Aggreko offers tailored heat exchanger applications to ensure seamless operations amidst the complexities of maintenance and emergencies. This article explores the company’s pivotal role in providing temporary solutions, addressing the critical needs of the industry with precision and efficiency.
By Hinal Patel, Business Optimization Advisor – Petrochemical & Refining at Aggreko North America
With technology tracing back to over 150 years ago, heat exchangers have undergone major developments and advancements across a range of industries – from oil and gas to food and beverage. For modern-day petrochemicals and refining, heat exchangers play an especially critical role.
Used to transfer heat between a source and a working fluid, heat exchangers maintain heating and cooling streams in a process plant to ensure essential, smooth process operations.
A vital source of fuels, lubricants, and feedstock for plastic production, the petrochemical and refining industries rely on heat exchangers as a critical component to ensure high-quality final outputs.
With over one hundred operable petroleum refineries, the United States is home to some of the largest petrochemical and refining facilities in the world. With a range of hazards, from fires and explosions to toxicity, keeping these facilities running safely is of the utmost importance, and their critical role in the production of petrochemical goods makes heat exchangers an essential link in the petroleum-based supply chain.
Temporary solutions
With heat exchangers being as important as they are for petrochemical applications, there must be a wide range of solutions available to fit the needs of plants and refineries. While permanent exchangers may be a useful addition to an industrial plant’s operation, sometimes temporary solutions are needed. Why choose a temporary solution when you can purchase one of your own?
For starters, mobile power offerings can be installed immediately, allowing plants to stay up and running in the event of utility failures and emergencies – without compromising efficiency and cost. Many systems can have a lead time of 6-8 months or more, and as a refiner, you’ll likely need that solution sooner rather than later.
With temporary technology providers, a team of technical experts and engineers assess your existing equipment and systems for risks, then recommend, design, and implement the best remedy for your plant.
Maybe your heat exchanger is down for maintenance, or the one you need is back-ordered. A temporary system allows you to continue regularly scheduled work, lightening the load until a permanent solution is in place. Tailor-made to each customer, temporary solutions provide a unique solution to individualized needs – without the commitment of purchasing expensive equipment. Several firms offer temporary exchangers, but only a handful specialize in those that meet the stringent needs of the petrochemical and refining industries. Aggreko, the world’s leading provider of mobile power solutions, specializes in temporary power generation, heating, cooling, and dehumidification equipment for the petrochemical and refining industries. Aggreko offers a large inventory of heat exchangers on the market, and its experience with several real-world projects shows the various ways temporary exchangers can be used in the petroleum world.
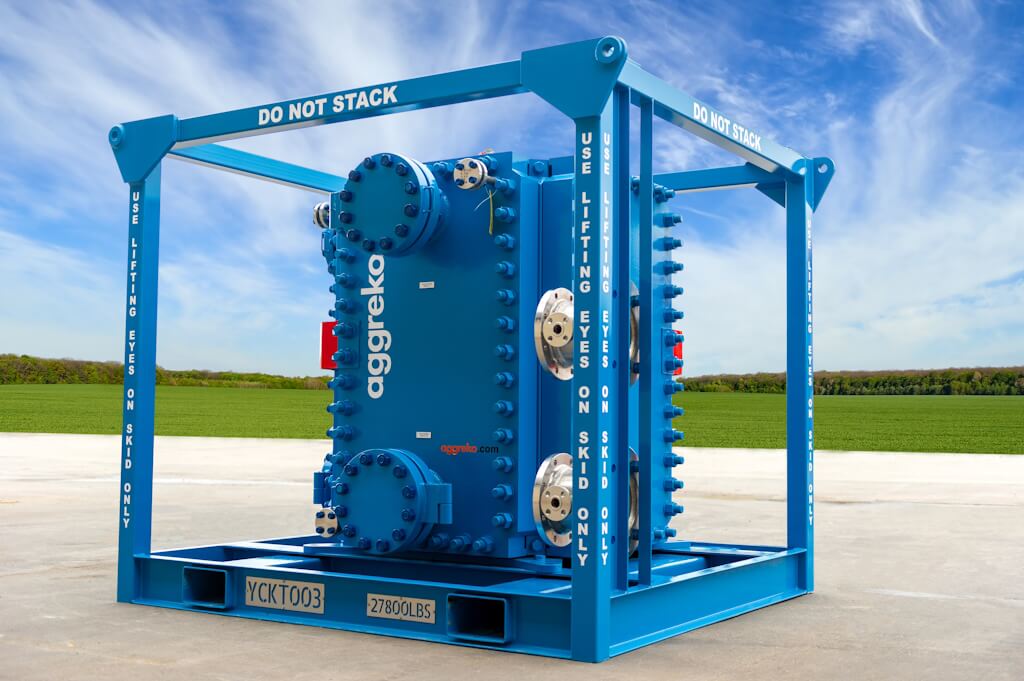
Aggreko’s exchangers on the market
Aggreko prides itself on delivering unique solutions, providing not only equipment for your project, but the support of a team of specialized engineers capable of developing the solution that best meets your plant’s needs. Temporary solution providers can quickly provide contaminant-free, refinery-grade exchangers to ensure process optimization – resulting in huge operational expenditure reductions.
Aggreko offers a range of top-level heat exchangers available on the market: smaller shell and tube heat exchangers, larger heat exchangers exceeding 5,000 square feet, and specialized units such as Hastelloy-C heat exchangers, unlike any others available.
The Large Node heat exchangers from Aggreko are some of the largest on the market, enabling petrochemical and refinery customers to reduce their carbon footprint by replacing several smaller heat exchangers with a single one. With a higher pressure and temperature rating than others, it’s suitable for various applications. A sustainable solution to customers focused on sustainability, Aggreko is the only rental company with this type of system and size offering. The Hastelloy-C heat exchanger is unlike any heat exchanger on the rental market. Its unique material allows for higher resistance to a wide range of corrosive chemicals and gases, making it the ideal solution for applications requiring high-performance heat transfer and corrosion resistance. As the metallurgy and configuration of this exchanger enables it to meet unique petrochemical and refining applications, beyond the capabilities of typical exchangers, it’s an ideal choice for plants operating in these industries. Similar to the Large Node heat exchangers, Aggreko is the only solutions provider to offer a system with this metallurgical composition to petrochemical and refining customers.
Real-world applications: Large Node heat exchangers
When a Gulf Coast refinery needed a temporary shell and tube heat exchanger arrangement for their Tail Gas Unit (TGU), Aggreko was called to supply a temporary solution to reinstate the production of their TGU while their permanent exchanger underwent significant maintenance. Their permanent exchanger was severely tainted by sulfur, and it was expected to take at least a couple of months to have it cleaned.
As the refinery’s existing exchanger was out of commission, the temporary exchangers were brought in to cool 500,000+ lb/hr of sulfur-laden quench water by 60°F using the refinery’s cooling water. The total heat load was expected to be about 40-45 million BTU/hr, which is significant and requires a large heat exchanger.
Given the high flow rates and heat rejection required, Aggreko evaluated the process conditions and determined that deploying two 5,700 sqft Large Node heat exchangers was the best solution. As a result, the TGU was up and running within the week. This provided the unit the ability to stay online without interruptions – allowing the client to maintain their production levels and maintenance schedule.
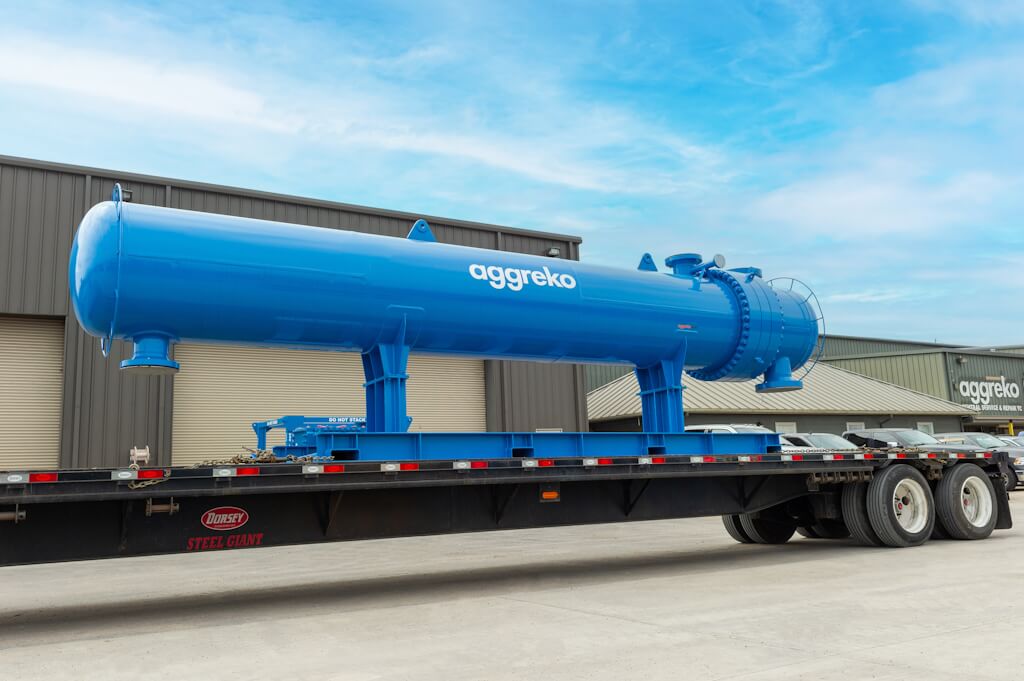
Real-world applications: Hastelloy-C
When a northern U.S. refinery experienced extreme corrosion in their tempered water coolers in the FCC slurry filtration service, both of their on-site exchangers had to be taken out of service. The plant needed to cool 200,000 lb/hr of a glycol mixture by >50°F with brackish cooling water. Given the high salt content of brackish water, a heat exchanger with specialized metallurgy is required.
Aggreko’s specialty equipment, process expertise, and local presence enabled the rapid deployment of a Hastelloy-C Crossflow heat exchanger, designed to uniquely maintain normal operations until a permanent exchanger was brought to the site. As a result, the Hastelloy-C heat exchanger ensured efficient heat transfer with a low-pressure drop, thus maximizing energy efficiency, and making it a sustainable choice for this application.
Ultimately, Aggreko’s experience with their Large Node and Hastelloy-C heat exchangers shows how temporary exchanges can be used for several scenarios in petrochemical plants and petroleum refineries.
The petrochemical industry’s exchangers must meet stringent requirements to ensure the desired quality of the final product from refineries and factories, and providers like Aggreko offer temporary exchangers when these customers’ permanent ones need to be out of commission.
About the author
Hinal Patel is currently a Technology Advisor at Aggreko, bringing experience from previous roles at SS Capital Group and Various Roles. Hinal Patel holds a 2004 – 2007 B.S. Chemical Engineering at Georgia Institute of Technology. With a robust skill set that includes heat transfer, hydrotreating, process optimization, fluid dynamics, process engineering and more, Hinal Patel contributes valuable insights to the industry.
About this Featured Story
This Featured Story was first published in Heat Exchanger World Magazine in April 2024. To read more Featured Stories and many other articles, subscribe to our print magazine.
Featured Stories are regularly shared with our Heat Exchanger World community. Join us and share your own Featured Story on Heat Exchanger World online and in print.