Miguel Gutierrez is a field consultant engineer at Saudi Aramco, based in Saudi Arabia. Miguel’s role is vast and varied, encompassing all angles of stationary equipment support. We spoke with Miguel to gain his insights on the dynamic challenges and advancements in heat transfer technologies within the oil and gas sector.
By Iryna Mukha, Heat Exchanger World
Miguel draws from a background as a stationary equipment engineer with a degree in mechanical engineering to fulfil an extensive and varied role. “I started working in the oil and gas industry in 1992, the same year I graduated. I have more than 30 years of experience working mostly as a stationary equipment engineer. I spent most of my career at Saudi Aramco providing technical support to Ras Tanura refinery,” says Miguel. He has been working at Saudi Aramco for 18 years, currently serving as a field engineering consultant in the area of stationary equipment, which involves heat exchangers, pressure vessels, piping, valves, among some others.
What are some of the challenges your company is experiencing with heat transfer?
“The majority of the issues that affect the heat transfer performance on a heat exchanger is related to fouling, which is the build-up of corrosion products and sediments on the surface area of the tubes limiting the heat transfer, causing fluid flow restrictions and increase the pressure drop across the equipment.”
“In the oil and gas industry, especially in the refining sector, the main challenges associated to equipment fouling are observed in seawater trim coolers and condensers, where the biological organic growth (also known as biofouling) inside the tubes impact on the heat transfer efficiency and at the same propitiate microbiologically induced corrosion (MIC).”
“In order to prevent this phenomenon, multiple efforts are carried out in continuous basis such as chemical treatment optimization, better control of the operation parameters using data base automation such as IOW (Integrity operating Window), increase equipment backwash frequency, etc.”
What are the specific materials that you use for heat exchangers?
“When it comes to the selection of the heat exchanger materials, it is governed by the damage mechanism identified on the specific application/service and we normally use API 571 standard as reference. Additionally, each process plant in the facility has what we call CCD (Corrosion Control Documents) which basically contain the corrosion loops and the damage mechanism associated.”
“All the above standards and documents combined with lessons learned and best industry practices, ultimately dictate the best material selection for a specific application. For example, seawater trim coolers and condensers tubes can be manufactured from either cooper-nickel alloys or duplex stainless steel, also titanium has been used lately as a more corrosion resistant alloy despite it is very expensive.”
“In the end, among all the possible material alternatives, the right selection is dictated by a life cycle cost evaluation.”
What are the main types of heat exchangers that you have been working with over the last decade?
“In the oil and gas industry, especially in the downstream sector (refining), the majority of the heat exchangers are shell and tube and air-cooled exchangers type. There are some others such as plate type heat exchangers used in DHT units as feed/effluent exchangers (normally used in clean service with low fouling factor) and double pipe or hairpin exchangers. But basically, the majority of them are shell and tube and are cooler type.”
“In the last decade, I have worked with all types, however, since the majority of the population is shell and tube and air-cooled exchangers type, my involvement in equipment repairs and troubleshooting in this last two types has been the most.”
How has the evolution of heat exchangers over the past decade affected your operations?
“Definitively, not only from the heat transfer performance point of view but also from the mechanical integrity, maintainability and availability point of view. Regarding the latest advances in the downstream sector (refining), the use of plate type heat exchangers has been maximized significantly in the last decade after substantial design improvements have been incorporated by most prestigious manufacturers in order to overcome deficiencies mainly related to inspection and maintenance limitations.”
“Just recently, I have also seen that the use of spiral heat exchangers has been the preferred option in some of the major projects as recommended by technology licensors, with the objective of achieving a compact design with high heat transfer efficiency in severe fouling applications (could be two or three times the heat transfer efficiency of a normal shell and tube heat exchanger). Additionally, an optimum plot space/equipment layout can be achieved, which translates into an economic design reducing the project costs. Lately, I have seen most of the technology licensors recommending the use of spiral heat exchangers in new projects.”
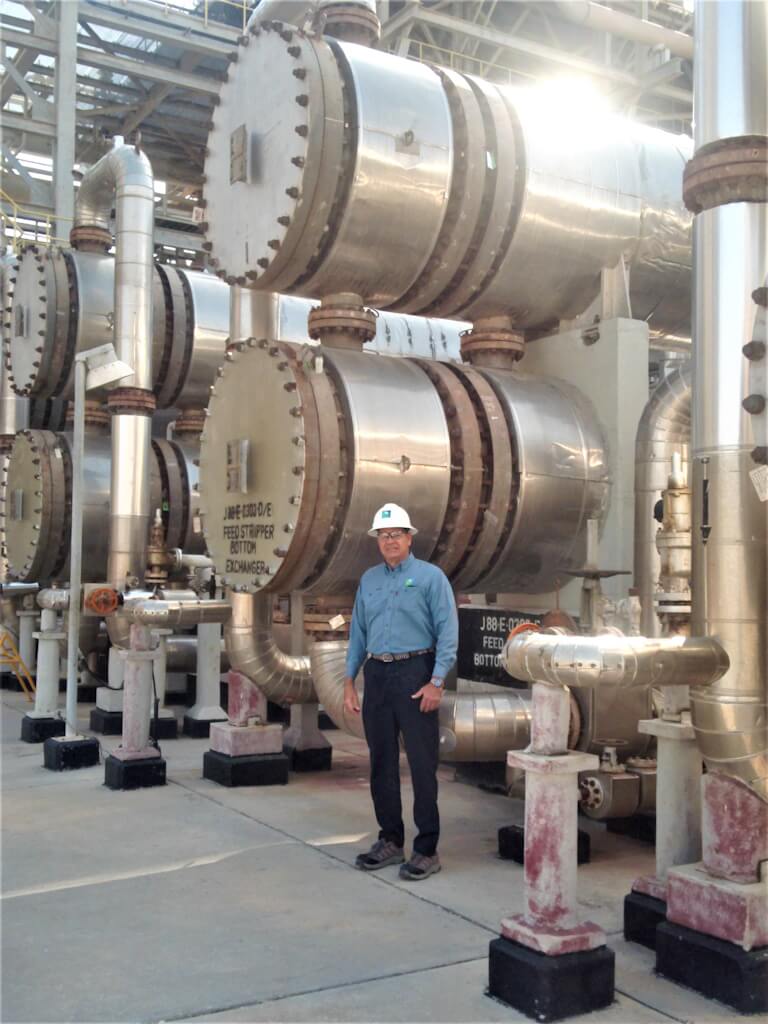
About this Featured Story
Why Subscribe?
Featured Stories are regularly shared with our Heat Exchanger World community. Join us and share your own Featured Story on Heat Exchanger World online and in print.