Covid, the war in Ukraine and an energy shortfall in Europe (especially Germany) are all factors driving up the price of natural gas and stimulating demand for LNG. The USA has emerged as a leading LNG exporter, with Europe as its principal market. The demand for LNG as ship fuel continues to grow, stimulating the development of bio-LNG, which can be produced in countries lacking natural gas reserves.
By James Chater
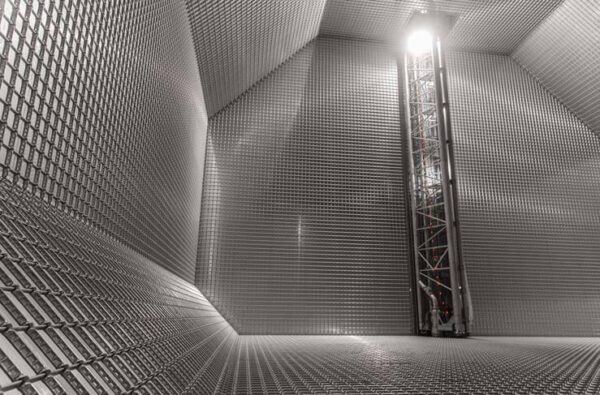
Outlook
Poor Europe! In the months before February 2021, gas prices in Europe hovered around 10 USD per million btu, with US prices shadowing them at an average of 5-7 USD lower. From February 2021, however, a gap started to open, widening still further after the invasion of Ukraine.
Eventually, European prices peaked at 70.04 (August 2022; the price has since fallen back), whereas the US price rose to only 8.79¹. As if this were not galling enough, on 26 August 2022, the day the Nord Stream pipelines were ruptured, prices in Europe surged, whereas the American price barely moved².
The timing of this parting of ways shows that the enormous price rise is due only in part to the war in Ukraine. The other factor was a surge in demand due to post-Covid economic recovery and a lack of capacity, especially of LNG carriers. And when it comes to LNG, the liquefaction, transport/storage and regasification processes are risky and complex, requiring large upfront investments, so it is bound to be more expensive than piped natural gas.
Transport
If the winter is severe, there are fears of power cuts and expensive heating bills, especially in Europe. But the problem is not the lack of gas, it is the lack of ships. To replace the gas being piped from Russia, consumers are turning to LNG. This means that LNG carriers are oversubscribed: they are reported to be booked up well into the second half of the decade, and contracts have soared in price. This tight market has occurred even though new LNG carrier construction yards have recently come on stream in China (Dalian, Jiangnan, Yangzijiang), challenging South Korean dominance. Another problem is that out of the 640-ship fleet worldwide, as many as 400 need to be refurbished to curb their emissions because they are diesel-powered and lack boil-off systems.
The transport markets (HGVs and ships) are growing even as end users face ever more stringent standards regarding pollution and CO2 emissions. Shipbuilders are receiving a deluge of orders for both LNG-powered containerships and LNG-powered LNG carriers. Most of these are of the dual-fuel type, allowing ships to switch between diesel and LNG. LNG carriers also use a system that allows boil off gas (BOG) to be used as fuel. A hybrid power system with battery storage also exists: already used in smaller vessels such as ferries, these are now being extended to LNG carriers.
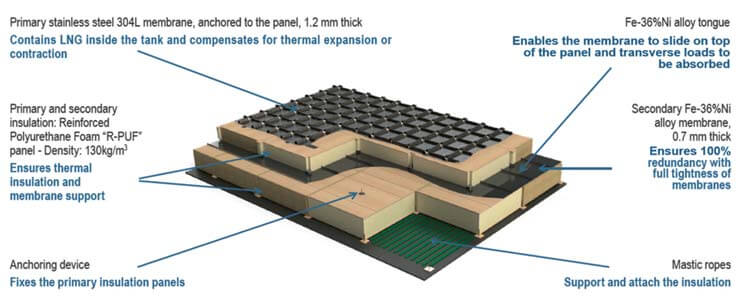
A newer technology is the solid oxide fuel cell, which a Shell-led consortium is testing on an LNG carrier. In LNG carriers, the predominant containment system is the GTT Mark III Flex system. This has been in use for several years but will soon be superseded by GTT NEXT1, designed to increase thermal performance and ensure a boil-off rate of less than 0.07%V/d. It is made up of a primary and a secondary metallic membrane, made of 304L and Fe36%Ni, respectively, both supported by a layer of insulating foam material.
LNG propulsion is a market for LNG that competes with electricity and heating gas. However, this pressure is being relieved by the development of bio-LNG and synthetic LNG, which for the first time, allows the production of LNG in regions that have no natural gas reserves. Bio-LNG (or liquified biomethane – LBM) is developed from existing biomass and waste and can be blended with LNG with no changes necessary to the vessel’s structure. Many projects are underway: plants are being built by Storengy/CM Fluids and REEFUELERY in Germany, AS Agrofirma Tervete in Latvia (using Wärtsilä technology), HAM/ CycleØ in Chile, and – largest of all – Titan’s plant in the Port of Amsterdam, the Netherlands.
Looking further into the future, synthetic LNG (also known as SNG or e-LNG) is viable once sufficient renewable electricity is available. To make SNG, hydrogen produced by electrolysis is reacted with CO2. The gas is cooled down in a heat exchanger, turning the CO2 to ice at -150°C. The remaining methane-hydrogen mixture is cooled further until the methane liquefies at -163°C. The hydrogen that is left remains gaseous and is returned to the methanation reactor. In October 2021 the ElbBLUE was the first ship to sail with synthetic LNG.
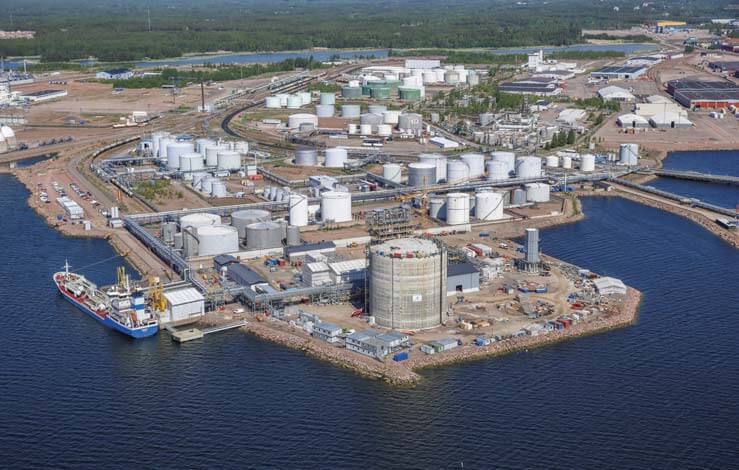
Nord Stream sabotage
The sabotage of the Nord Stream pipelines is one in a series of pointlessly destructive acts that have characterized the Russian-Ukrainian conflict since its beginning. The damage to the two lines was caused by three explosions on 26 September 2022. The pipelines, owned by Gazprom, were not operating but were filled with natural gas. Whoever conceived this act is responsible not only for the extensive damage to infrastructure but also for the environmental harm caused by the massive release of methane. The steel pipes, after being exposed to corrosive saltwater, will have to be replaced. The repairs, if they occur, will take several months. But there are always winners: demand for LNG will rise in the short and medium term, and it could well be that oil and gas imports from Russia will never be resumed.
Exports
By the end of 2022, the USA will have the world’s largest LNG capacity. About 71% of its exports go to Europe, the top destination being the Netherlands. Exports to Europe were being stepped up even before the war in Ukraine, and President Biden’s promise of an additional 15 cu m of LNG for Europe this year is likely to be surpassed. US export capacity has expanded rapidly since November 2021, with new trains at Cheniere Energy’s Sabine Pass and Venture Global’s Calcasieu Pass. Cheniere is planning two more trains and a storage tank at Corpus Christi, with construction slated for 2024-2031. The Cameron LNG expansion in Louisiana has been awarded to JGC America and Zachry Industrial, who will add a fourth train.
In Mozambique, Baker Hughes has secured a new service contract for Eni’s Coral Sul FLNG. The FLNG will be ready to achieve its first LNG cargo in the second half of 2022, adding Mozambique to the LNG-producing countries. Eni is also working on a second FLNG, which will likewise be located offshore Mozambique. Tanzania is also mulling an LNG project with a consortium of Shell, ExxonMobil, Equinor and Ophir Energy. A final investment decision is expected in 2025.
In the Middle East, QatarEnergy is engaged in an ambitious expansion of North Field East and North Field South, both of which source LNG liquefaction. The country’s LNG output is expected to expand from just under 80 to 126 metric tonnes per annum by 2027. Four new LNG trains will be constructed. Shell, Totalenergies, Exxon Mobil and Eni are all investors. After a huge build-up of its export capacities in recent years, Australia faces a gas shortage! Australia allows so much LNG to be exported that it has neglected its own needs. Australia considered export curbs last summer, before ruling them out.
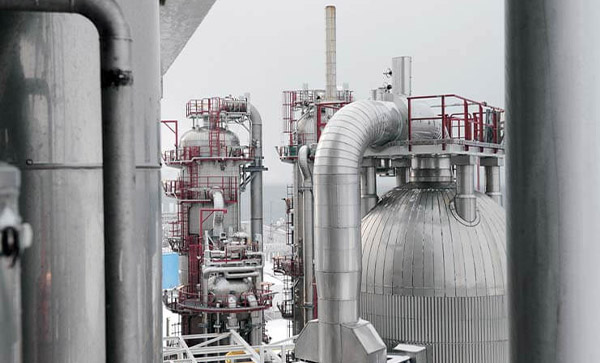
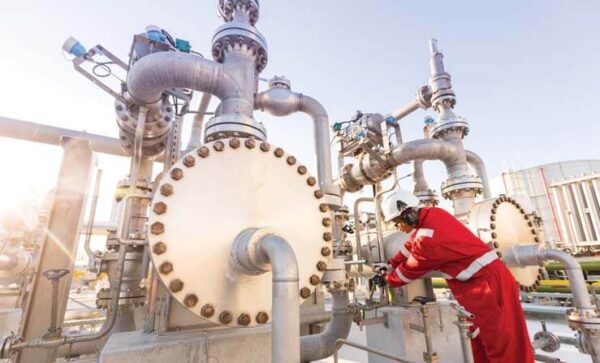
Imports
The European market is so needy that ships are facing long delays in offloading their LNG because of a dire shortage of terminals. This bottleneck shows the urgent need for a new import terminal and Floating Storage Regasification Unit (FSRU) capacity. In Germany, construction work has started on the LNG jetty at Stade earlier than originally planned, so first gas will flow in 2023 rather than 2026. Likewise, the Wilhelmshaven terminal, approved in 2022, is expected to become operational in late 2022 or early 2023. The Brunsbüttel terminal will start operating in 2026. Other projects are planned or underway in Croatia, Finland, Greece and Italy. As many as 25 new FSRUs are expected to be deployed in Europe, with the Netherlands expecting its first unit to start in 2022.
Europe’s main competitor for LNG is Asia. New terminals and FSRUs are being proposed or planned
in China, India, Indonesia, Myanmar, Pakistan, the Philippines and Thailand. Vietnam is building its LNG terminal at Son My. In Pakistan, Excelerate and Engro are exploring a possible joint project.
Materials
If there is one material that is indispensable in LNG production, transport and storage, it is nickel. It is the common denominator for such stainless grades as 316 and 304, and it is used in nickel-iron alloys (5%, 9%) as well as in Invar. It is essential for cryogenic applications in which resistance to extremely cold temperatures and temperature fluctuations is required.
The price of nickel has been rising for some time, even spiking 60% in one day in March, bringing it to 40,000 USD a tonne. Russia supplies about 6% of world production, and the war in Ukraine has spooked traders.
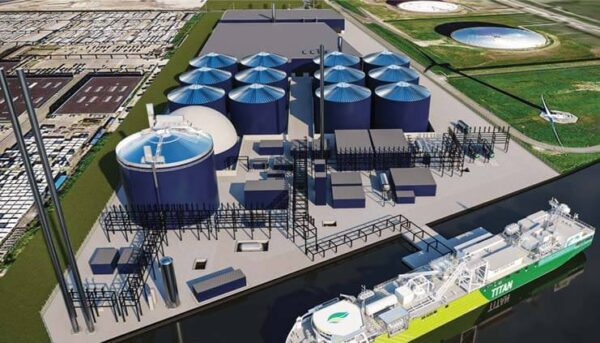
In this context, the arrival of Posco’s High Manganese Steel (about 25% manganese) is welcome. It can replace 9% Ni in LNG carriers and LNG-fuelled ships. A recent example of its use is in the LNG fuel tank of a DSME-built crude-oil carrier. It has lower price and higher strength than competing materials and performs well in cryogenic temperatures.
In the purification process, duplex stainless steels or nickel alloys are used in valves exposed to low temperatures and saltwater. Valves in cryogenic service are usually made of 316, but other metals such as nickel-aluminium-bronze are often used.
Heat exchangers and LNG:
The main heat exchangers used in gas liquefaction process trains are: plate-fin heat exchangers (PFHEs) and spiral-wound heat exchangers (SWHEs). These types of exchangers have large internal surface areas consisting of a large number of heat exchanger cores or circuits. These designs can achieve a close temperature approach between the refrigerant and the natural gas in the liquefaction cycle.
However, with today’s technology, there is a limit on the heat exchanger size. A single pfHE can typically be designed to liquefy about 1.5 MtpA of lng. Higher capacity would require multiple exchanger cores grouped together to provide the heat exchange areas. on the other hand, a single SWHE can typically be designed for 4 MtpA of LNG.
PFHEs, often referred to as brazed aluminum heat exchangers (BAHXs), consist of aluminum fins. PFHEs can be configured with different flow configurations: cross-current, parallel, and multipass directions. This type of heat exchanger is also very common in the ngl recovery unit to achieve high recovery.
SWHEs, or spiral (or coiled) wound heat exchangers, are designed with a greater internal heat transfer area and therefore can operate with a larger temperature gradient. In addition to the larger surface area, the other advantage of the SWHE is its higher proven tolerance to thermal shocks. However, because of the fixed heat exchange configuration, the exchanger design has a limited flexibility to handle different feed gas compositions.
(source: Handbook of liquefied natural gas, 2014)
About this Featured Story
This Featured Story was first published in Heat Exchanger World Magazine in March 2023. To read more Featured Stories and many other articles, subscribe to our print magazine.
Featured Stories are regularly shared with our Heat Exchanger World community. Join us and share your own Featured Story on Heat Exchanger World online and in print.