Thermo-Clean is built on over 30 years of experience in the thermal cleaning of heat exchangers, filter cleaning, and the removal of plastic and rubber from metal equipment. In this interview with CEO Robert Mol, we discussed the company’s unique installations which set it apart from the rest of the cleaning sector, and its ability to return fouled exchangers to their original performance capabilities.
By Ellie Pritchard
Thermo-Clean began as the subsidiary of Jos Mol Coatings, a distributor of powder coatings in Belgium and Luxembourg, in 1989. Sadly, founder Jos Mol passed away unexpectedly only a year later in 1990 at the age of 49 and, due to the young age of Jos’s son Robert, the leadership of the company was handed to an outside partner, Guido de Cock. Since 2005 and the well-earned retirement of Mr de Cock, Robert Mol has led the company alone. He has worked for the past 30 years to develop Thermo-Clean into the success it is today; with 10 locations across Europe, and a plan to grow further, Thermo-Clean is a leader in thermal cleaning solutions, helping to reduce its customers’ greenhouse gas emissions through optimised cleaning.
The cleaning specialists
“I started with the company in May 1989 – I was the second employee. It began with just the two of us,” Robert explains. “Coming from the paint and coatings industry, our Jos Mol Coatings’ customers would ask us how to clean their equipment. So Thermo-Clean came about by cleaning equipment first for the paint industry, and then we saw that our methods worked for the removal of other materials such as oil, plastics, glue, etc.”
With Robert now the CEO, the company has become a specialist in thermal heat exchanger cleaning, polymer removal, and filter cleaning. “Thanks to our specially developed thermal cleaning technique, we can return heat exchangers and parts to original design performance. This also means better heat transfer, lower energy costs, and less environmental impact because a cleaner heat exchanger equals lower fuel consumption, leading to reduced greenhouse gas emissions.” Present in the Netherlands, Belgium, France, Germany and Slovakia, Thermo-Clean is able to offer its services to companies across Europe in a “10-step total care cleaning process”. Over the past 3 years, the company has focused on expanding its “total cleaning” concept to now include a full service:
• Removing or swapping out a complete heat exchanger
• Transporting the exchanger off site
• Dismantling the heads
• Extracting the bundle
• Safely cleaning all parts with the advanced thermal cleaning process
• Providing additional services (Eddy Current measure-ment, tube replacement, shell refinishing and repairs)
• Reassembling the exchanger
• Pressure testing
• Returning the exchanger to the customer
• Reinstallation
In certain cases, if a customer is unsure of which type of fouling is affecting their heat exchanger, Thermo-Clean will do an initial test with a sample of the fouling to determine whether it is organic, inorganic, or a mixture of the two.
“We perform this test very quickly so that we know what will happen inside the pyrolysis oven – for example, by what percentage we can reduce this specific case of fouling,” Robert explains. “If we have doubts then we run a further TGA [thermogravimetric analysis] test to understand exactly what is in the fouling itself.”
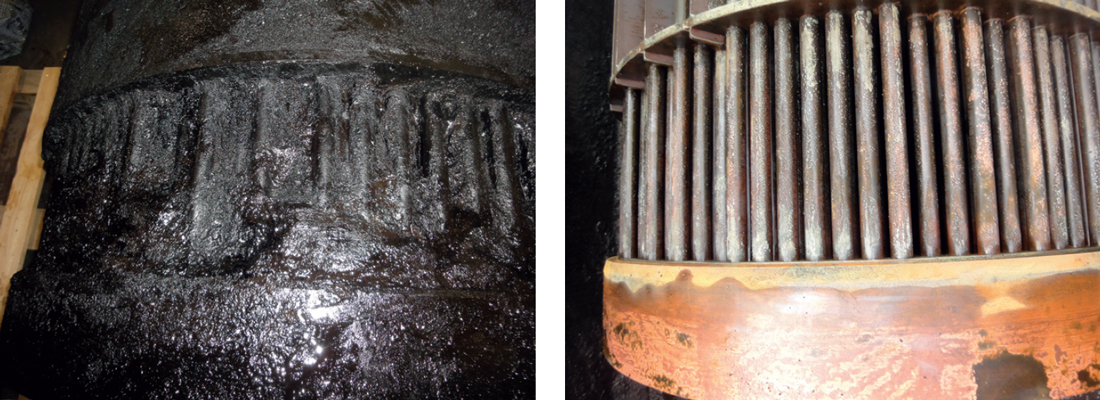
How pyrolysis works:
Thermal cleaning relies on pyrolysis, the thermal decomposition of organic materials in an oxygen poor environment (Fig. 1). At a temperature below 450°C (842°F), organic materials are converted into a homogeneous residue ready for further controlled pro-cessing.
The parts to be cleaned are put on a loading cart that is brought into the oven chamber. After closing, The oven chamber is made inert by lowering the oxygen level to 8%. The temperature is then slowly increased to as high as 450°C (842°F), depending on the character of the objects and the nature and amount of fouling. When the temperature required for gasification is reached, slight positive pressure causes the gases released to flow to the afterburner chamber. Here, they are processed at high temperature (>850°C/1562°F) for at least 2 seconds, after which they are removed (ii). This air current is sometimes used for heat recycling to recover part of the energy. Because all organic components are gasified, only a residue consisting of pigments and inorganic fillers remains. This is generally 1-5% of the original fouling volume and can easily be removed by various techniques.
(ii) If the fouling contains sulphur and/or halogens, the gases need to be scrubbed before entering the atmosphere. The permitted emissions are regulated by local authorities and can vary between countries.
(Source: ‘Thermal cleaning of heat exchangers, no alternative but a better way to clean’, Robert Mol, 2019)
In most cases, however, where the fouling is known, the team begins by learning the weight, volume, and design (plans) of the exchanger; from this information they can make an offer and a detailed estimate of the timescale for cleaning.
“Once this is agreed, we usually send our vehicles to collect the exchanger from the customer. Upon arriving at one of our 10 facilities, the most important thing to do first is arrange the right support for the exchanger to ensure it does not buckle or become misshapen during the thermal cleaning,” says Robert. “We then place thermal elements throughout the heat exchanger
“The heat can get into every corner, so it is a very extensive cleaning method – we can remove almost 100% of the fouling.”
to measure the temperature at different parts – for example, on the plate and within the tubes. We do this to monitor whether the internal parts and even the housing are all heating up in the same way.”
Robert explains that, in comparison to high-pressure methods, Thermo-Clean can predict much more accurately how long the cleaning process will take.
“With our technology, we can inform the customer in advance if we need 24 hours, 40 hours, 60 hours. This makes the planning for the customer much easier. Other methods sometimes require 1-2 weeks resulting in lost time and, even then, only 70% of the fouling has been removed,” says Robert. “For us, timescale is determined mostly by the weight of the part; we have to increase and decrease the temperature very slowly to avoid deformation of the parts. When heated, the thinner tubes will expand rapidly but the much thicker plate(s) will not. We have to ensure that both parts expand in the same way at the same time; the same with the cooling down, everything needs to shrink in the same way too.”
Savings in time, money, and emissions
Thermo-Clean uses heat and a low oxygen level (see box text Pyrolysis) to turn the organic elements in the fouling into a gas, like smoke. This smoke becomes an energy source which is then used to heat the entire oven chamber – this system essentially reuses the energy generated by the fouling to clean the equipment. Then, when all the organic parts have been turned into a gas, the oven enters a cool down phase, and the inorganic fouling now appears as an ash-like product which is far easier to dispose of. The company states its method can reduce fouling to only 5% of its original volume, and in some cases even lower; oil for example reduces to around 1% and is easily rinsed, removing the need for high pressure washing afterwards.
“In general, if you have a total of 1kg of fouling, 50 grams of ash are left over,” Robert confirms. “The benefit of our system is that the heat can get into every corner, so it is a very extensive cleaning method – we can remove almost 100% of the fouling. This means that our cleaning technology is capable of returning equipment and parts practically back to their original specs and state. For the customer, this saves them an enormous amount of money in downtime, but also drastically reduces their greenhouse gas emissions because we use less energy, less water, and the equipment can then run for much longer after cleaning, rather than needing to repeat the process again.”
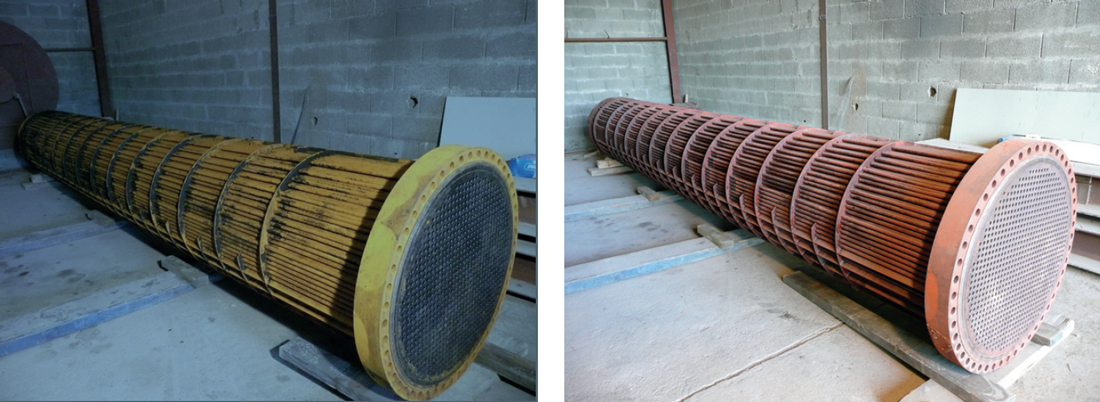
Proprietary solutions
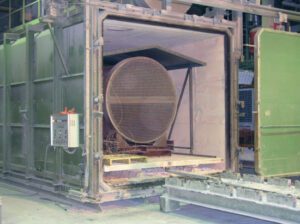
Many companies are active in thermal cleaning, but what sets Thermo-Clean apart are the specially prepared installations for very large and heavily polluted parts, the company states. “Together with an in-house system supplier, we have created these cleaning/pyrolysis ovens – they are specially made for Thermo-Clean and not available on the market,” says Robert. “This is our proprietary technology. We have developed special software to control the cleaning process; it is possible to clean special heat exchangers and bring them back to a very high level of performance which is not possible with other providers.”
Through a collaboration with TC Machinery BV, an installation was derived to ensure an effi cient and safe environment for the optimal thermal cleaning of heat exchangers. What makes these specially developed ovens unique to Thermo-Clean is the oxygen and temperature control which means the team can accurately monitor what happens during the gasifi cation of organic fouling. Thanks to the size of the installations, it is also possible for several exchangers to be cleaned at the same time, providing they are the same spec, size, and weight, and suffer from the same type of fouling.
Fouling: Organic, inorganic, or both?
“Thermal cleaning can tackle organic fouling and the combination of organic and inorganic.
When the fouling consists of organic and inorganic components, the organic component acts as a kind of glue in which the inorganic components attach themselves. Thermal cleaning converts the organic components into a powder, therefore releas-ing the inorganic components which can then easily be removed with high-pressure cleaning.
If only inorganic components are present in the fouling, thermal cleaning has only a little effect. However, we have noticed while testing that, for example, lime deposits after thermal cleaning become brittle and easier to rinse off with high pressure.”
(Source: ‘Thermal cleaning of heat exchangers, no alternative but a better way to clean’, Robert Mol, 2019)
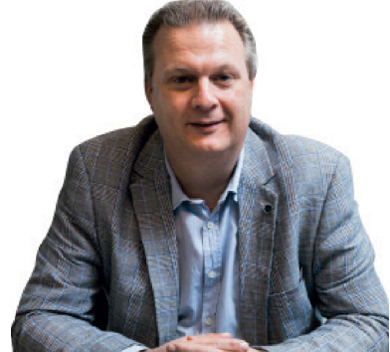
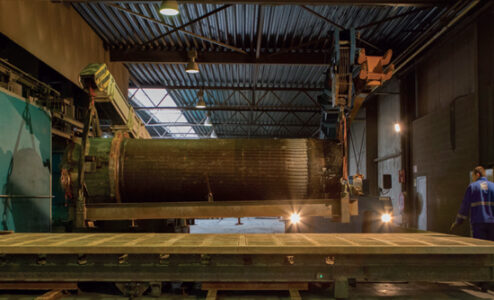
Good as new
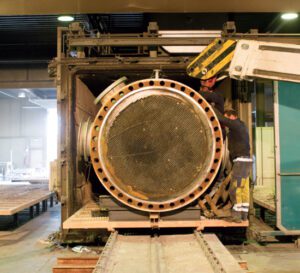
Thermo-Clean’s solution is not limited to heat exchangers but can also clean all types of process industry flow equipment, such as demisters, piping, external parts or filter cleaning.
“We see in today’s market is that companies who are not familiar with thermal cleaning are wary of this process as they are afraid of possible damage to their equipment. For many, they only have one heat exchanger, so I can understand this concern.” And how does Robert relieve this concern? He offers to clean a company’s disused, ‘scrapped’ heat exchanger.
“We put it in one of our ovens and we clean it. In many cases, our method can resurrect even the most fouled heat exchangers, and the customer can use this as a temporary replacement whilst we work on their in-service exchanger. Other times, the scrapped exchanger cannot be used again but we have cleaned it to a point where the metal and parts can be sold by the customer. Either way, we prove the capabilities of our thermal cleaning and the competency of our team.”
Responding to the future
In terms of the future, Thermo-Clean sees clear growth towards alternative cleaning techniques for heat exchangers, of which thermal cleaning will become increasingly important. Robert suggests that almost 80% of heat exchanger cleaning is carried out through high-pressure
cleaning methods. The remaining 20% is performed by chemical, mechanical, ultrasonic and thermal methods; the latter of which is used in less than 1% of cases today.
“High-pressure cleaning is the easiest to use, but has many drawbacks,” he explains. “For example, the vast amount of water consumed, which creates an enormous amount of waste and the performance of the cleaning is not optimal, because water cannot reach everywhere and thus leaves behind a lot of residual fouling in the exchanger.” The residual fouling results in a shorter service life of the equipment, because the exchanger will become contaminated again even faster than before. “What at first sight appears to be cheaper is in practice a lot more expensive and much more environmentally unfriendly. That is why we are seeing an increase in interest in alternative techniques, such as thermal cleaning.”
Thermo-Clean is preparing for the future by, amongst other things, equipping its existing factories with the right installations and tooling to increase capacity regionally. In addition, regions where clusters of chemical companies are located are also being investigated in order to set up thermal
cleaning centres locally by Thermo-Clean itself or with partners. The company aims to set up a new location every year to meet future demand.
“We are responding to this increase in demand by providing all our factories with the necessary equipment and training,” says Robert. “In addition, we are aiming for further expansion in regions with high demand to offer our techniques.”
About this Featured Story
This Featured Story was first published in Heat Exchanger World Magazine in May 2022. To read more Featured Stories and many other articles, subscribe to our print magazine.
Featured Stories are regularly shared with our Heat Exchanger World community. Join us and share your own Featured Story on Heat Exchanger World online and in print.