PECPL has partnered with German company GESMEX for the manufacture and supply of plate & shell heat exchangers. These heat exchangers are extensively used in oil & gas and other process industries. Under our partnership agreement, Gesmex will continue to manufacture the plate assembly – its core competency – and Precision will manufacture the shell and complete the final assembly at its Chennai facility.
By Vijay Chakravarthy (Precision Equipments Ltd.) and Mike Hallmann (GESMEX)
The plate & shell configuration offers many important advantages over the conventional shell & tube. Those who have switched over to the plate & shell configuration often react by asking: “How come we were not aware of this choice before?” or “why did we not know about this earlier?”. In this short article we will explain or provide:
1. A basic description of plate & shell with sub component views
2. Current market applications
3. Advantages of plate & shell over conventional shell & tube
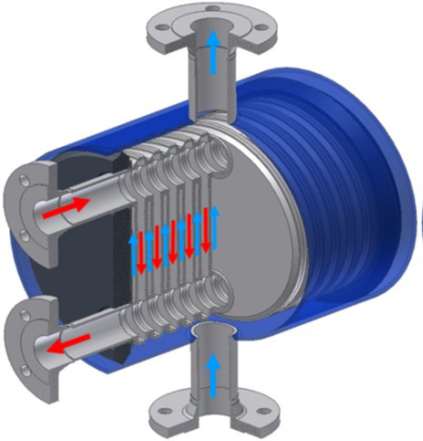
Basic description of plate & shell
A basic sketch of plate & shell is shown in Fig. 1 and a cut-away view in Fig. 2. From both these figures it can be seen that:
- Circular heat exchanger plates are arranged as a pack to form flow channels.
- The warm and cool streams flow through alternate channels mostly, counter-current
- Heat transfer takes place through the walls of the plate channels
- The plate channels are separated by highly reliable laser-made welds
- Plates are welded alternately on the outer circumference and on the edges of the plate openings
- Appropriate ports are provided in the plate pack for the channel side and shell side streams to flow through the plate pack
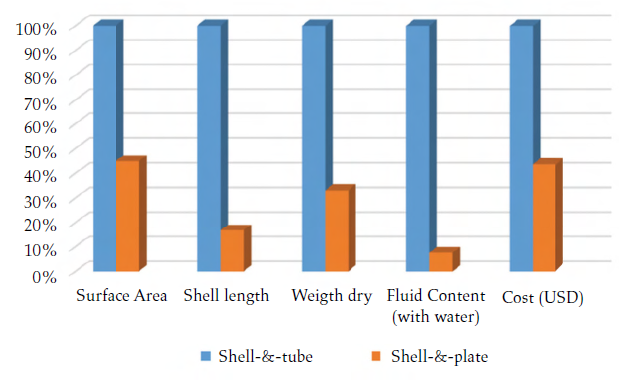
USPs as a result of GESMEX laser welding technology advantages
If you were to reflect on your past experiences, what is the weakest point of a welded heat exchanger – for shell and tube as well as all types of welded PHE? Your likely conclusion will be that it is the welds of either the tube-to-tubesheet or circumferential on exchanger plates. That was our initial driver.
Over a period of two years, GESMEX and the German company Trumpf developed a special laser welding technology, able to create weld seams with a unique cross-sectional area. In fact, that area provides up to 3.5x the thickness of the heat transfer plates alone. Thanks to this development, the plate welds are no longer the weakest points of the heat exchanger design. Since the plate material became the weakest point, working out how to improve reliability of heat exchangers for demanding applications became predictable instantly. Now the focus could be set on material thickness, material grades, alloy structure, etc.
In Figure 3 you can see the deformations that GESMEX laser welded plate packs are able to withstand during burst pressure testing, performed continuously.
The welding machine resulting out of the original inventions was installed in year 2008. Last year, a second Laser welding center was taken into operation that consist of all the original advantages as well as additional 14 years of shell & plate manufacturing and operational experience of > 3,000 heat exchanger.
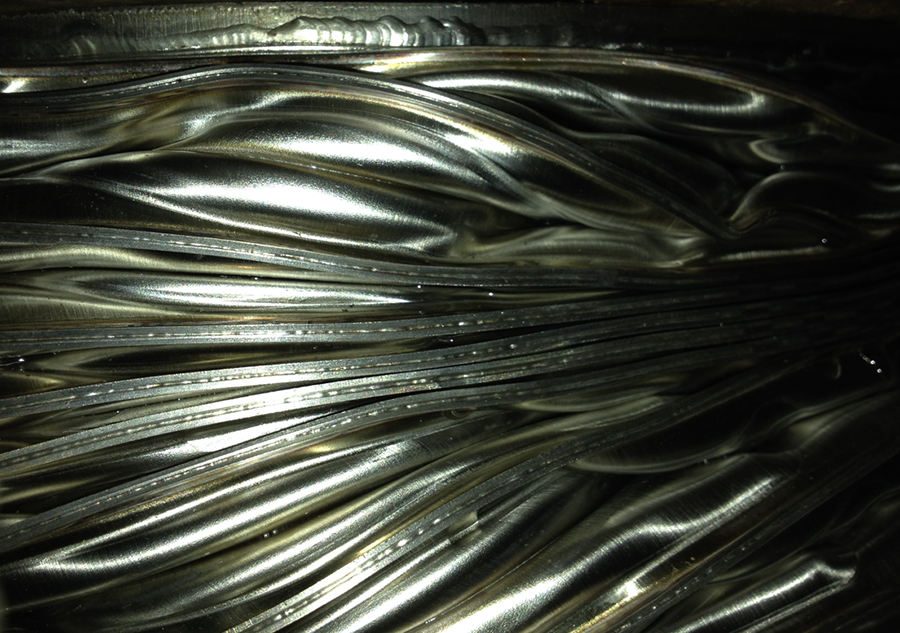
Current market applications
It should be noted that plate and shell heat exchangers are capable of meeting almost all of the same operating conditions as those of conventional shell & tube heat exchangers. Therefore, it can cover a broad range of applications. Typical operating parameters for plate & shells are shown below.
Operating Parameters
- operating pressure: -1 to 400 bar(g) (depending on design temperature)
- operating temperature: -200 to +550°C (depending on design pressure)
- dynamic viscosity: up to 8.000 mPa s (like crude oil 15°C)
- performance range: up to 100 MW
Materials of construction
Stainless steel (304, 304L, 316, 347, various Hastelloy® grades) is the principal material of construction. The plate presses also handle Titanium depending on the requirements placed by the application.
Markets – Oil & Gas/LNG
- Glycol Interchanger
- LNG Cargo Condenser
- Crude Oil Cooler
- NG Heater
- Fuel Gas Cooler
- LNG BOG Heater
- Vent Gas Economizer
The table above summarizes the different applications where Gesmex heat exchangers are currently employed. Gesmex/PECPL are engaged in efforts that will broaden the applications base to meet the needs of process industries as a whole.
Summary
Plate & shell offers the following advantages over shell &tube
- Compact design – less surface area required. more surface area / per installed volume.
- Counter current flow – Higher effective mean DT
- Lower volumetric hold-up and reduced weight.
- Partial rounded geometry
- All welded construction
- Smaller size and foot print compactness and lower foot print (3 to 4 times size reduction in volume & weight)
- Lower overall cost – capital & operating