Often in power generation, the maintenance practice motto of the heat exchangers is “don’t worry about it until it leaks.” Only then do plant personnel open the heat exchanger just to plug the leak and then close it back up and keep running. They never get to the root cause of the leak. Due to this practice, the main steam condenser is one of the most overlooked exchangers in the plant. This can lead to catastrophic results. One of the most misunderstood and detrimental defect mechanisms that a condenser can experience is microbiological-influenced corrosion (MIC).
Michael Davis, Managing Partner, ProQual Inspections
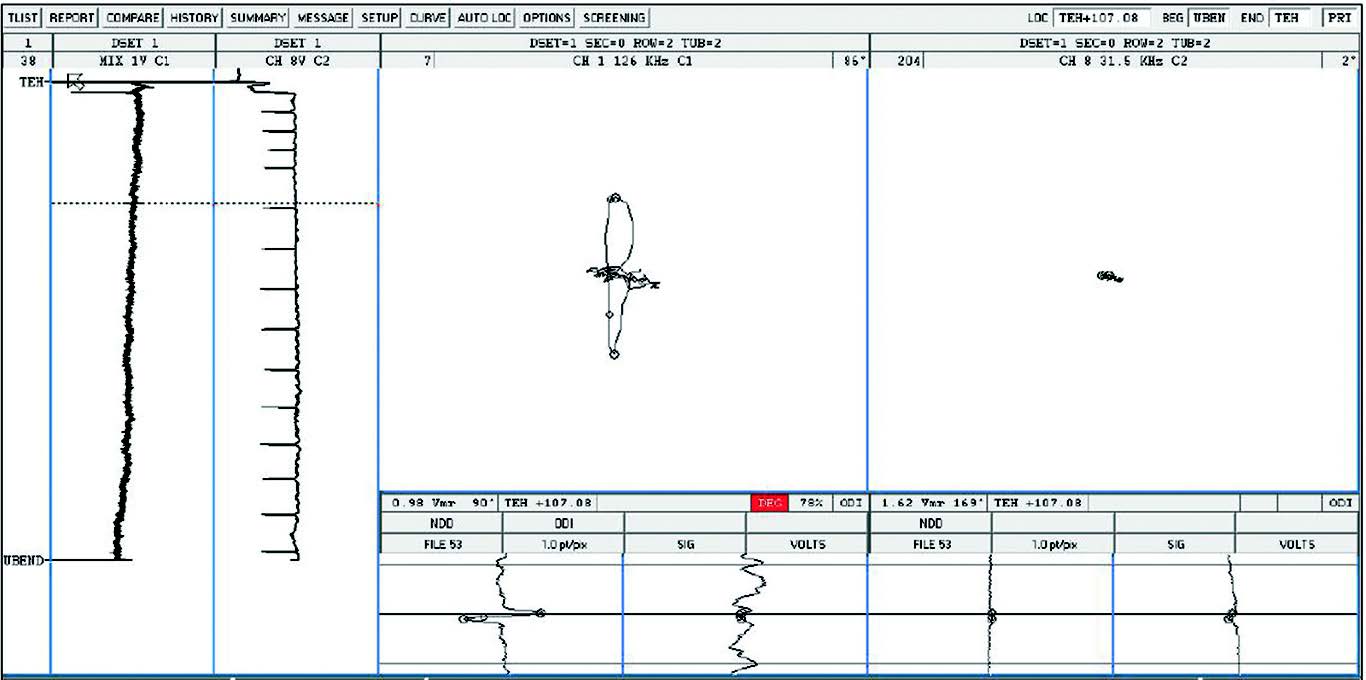
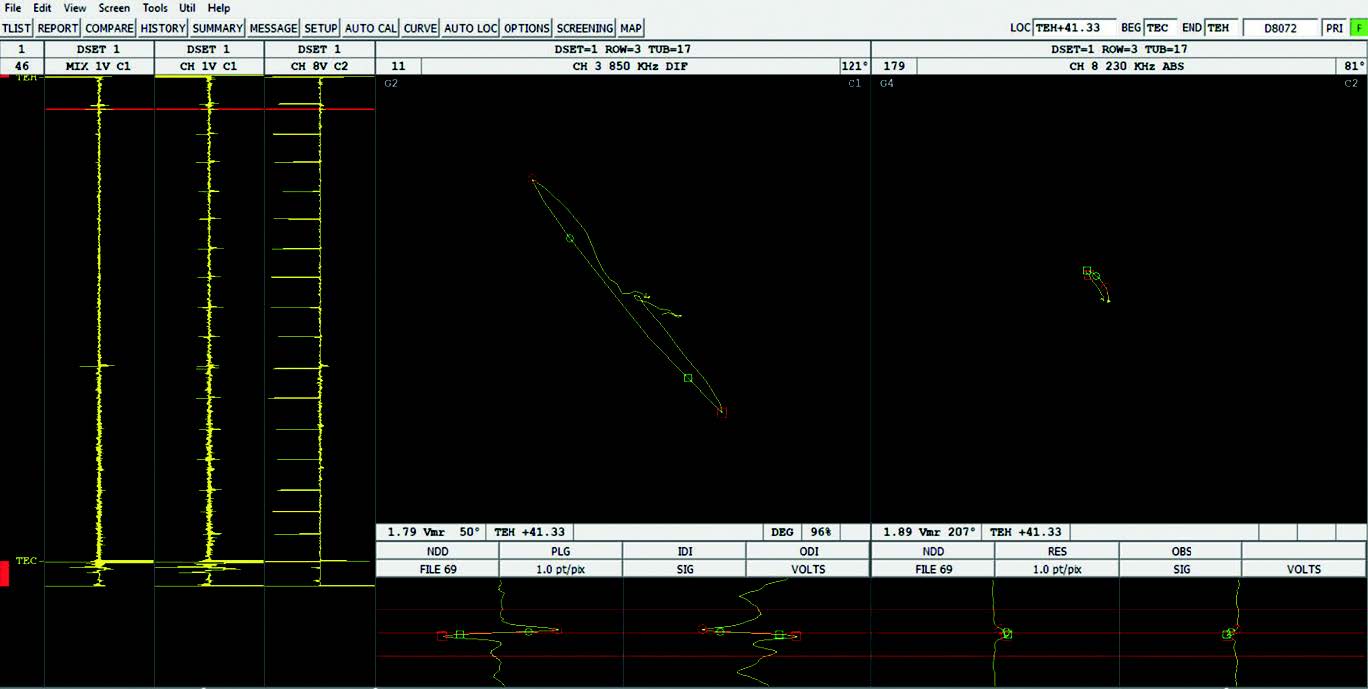
Recently, a two-unit (Unit 1 665 MW and Unit 2 700 MW) coal fired power plant in the Midwest of the United States was experiencing leaks in their high pressure feed water heaters on unit 1. The tube specifications are .625” X .072” 304 SS. During their next outage, a 100% eddy current exam was conducted on the heater with the leaks. Eddy current testing showed very deep, small volume indications throughout the outlet (upper) section of the heater with all the signs of being chloride-induced stress corrosion cracking. The SCC found in the HPFWH is a classic example of chloride induces SCC. So, the question is, where are the chlorides coming from?
Initial investigation
After discussions with the plant engineers, there were a few theories for the origins of chlorides. During these discussions it was discovered that the main condensers have never been eddy current tested. In the past whenever they had a leak, they just brought the unit down, plugged the tube(s) and brough the unit back online. In addition to finding out the condenser has never been tested, we found out the water used for cooling came from the local reservoir. Like many reservoirs, it is used for recreational use as well as agricultural use. As the water comes into the intake for the plant, it is chlorinated to kill off any bacterial growth that can cause other issues. Once we discovered this, we were convinced that tube leaks in the condenser were the source of chlorides causing the tube leaks in the HP feedwater heaters. It was highly recommended that an eddy current exam be conducted on the condenser to see if the cause of the leaks could be discovered.
Pinpointing the source
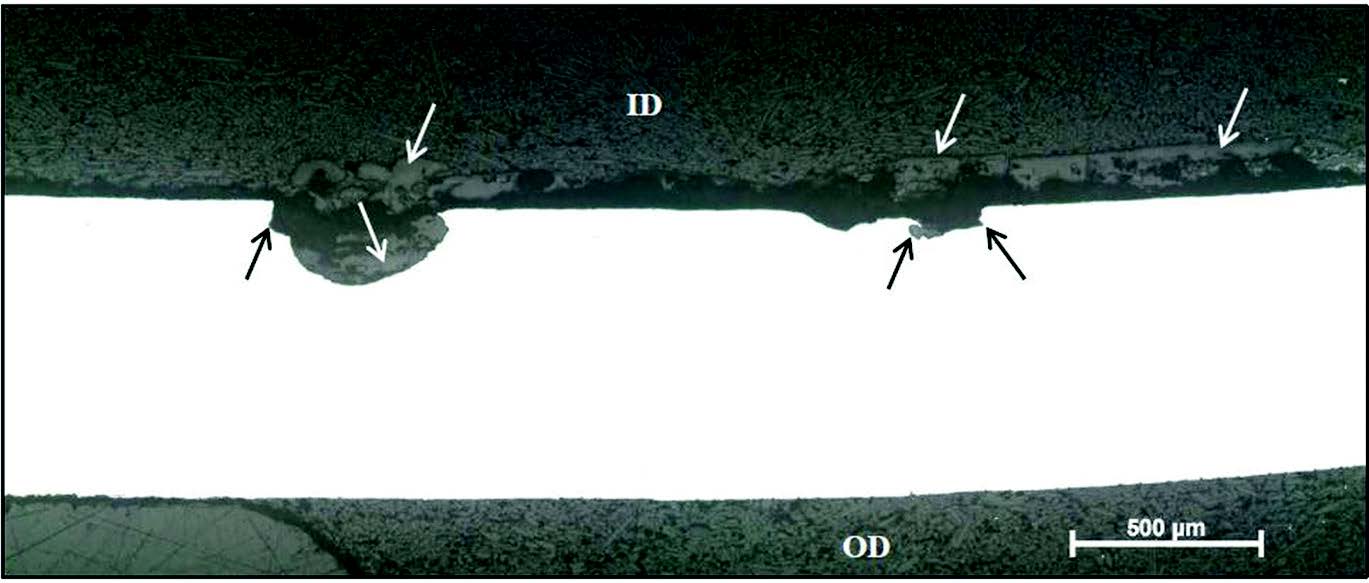
On the next outage, a 25% (2,827 each) exam was conducted on the east and west water boxes concentrating on 100% of the tubes in the first ten rows, then random tubes throughout the bundle to make up the remaining 25%. The tube specification for the condenser is .875” X .028” 304 SS. The results of the exam were quite revealing. Several tubes had inside diameter (ID) indications with some of them very deep and at or very near through wall. There were also several with outside diameter indications (see Figure 1). So now that the source of the chlorides was found (condenser tube leaks), we now need to know what the caused these indications. Tube samples were extracted from both water boxes to include both ID and OD indications. Metallurgical analysis was performed on these samples. We finally found the cause.
Metallurgical analysis
The eddy current indications in the submitted condenser tubes were a result of fine MIC pitting on the ID surface. Custers of very fine, tunneled pits were found at each of the indication sites. Subsurface tunneling pits under uniform films that are rich in manganese, especially in chlorinated waters, is common in stainless steels where MIC has occurred.


Conclusion
A comprehensive testing program is essential for the safe, reliable operation of any plant. Often a failure in one component will lead to damage and failures downstream with other components. In this case, neglecting condenser tube leaks can lead to failures in the HP feed water heaters. While the ID flaws were easily understood to be MIC, the OD indications were found out to be also MIC. They started out as a small tunnel on the OD and then opened up closer to the OD of the tube. Therefore, eddy current testing identified them as OD flaws when in fact, they were just really deep ID flaws. As a result of these findings, the plant implemented a complete and regular testing program on the condensers in this plant, they now conduct 100% eddy current test on the condenser during every outage on both units. Since implementing this testing program, they have not had any online tube leaks since.
About this Technical Story
This Technical Story was first published in Heat Exchanger World Magazine in October 2024. To read more Technical Stories and many other articles, subscribe to our print magazine.
Technical Stories are regularly shared with our Heat Exchanger World community. Join us and share your own Technical Story on Heat Exchanger World online and in print.