven in many industries: such as a vacuum condenser in waste incineration plants, an evaporator in geothermal power plants, and a plate falling film evaporator in sugar factories.