The Ekin Endustriyel team rolled up their sleeves for a heat recovery project in a textile plant in Bursa, Turkiye, applying their expert engineering knowledge in the field of energy efficiency.
By Enes Kuzey Er, Ekin Endustriyel
Due to the compactness of the design, this kind of heat recovery system is ideally suited to facilities which value the environment and are keen to preserve resources. An additional bonus is that in many countries, local governments support investments in this type of technology, which assists companies in fulfi lling their aims of lowering carbon and other greenhouse gas emissions.
The heat recovery systems, which in this case were specifi cally designed for the textile industry customer, can be manufactured in various confi gurations depending on the process details and facility layout.
The heated oil and air resulting from the operation of the compressors contain a large amount of energy, which is recovered using a 3-stage heat exchanger system. This has resulted in signifi cant savings in energy costs as the recovered waste heat provides hot water for the facility rather than using natural gas.
Three stage process
In the first stage, air at approximately 80 °C from each compressor flows through MIT shell and tube heat exchangers, heating the water. Two heat exchangers were designed for each of the two separate compressors. The exchangers measure DN150*1250 mm, are type BEM (TEMA) and are constructed from SF-Cu grooved tubes (EN-12449) with an S235JR shell (EN-10217). Approximately 35 kW of heat is recovered with each exchanger at this stage.
In the second stage, the compressor recovers the hot oil in a closed cycle. At approximately 80°C, the oil passes through the primary circuit, and the water heated in the first stage passes through the secondary circuit. For this stage, two highly efficient MIT Plate Gasketed heat exchangers were deployed, and 150kW heat recovery per exchanger was achieved.
In the third and final stage, the water heated by the first two stages passes through a single heat exchanger constructed entirely in stainless steel. A custom-designed MIT Tubular Series heat exchanger heats both hard water and soft water while keeping them separated. The exchanger measures DN200*2950 mm and is type BEM (TEMA). The construction material was AISI 316 (EN-10216) for the tubes and AISI 304 (EN-10217) for the shell.
Clean water entering the system at 20 °C was heated to 50 °C, and a total heat transfer of approximately 350 kW was achieved.
Energy savings
After passing through a stainless heat exchanger, the recovered clean hot water is used as domestic water by the facility. In this way, the business achieves significant reductions in fuel costs. The payback time of the system is calculated at approximately 14 months.
Another advantage of the system may yet emerge, as the hot water obtained in the second stage may eventually be used for other applications in future.
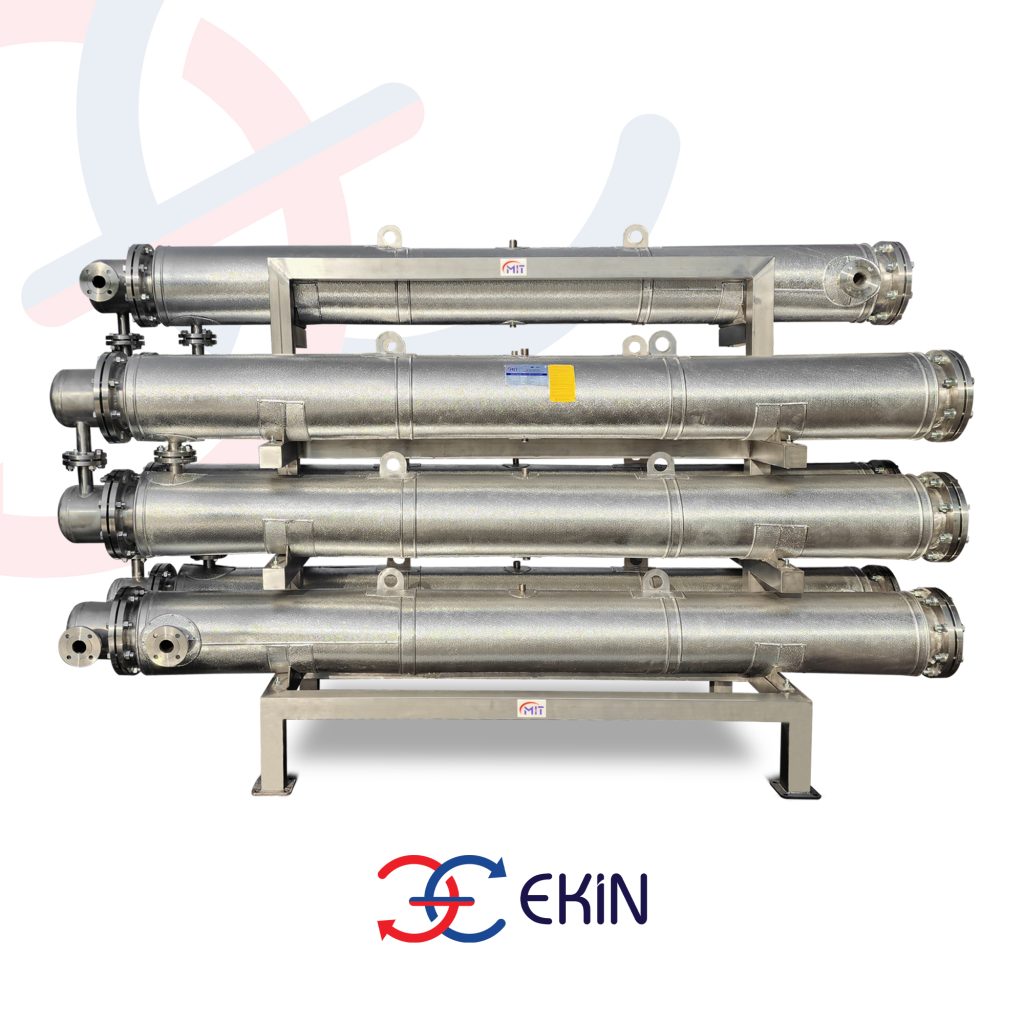
About the author
Enes Kuzey Er is a Heat Transfer Product Sales – R&D Specialist at Ekin Endustriyel, responsible for the sale of heat transfer products such as plate heat exchangers (gasketed or brazed) and shell and tube heat exchangers. He also finds solutions for industry needs based on customer feedback and provides support for R&D processes.
About this Technical Story
This Technical Story was first published in Heat Exchanger World Magazine in February 2024. To read more Technical Stories and many other articles, subscribe to our print magazine.
Technical Stories are regularly shared with our Heat Exchanger World community. Join us and share your own Technical Story on Heat Exchanger World online and in print.