This article is part two of a two-part series. The first Q&A session appeared in the May/June issue of Heat Exchanger World magazine and can be found here: https://heat-exchanger-world.com/qa-plate-heat-exchangers-part-1/
Dr Giuseppe Tommasone has been working with Plate Heat Exchangers (PHEs) since 1979. Over the years, he has collected commonly asked questions about the equipment. Here you can find all of the answers to those frequently asked questions in one place, put together over 40+ years of experience.
By Dr Giuseppe Tommasone, Heat Transfer Consultant
Q1) When I have to assemble plate packs after service, should I use a torque wrench?
A) No, there is no need for a torque wrench. The only criteria are measuring internal distance (A) between frame and cover plate (see PHE’s nameplate) and tightening bolts to the proper length (see figure 1). A common mistake is tightening it too much, thinking that is safer, but it in fact causes the gasket groove of the plate to be deformed and possible leakage will occur.
Q2) In case of leakage should I remove damaged plate?
A) Not only one plate should be removed, but a couple every time, otherwise a mixing between two fluids will occur. If only a couple of plates are removed, a PHE is able to continue working without a significant difference. NOTE: On a Plate Heat Exchanger specially designed for high temperature duties, extreme and sudden temperature drops may sometimes cause a temporary leakage. A typical example is a sudden shutting-off of the hot medium flow. The heat exchanger will normally seal again, as soon as the temperatures of the equipment have stabilized.
Q3) due to space restrictions, I would like to install a PHE in a horizontal position, rather than the traditional vertical. Are there any issues with this?
A) In principle there are no objections; maybe plates with diagonal flow could work better than parallel flow plates, due to no possible area for air/gas bubbles on the top, but several studies demonstrate there are no differences in thermal performance. Diesel engines, for example, are typically mounted horizontally.
Q4) We have pressure spikes in our water circuit, how can we detect if leakage is due to water hammer?
A) A PHE responds to water hammer or hydraulic shock in one typical way: gaskets being out of groove. Other units like Brazed Plate Heat Exchangers (BPHE) can experience deformation in the last plate at the end of the plate pack due to its rigid structure. A PHE, owing to a set of gaskets, is a little bit more flexible, but gaskets are not able to stay in their proper position when pressure spikes suddenly.
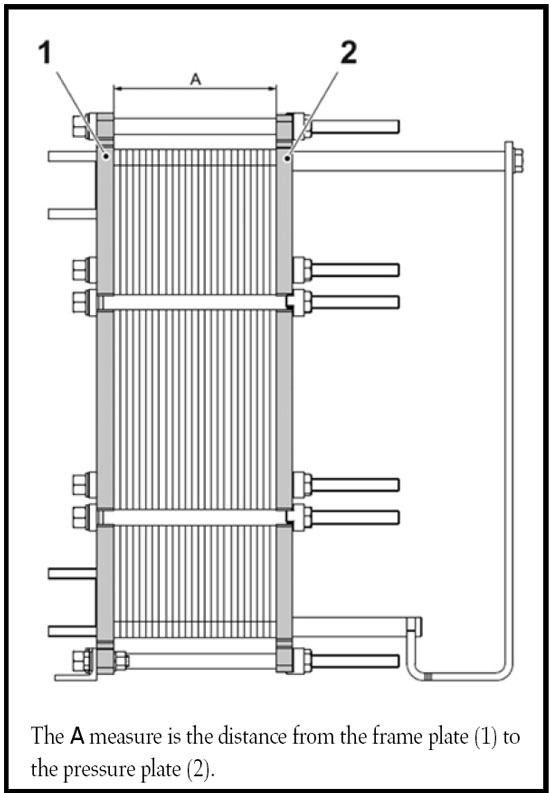
Q5) After weeks of operation, we notice a significant reduction of heat load: what should we keep under control first?
A) If flowrates are what they should be according to specifications and pumps are running properly, first check on the pressure drops. It is good practice to install pressure gauges upstream and downstream from the PHE. During start-up, particles inside piping often move into the PHE which acts as a press filter, keeping solids inside the plate pack.
Normally, pressure data is sent to OCS so the control room is able to detect immediately any pressure drop increases. Nowadays, IoT devices can help to read these info on smartphones as well.
Q6) A supplier has mentioned ‘backflushing’ to increase the service period of plate pack opening; what is this?
A) Backflushing is a system created mainly for large seawater cooling in order to change the flow of both fluids in the opposite direction, so that particles, debris and so on laying on the bottom of the plate pack due to reverse flow are dissipated.
Q7) ‘AHRI Certified’ is mentioned on a data sheet. What does it mean?
A) The AHRI Product Performance Certification Program is a voluntary program, administered and governed by AHRI, which ensures that various types of heating, ventilation, air conditioning, refrigeration, and water heating products perform according to manufacturers’ published claims. Products that are certified through the AHRI Product Performance Certification Program are continuously tested, at the direction of AHRI, by an independent third–party laboratory, contracted by AHRI, to determine the product’s ability to conform to one or more product rating standards or specifications.
This program applies to production models of gasketed plate-type heat exchangers, that utilizes any of the following fluids on one or both circuits, for HVAC applications only.
• Water;
• Seawater;
• Ethylene Glycol (10%-50% concentration);
• Propylene Glycol (10%-50% concentration)
Q8) Our maintenance department was trying to solve a leakage problem and tightened the plate pack too much (less than the ‘A’ measure on the nameplate) and the plates are now deformed. Is there any chance to reshape the plate?
A) Generally, once a plate has lost its original corrugation design it is not worth trying to return it to the original shape, it is better to buy a new plate pack.
Only in the case of large plates in an exotic/expensive material does trying to adjust the plate make sense, bearing in mind that in any case positive results are not guaranteed.
Q9) Several PHE manufacturers mention clip-on, Clip-grip gaskets, Sonderlock, Eco-loc glueless gaskets. Are these preferred over glued gaskets?
(A) First of all, it’s important to understand that the glue function of a glued gasket is to keep the gasket in the right position for the gasket groove of the plate and not to seal fluids. The glue is never in contact with process fluids.
Removing the glue from the gasket it not easy (sometimes nitrogen at a low temperature is used for easier removal). It is common to heat up the back side of the plate with a flame in order to remove gasket in the field, or in a Service Centre using caustic soda at 20% at 60°C followed by water-rinsing with water and then orthophosphoric acid at 20%.
In the past, the main issue with glue-less gaskets was on large plates, because once the plate pack was opened, gaskets stuck to the back side of adjacent plate and sometimes, during cleaning operations, they fell out of the proper position. For this reason EPC contractors and top players in oil & gas were keeping glue gaskets in their projects.
In recent years glue-less gaskets with better design have been introduced, mainly in the HVAC market and later on for industrial applications; with new developments such as Clip-Grip, glueless gasket are widely accepted.
Q10) We found small traces of process fluid in the cooling water, but looking at plates we are not able to detect any holes. What should we do?
(A) In case of chloride presence higher than 300 ppm, corrosion (pitting) could be a possible cause with plates made of 304/316 steel, and the small holes can be difficult to detect.
The best way to inspect for corrosion, holes or cracks is dye penetrant testing. Using this method, which originated in the aviation industry, even the finest hairline cracks in the plate can be made visible.
After cleaning, the entire surface of each single plate is sprayed with a fluorescent paint. After the appropriate exposure time, the plate is rotated and thoroughly inspected under UV light in the darkened test room. Damaged plates are marked accordingly and placed aside. Flawless plates are now cleaned again by means of high pressure.
The ultraviolet test is used upon request, usually specialty applications where fluid mediums can only be detected under UV light (see figure 2).
On site dye-testing is standard for locating cracks, pinholes, or failures. With red dye-penetrant saturating the plate surface, and white developer solution covering the reverse side, this test is capable of detecting even miniscule imperfections (see figure 3).
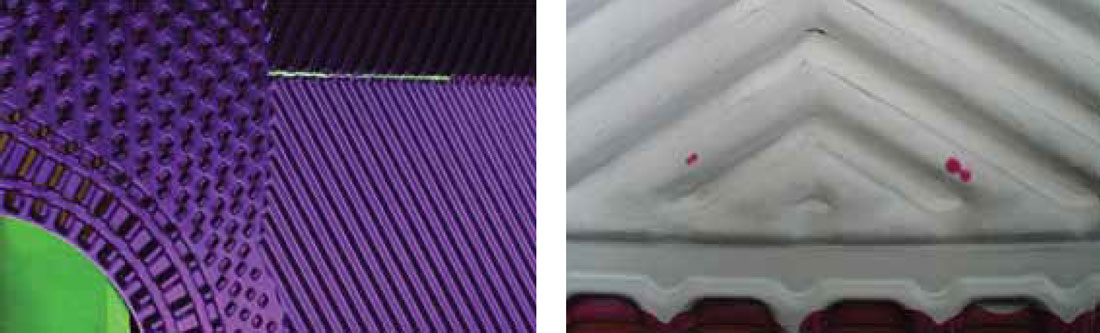
Q11) on data sheet, 3mm of over-thichkness for corrosion 3 mm is mentioned. How does this apply to a plate of 0.5 mm?
A) This is the classic result of copy & paste of a Shell & Tube in Carbon Steel specification. Over thickness for stainless steel does not occur in standard industrial ap-plications.
The only time this would happen with a PHE is with sulphuric acid where Hastelloy C276 plates are used with 0.7 mm instead of 0.6 mm taking in consideration corrosion rate of material every year. Plate heat exchangers constructed of alloy C276 plates and Viton gaskets impose certain limitations on the process in order to achieve reliable and extended operation of the heat exchangers. The maximum allowable temperature into a plate heat exchanger is a function of acid concentration. Exceeding the maximum temperature will result in higher corrosion rates and reduced life of the plate pack.
ABOUT THE AUTHOR
Dr. Giuseppe Tommasone is a heat transfer expert and consultant for an EPC contractor. His expertise is in special heat exchangers in the oil & gas industry where he helps customers to improve performance by providing heat transfer solutions.
Since 1979 he has worked with and helped more than 3000 small, medium, and large businesses in the oil & gas, power, steelworks, chemicals, and pharma industries as well as EPc contractors. Dr. Tommasone studied Chemical Engineering in Milan, Italy.