Corrosion, a natural process we encounter everywhere, presents significant challenges in diverse industries. One industry greatly affected by this phenomenon is the realm of heat exchangers. Getting a handle on the basics of corrosion and how it specifically relates to heat exchangers becomes crucial. So, let’s unpack it together.
By Omari Hussein Sabuni, Mechanical Engineer – Kinyerezi Power Plant

In this detailed exploration, we’ll unravel the intricacies of corrosion, dissecting its various types as they pertain to heat exchangers. More importantly, we’ll shine a light on why it’s absolutely paramount to prevent and control corrosion. Think of this article as your guide, steering you through the maze of corrosion, ensuring you not only understand its nuances but also grasp the vital role of keeping it in check within the realm of heat exchangers. Stay with us as we break it down in simple terms, making the complex world of corrosion a bit more comprehensible.
Defining Corrosion
Corrosion is the gradual deterioration of materials due to a reaction with their environment, leading to the loss of material and compromise of structural integrity. In the realm of heat exchangers, corrosion can be particularly detrimental, impacting efficiency, safety, and overall performance. The materials commonly used in heat exchangers, such as metals and alloys, are susceptible to corrosion under certain conditions.
Relevance of Corrosion in Heat Exchangers
Heat exchangers play a critical role in various industrial processes, facilitating the transfer of thermal energy between fluids. The efficiency of heat exchangers relies heavily on the integrity of their materials, making corrosion a significant concern. Corrosion in heat exchangers can manifest in several ways, affecting both the performance and lifespan of these vital components.
Types of Corrosion in Heat Exchangers
To address corrosion effectively, it is essential to understand the different types that can occur in heat exchangers. The following are some common corrosion types encountered in these systems:
1. Uniform Corrosion in Heat Exchangers
Uniform corrosion is characterized by its even distribution over the surface of the material, leading to a gradual reduction in thickness. This corrosion process occurs due to chemical reactions between the material and its surrounding environment. In the case of heat exchangers, which are frequently exposed to varying temperatures, pressures, and corrosive substances in the fluids they handle, the impact of uniform corrosion can be significant.
Impact on Heat Exchangers:
While uniform corrosion may not result in immediate failure, its consequences become increasingly pronounced over time. The primary concern lies in the gradual thinning of the metal, which compromises the structural integrity of heat exchanger components.
The reduced thickness can lead to several adverse effects:
- Diminished Heat Transfer Efficiency: As the metal thins due to uniform corrosion, the heat exchanger’s ability to efficiently transfer thermal energy between fluids is compromised. Thinner walls may result in decreased heat transfer rates, leading to reduced overall performance.
- Increased Vulnerability to Other Forms of Corrosion: The weakened metal surface, resulting from uniform corrosion, becomes more susceptible to other types of corrosion. For example, pitting corrosion may initiate in areas where uniform corrosion has thinned the protective layer on the metal surface.
- Structural Integrity Concerns: Over time, the continuous loss of material due to uniform corrosion can raise concerns about the structural integrity of the heat exchanger. This may lead to the development of leaks or, in extreme cases, catastrophic failure.
2. Galvanic Corrosion in Heat Exchangers
Galvanic corrosion is a process that ensues when two dissimilar metals come into direct contact while being exposed to an electrolyte, such as water or other conductive fluids. This phenomenon results in the accelerated corrosion of one of the metals, acting as the anode, while the other metal acts as the cathode. The driving force behind galvanic corrosion is the electrochemical potential difference between the two metals.
Impact on Heat Exchangers:
Heat exchangers, by their very design, often incorporate different metals in close proximity due to diverse operational requirements. This makes them particularly susceptible to galvanic corrosion. The consequences of galvanic corrosion in heat exchangers can be significant:

- Accelerated Corrosion: The galvanic couple formed by dissimilar metals sets the stage for accelerated corrosion of the more electrochemically active metal. This can lead to localized corrosion and structural deterioration.
- Reduced Lifespan of Components: The intensified corrosion in specific areas compromises the structural integrity of heat exchanger components. Over time, this can contribute to premature failure and a shortened lifespan of the equipment.
- Impaired Heat Transfer Efficiency: Galvanic corrosion may result in the formation of corrosion by-products that can impede the flow of fluids within the heat exchanger. This impediment can reduce the efficiency of heat transfer between the fluids, affecting overall
performance.
3. Pitting Corrosion in Heat Exchangers
Pitting corrosion is characterized by the localized formation of small pits or craters on the metal surface. Unlike uniform corrosion that occurs uniformly across the entire surface, pitting corrosion concentrates its attack in specific areas. The initiation of pits is often associated with the breakdown of protective films on the metal surface, allowing aggressive ions to attack localized spots. Pitting corrosion is particularly insidious because the pits can penetrate deeply into the material, even though their size may be relatively small. This makes detection challenging, and the impact can be severe, leading to compromised structural integrity.
Impact on Heat Exchangers:
In the context of heat exchangers, where the efficiency and reliability of thermal energy transfer are paramount, the consequences of pitting corrosion can be significant:
- Development of Holes and Leaks: Pitting corrosion can lead to the creation of small, yet deep, pits on the metal surface. Over time, these pits can propagate and coalesce, resulting in the development of holes and leaks in the heat exchanger tubes and surfaces.
- Reduced Heat Transfer Efficiency: As pitting progresses, the metal surface in affected areas becomes uneven, disrupting the smooth flow of fluids and hindering the efficient transfer of heat. This can lead to reduced heat transfer efficiency and decreased overall performance.
- Structural Compromises: The localized nature of pitting corrosion means that critical structural components may be compromised. This can result in weakened areas that are more susceptible to mechanical stresses, potentially leading to catastrophic failure.
4. Crevice Corrosion in Heat Exchangers
Crevice corrosion is characterized by its occurrence in small, enclosed spaces, where a stagnant electrolyte can accumulate. These spaces can be naturally present in the design of heat exchangers, typically in joints, seams, or other areas where metal surfaces are in close proximity but limited exposure to the surrounding environment. The stagnant electrolyte may contain corrosive ions, and the restricted access to oxygen can create localized conditions conducive to corrosion. The corrosion process in these confined spaces often leads to the degradation of the material in and around the crevice, which can have detrimental effects on the overall performance of the heat exchanger.
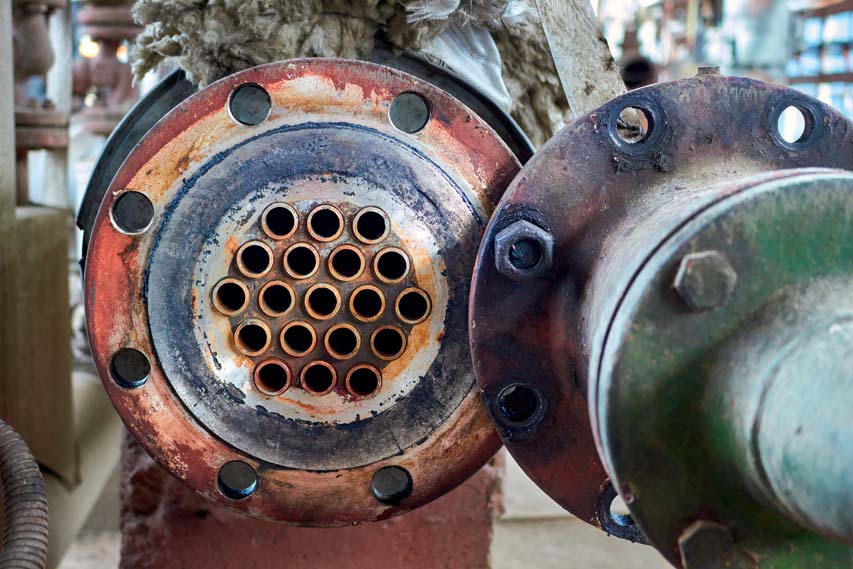
Impact on Heat Exchangers:
In the context of heat exchangers, the impact of crevice corrosion is notable due to the specific design characteristics of these systems:
- Localized Material Degradation: Crevice corrosion can result in localized material degradation within the confined spaces of heat exchangers. The corrosion process may lead to the formation of pits and cracks, compromising the structural integrity of the affected areas.
- Reduced Heat Exchanger Efficiency: As crevice corrosion progresses, the material loss in the confined spaces can impede the smooth flow of fluids within the heat exchanger. This impediment can lead to reduced heat transfer efficiency and compromised overall performance.
- Risk of Leaks: The localized corrosion within crevices increases the risk of developing holes or leaks in the affected areas. This can result in fluid leakage, impacting the efficiency of the heat exchanger and posing safety concerns.
Importance of Corrosion Prevention and Control
Importance of Corrosion Prevention and Control Given the critical role of heat exchangers in various industries, preventing and controlling corrosion is paramount. Several strategies can be employed to mitigate the adverse effects of corrosion on heat exchangers:
- Material Selection: Choosing corrosion-resistant materials for heat exchanger components is the first line of defense. Stainless steels, titanium, and certain alloys exhibit high resistance to corrosion.
- Protective Coatings: Applying protective coatings or corrosion inhibitors can create a barrier between the metal surface and the corrosive environment, extending the lifespan of heat exchangers.
- Cathodic Protection: Utilizing cathodic protection methods, such as sacrificial anodes or impressed current systems, can help prevent galvanic corrosion by shifting the corrosion potential of the metal.
- Regular Maintenance and Inspection: Implementing a routine maintenance and inspection schedule is crucial for detecting and addressing corrosion at an early stage, preventing extensive damage.
- Fluid Treatment: Treating the fluids circulating in the heat exchanger with corrosion inhibitors or other additives can mitigate corrosion by altering the chemical properties of the environment.
Conclusion
This article has provided a comprehensive overview of corrosion, its various types in the context of heat exchangers, and highlighted the significance of corrosion prevention and control measures. By implementing these strategies, industries can ensure the longevity, efficiency, and safety of their heat exchanger systems, ultimately contributing to enhanced operational performance. As technology evolves, ongoing research and innovation in materials and corrosion prevention techniques will continue to play a pivotal role in mitigating the impact of corrosion on heat exchangers.
About the author
Omari Hussein Sabuni is an experienced mechanical engineer at Kinyerezi Gas Power Plant, specializing in heat exchanger design, optimization, troubleshooting and providing practical solutions for various heat exchanger problems. He is skilled in analyzing thermal systems and developing innovative solutions to enhance heat transfer efficiency and adept at conducting feasibility studies, performing risk assessments, and ensuring compliance with industry standards.
About this Technical Story
This Technical Story was first published in Heat Exchanger World Magazine in March 2024. To read more Technical Stories and many other articles, subscribe to our print magazine.
Technical Stories are regularly shared with our Heat Exchanger World community. Join us and share your own Technical Story on Heat Exchanger World online and in print.