Tubular heat exchangers play a critical role in various industrial processes, facilitating efficient heat transfer between fluids. However, they are not immune to issues that can affect their performance and reliability. In the following sections, we will explain how to apply the following troubleshooting tips for tubular heat exchangers, focusing on five key problems: leakage due to poor service, leakage due to incorrect gaskets, leakage due to corrosion, contamination due to poor cleaning, and high pressure drop.
By Omari Hussein Sabuni, Mechanical Engineer – Kinyerezi Power Plant
Tubular heat exchangers are commonly classified into two main types:
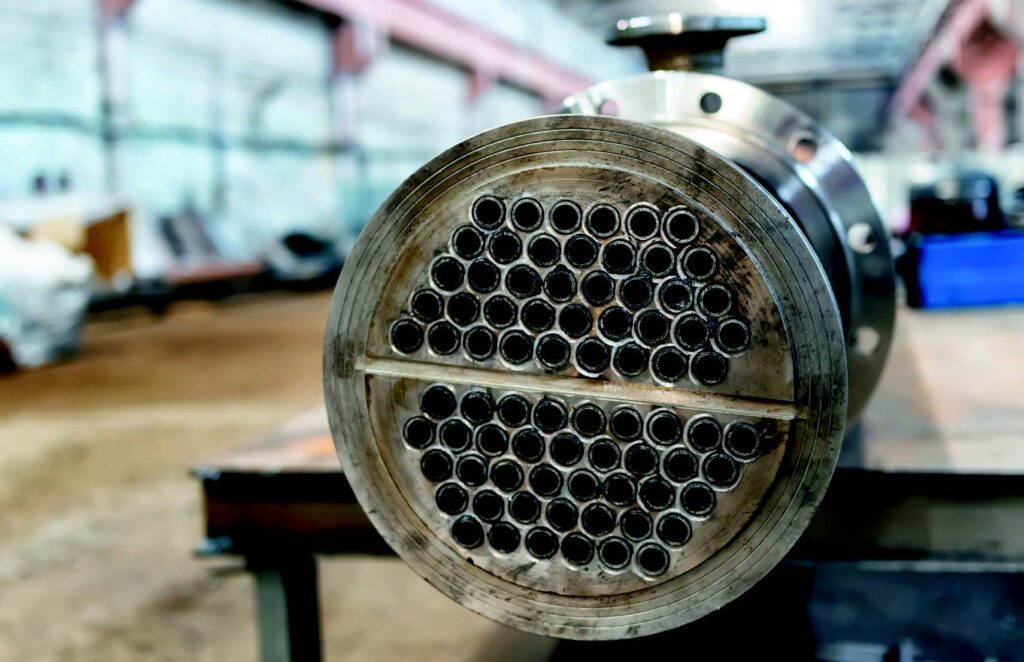
Shell and tube heat exchangers: This is the most common and widely used configuration. It consists of a cylindrical shell with a bundle of tubes inside. One fluid flows through the tubes (known as the tube-side fluid), while the other fluid flows around the tubes within the shell (known as the shell-side fluid). Heat is transferred between the fluids through the tube walls.
Shell and tube heat exchangers offer high thermal efficiency, versatility, and can handle a wide range of temperatures and pressures. They are used in various industries such as power generation, chemical processing, oil and gas, HVAC (Heating, Ventilation, and Air Conditioning), and refrigeration.
Finned tube heat exchangers: In finned tube heat exchangers, the heat transfer tubes are equipped with finned surfaces to increase the heat transfer area. These fins enhance heat transfer by improving convection between the tube surface and the fluid flowing over the fins. Finned tube heat exchangers are commonly used in applications where space limitations or airflow considerations require compact heat exchanger designs, such as air-cooled heat exchangers or refrigeration systems.
Parts of a tubular heat exchanger
A tubular heat exchanger consists of several key components, each serving a specific function in facilitating heat transfer between fluids. Here are the main components of a tubular heat exchanger and their functions:
Tubes: Tubes are the primary heat transfer elements in a tubular heat exchanger. They are typically made of metal (such as stainless steel, copper, or carbon steel) and form a bundle or assembly within the heat exchanger. The tubes allow the flow of fluids and facilitate the transfer of heat between the fluids.
Tube sheets: Tube sheets are thick plates that support and hold the tubes in place at both ends of the heat exchanger. They create a sealed barrier between the tube-side and shell-side fluids. Tube sheets provide structural integrity, prevent fluid mixing, and maintain the separation of the two fluid streams.
Shell: The shell is the outer housing or enclosure of the tubular heat exchanger. It surrounds the tube bundle and provides a space for the shell-side fluid to flow. The shell is designed to withstand the pressure and temperature of the shell-side fluid and to contain it within the heat exchanger.
Baffles: Baffles are plates or grids installed inside the shell to direct the flow of the shell-side fluid. They create a tortuous path for the fluid, enhancing heat transfer by promoting turbulent flow and preventing the bypassing of fluid across the tube bundle. Baffles also provide structural support to the tubes.
Tube support plates: Tube support plates are positioned within the heat exchanger to provide additional support for the tubes, preventing sagging or vibration during operation. They are typically placed at intervals along the length of the tube bundle and help maintain the tube alignment and spacing.
Inlet and outlet headers: The inlet and outlet headers are located at the ends of the heat exchanger and connect the tubes to the external piping system. They serve as entry and exit points for the fluids and ensure proper distribution and collection of the fluids within the heat exchanger.
Expansion joints: Expansion joints are flexible connectors installed in the tube-side piping to accommodate thermal expansion and contraction of the tubes. They allow for the movement of the tubes without causing stress or damage to the heat exchanger structure.
Insulation: Insulation is applied to the outer surface of the heat exchanger to minimize heat loss or gain to the surrounding environment. It helps maintain the desired temperature of the fluids and improves the overall energy efficiency of the heat exchanger.
Troubleshooting tubular heat exchangers
Troubleshooting tubular heat exchangers involves identifying and addressing issues that may affect their performance, efficiency, or reliability. When doing so, it is essential to follow a systematic procedure. Here is a suggested procedure for troubleshooting a tubular heat exchanger:
Identify the problem: Start by understanding the symptoms or issues affecting the heat exchanger. This could include leakage, reduced heat transfer efficiency, high pressure drop, or other anomalies. Gather as much information as possible about the problem, including when it started, any changes in operating conditions, or any recent maintenance activities.
Visual inspection: Perform a thorough visual inspection of the heat exchanger. Look for any visible signs of damage, leakage, corrosion, fouling, or blockages. Check for loose connections, damaged gaskets, or any other apparent issues that could contribute to the problem.
Review operating conditions: Review the operating parameters of the heat exchanger, including fluid temperatures, flow rates, pressures, and any control settings. Compare these values to the design specifications or normal operating conditions to identify any deviations.
Analyze fluid parameters: Monitor and analyze the fluid parameters on both the tube-side and shell-side, including temperature differentials, pressure drops, and flow rates. Use instrumentation or gauges to measure these values accurately. Look for any abnormalities or variations from the expected values.
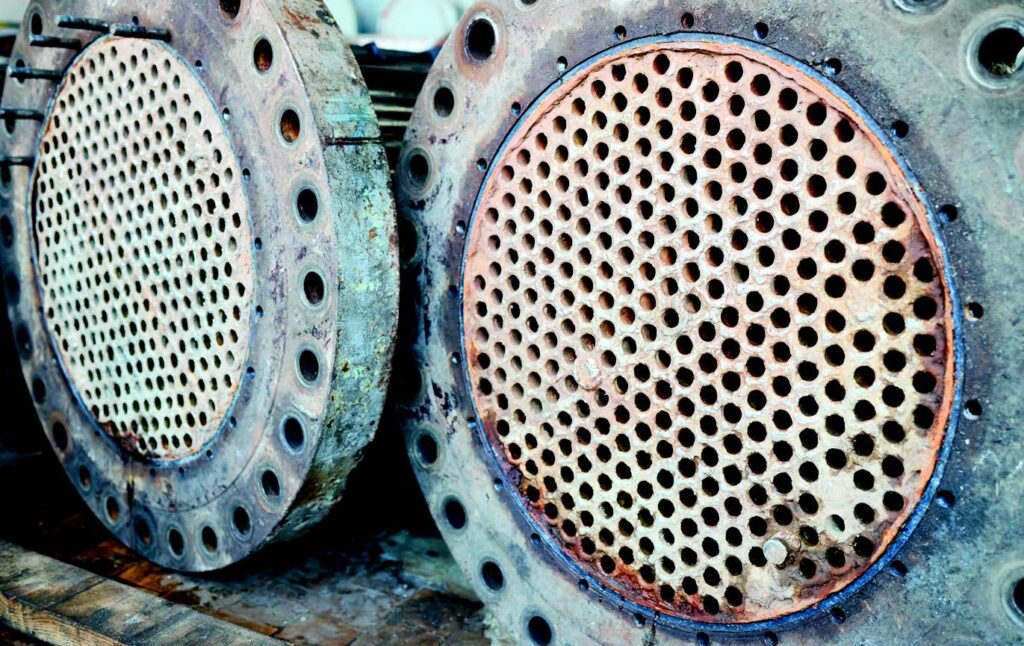
Review maintenance history: Examine the maintenance history of the heat exchanger. Check for any recent maintenance activities, including cleaning, gasket replacements, or repairs. Assess whether these activities could have contributed to the current problem or if they were performed correctly.
Conduct non-destructive testing (NDT): If necessary, perform non-destructive testing techniques such as ultrasonic testing, magnetic particle inspection, or dye penetrant testing to assess the integrity of the tubes, tube sheets, or other critical components. These tests can help identify hidden defects or damage that may not be visible during the visual inspection.
Address common issues: Based on the findings from the visual inspection, analysis of operating conditions, fluid parameters, and NDT results, address common issues that could be causing the problem. This may involve repairing leaks, replacing damaged gaskets, cleaning fouling or deposits, or correcting flow imbalances.
Seek expert assistance: If the troubleshooting process does not lead to a clear resolution or if the problem requires specialized knowledge or expertise, it is advisable to seek assistance from qualified technicians, engineers, or heat exchanger specialists. They can provide further guidance and expertise to diagnose and resolve complex or persistent issues.
Monitor and verify: After implementing any necessary repairs or corrective measures, closely monitor the performance of the heat exchanger. Verify that the problem has been resolved and that the heat exchanger is operating within the desired parameters. Continuously monitor the heat exchanger’s performance to ensure long-term reliability and efficiency.
Leakage due to poor service
Safety first: Ensure you follow appropriate safety procedures, such as wearing protective gear and isolating the equipment from the power source or any hazardous substances.
Visual inspection: Begin by visually inspecting the heat exchanger for any visible signs of leakage, such as drips, wet spots, or discoloration around the tubes, joints, or seals. Make sure to examine both the internal and external parts of the heat exchanger.
Check gaskets and seals: Gaskets and seals play a crucial role in preventing leaks. Inspect them for signs of wear, damage, or misalignment. Replace any damaged gaskets or seals as necessary.
Tighten connections: Use appropriate tools to check and tighten the connections of the tubes, flanges, and other components. Over time, these connections may become loose and contribute to leakage.
Pressure test: Perform a pressure test to assess the integrity of the heat exchanger. Use a suitable method to apply pressure to the system and monitor for any pressure drops, indicating potential leaks. This test can help pinpoint the location of the leakage.
Inspect tube integrity: Inspect the tubes themselves for any signs of corrosion, erosion, or mechanical damage. Pay particular attention to areas near bends, joints, or tube sheet connections. Replace any compromised tubes to prevent leaks.
Cleaning and maintenance: Poor service can lead to fouling and blockages, which can cause leaks. Regularly clean the heat exchanger to remove scale, deposits, or any foreign materials that may obstruct the tubes or affect their performance.
Consider fluid properties: Review the properties of the fluids flowing through the heat exchanger. Certain fluid characteristics, such as high temperature, corrosiveness, or excessive velocity, can contribute to leakage. Adjust operating conditions or choose appropriate materials that can withstand these conditions.
Seek professional assistance: If you are unable to identify or resolve the leakage issue, it is advisable to seek help from a qualified technician or heat exchanger specialist. They can provide further guidance, conduct more in-depth inspections, and offer repair or replacement solutions.
Leakage due to incorrect gaskets
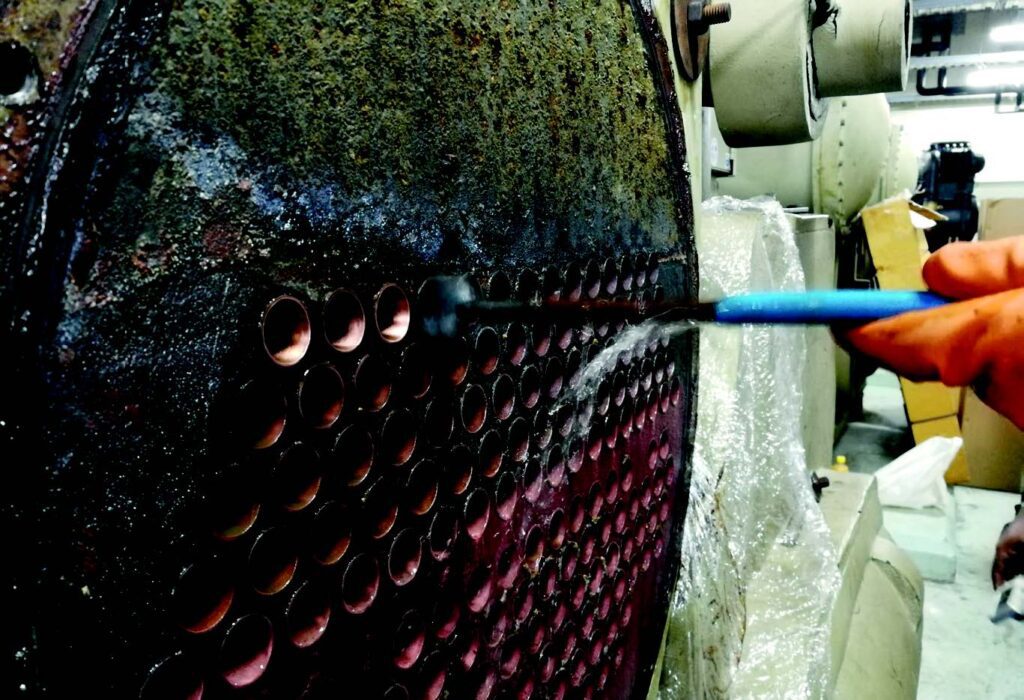
Identify the problem: Leakage is usually evident by visible signs of fluid seeping or spraying around the gasket area. Inspect the heat exchanger thoroughly to confirm that the leakage is indeed caused by the gasket.
Examine the gasket: Carefully inspect the gasket for any signs of damage, such as cracks, tears, or deformities. Additionally, check if the gasket material is compatible with the process fluids and operating conditions.
Verify gasket specifications: Compare the gasket installed with the manufacturer’s specifications and recommended gasket material. Ensure that the correct gasket size, type, and material are being used for the specific heat exchanger application.
Torque check: Improper gasket installation or inadequate tightening can lead to leakage. Verify if the gasket is correctly seated and tightened to the recommended torque value. Consider using a torque wrench to ensure proper tightening.
Clean mating surfaces: Residue, corrosion, or foreign particles on the heat exchanger’s flange surfaces can prevent the gasket from forming a proper seal. Clean the mating surfaces thoroughly using a suitable solvent or cleaning agent.
Gasket alignment: Ensure that the gasket is correctly aligned within the flange grooves. Misalignment can result in uneven pressure distribution and cause leakage. Adjust the gasket position if necessary.
Consider gasket lubrication: Some gasket materials benefit from a thin layer of lubricant to improve sealing performance. Check the gasket manufacturer’s recommendations regarding lubrication and apply it if required.
Gasket replacement: If the gasket is damaged or incompatible, it may be necessary to replace it entirely. Follow proper procedures for gasket removal, installation, and tightening to ensure a reliable seal.
Test the repaired heat exchanger: After addressing the gasket issue, perform a thorough inspection and conduct a pressure test to verify that the leakage problem has been resolved. Monitor the heat exchanger during normal operation to ensure continued leak-free performance.
Leakage due to corrosion
Visual inspection: Perform a thorough visual inspection of the heat exchanger to identify any signs of corrosion. Look for rust, discoloration, pitting, or any visible damage on the tubes, tube sheets, and other components.
Pressure testing: Conduct a pressure test on the heat exchanger to identify the location and extent of the leakage. This can be done by pressurizing the system with air or water and observing for any drops in pressure. A pressure drop can indicate the presence of a leak.
Tube cleaning: Corrosion can often be accelerated by fouling and deposits on the heat exchanger tubes. Clean the tubes using appropriate methods such as mechanical brushing, chemical cleaning, or high-pressure water jetting. This helps remove deposits and reduces the chances of corrosion.
Chemical treatment: Implement a chemical treatment program to inhibit corrosion. Corrosion inhibitors can be added to the heat exchanger system to protect the metal surfaces from corrosive elements. Consult with a chemical specialist to determine the most suitable inhibitor for your specific heat exchanger and operating conditions.
Material evaluation: Assess the materials used in the heat exchanger construction. Certain metals and alloys are more resistant to corrosion than others. Consider using corrosion-resistant materials such as stainless steel or titanium for the tubes or tube sheets in areas prone to corrosion.
Coatings and linings: Applying protective coatings or linings to the internal surfaces of the heat exchanger can provide an additional barrier against corrosion. These coatings create
a protective layer that prevents direct contact between the metal surface and corrosive fluids.
Regular maintenance: Establish a routine maintenance schedule to inspect and maintain the heat exchanger. This includes cleaning, chemical treatment, and inspection of components to detect early signs of corrosion. Prompt action can prevent corrosion-related leaks from worsening.
Environmental factors: Consider environmental factors that can contribute to corrosion, such as moisture, temperature, and the presence of corrosive substances in the process fluid. Take measures to control these factors, such as installing insulation, maintaining proper ventilation, or modifying the fluid chemistry.
Repair or replacement: In cases where the corrosion damage is severe or extensive, repair or replacement of affected components may be necessary. Consult with a qualified technician or engineer to assess the extent of damage and determine the most appropriate course of action.
Contamination due to poor cleaning
Visual inspection: Conduct a thorough visual inspection of the heat exchanger to look for any signs of fouling or deposits. This may include inspecting the tubes, headers, and any access points for accumulation of dirt, debris, or scale.
Pressure drop analysis: Measure the pressure drop across the heat exchanger. Higher than normal pressure drop can indicate fouling or blockage caused by poor cleaning. Compare the measured pressure drop with the design specifications to identify any discrepancies.
Temperature analysis: Monitor the temperatures at the inlet and outlet of the heat exchanger. A significant increase in temperature differential may suggest fouling, as it can impede heat transfer. Compare the measured temperatures with the expected values to identify any deviations.
Flow rate measurement: Measure the flow rates of the fluid entering and leaving the heat exchanger. A decrease in flow rate can indicate fouling or blockage. Compare the measured flow rates with the design specifications to identify any discrepancies.
Chemical analysis: Conduct a chemical analysis of the fluid flowing through the heat exchanger. This analysis can help identify the presence of contaminants or scaling agents. A laboratory analysis of the fluid sample can provide insights into the nature of the fouling and guide appropriate cleaning methods.
Cleaning method evaluation: Review the cleaning methods and procedures currently employed. Evaluate their effectiveness and determine if they are suitable for the type of fouling observed. Consider alternative cleaning techniques such as mechanical cleaning, chemical cleaning, or high-pressure water jetting, depending on the nature of the contamination.
Cleaning frequency: Assess the cleaning frequency of the heat exchanger. Poor cleaning practices often result from infrequent or inadequate cleaning routines. Adjust the cleaning schedule to ensure that the heat exchanger is cleaned regularly and thoroughly, taking into account the operating conditions and the fouling propensity of the fluids being processed.
Training and education: Provide training to personnel responsible for cleaning the heat exchanger. Ensure they understand the importance of proper cleaning procedures and the potential consequences of poor cleaning practices. Emphasize the use of appropriate cleaning agents, tools, and techniques to prevent or remove fouling effectively.
Monitoring and maintenance: Implement a monitoring and maintenance program for the heat exchanger. Regularly inspect the equipment, record and analyze performance data, and conduct preventive maintenance to minimize fouling and ensure optimal heat transfer efficiency.
High pressure drop
Check fluid flow rates: Ensure that the flow rates of both the hot and cold fluids are within the design specifications. Verify if there are any deviations from the expected flow rates, as this can directly affect the pressure drop.
Inspect fouling or scaling: Fouling or scaling on the inner surface of the tubes can restrict fluid flow and lead to high pressure drop. Conduct a thorough inspection of the tubes to identify any deposits or build-up. Clean the tubes if necessary or consider implementing a regular maintenance schedule to prevent fouling.
Examine tube integrity: Inspect the tubes for any damage or deformation that may cause an obstruction to the fluid flow. Look for signs of corrosion, erosion, or physical deformities such as dents or bends. Damaged tubes should be repaired or replaced to restore proper flow and reduce pressure drop.
Evaluate tube roughness: The roughness of the inner tube surface can impact pressure drop. Check the tube specifications and compare them to the expected roughness values. If the roughness is higher than anticipated, it could lead to increased friction and pressure drop. In such cases, consider polishing or replacing the tubes to reduce roughness.
Verify tube diameter and length: Confirm that the tube dimensions are correct according to the design specifications. Incorrect tube diameter or length can result in increased pressure drop. Ensure that the actual dimensions align with the required dimensions and make adjustments if necessary.
Examine the presence of blockages: Check for any blockages or obstructions in the heat exchanger, such as debris, foreign objects, or misplaced components. These blockages can disrupt fluid flow and lead to higher pressure drop. Remove any obstructions and ensure the exchanger is clear and properly assembled.
Evaluate the design parameters: Review the design parameters of the heat exchanger, such as tube layout, number of passes, and baffle design. In some cases, a poor design or mismatched specifications can contribute to high pressure drop. Consult the original design documentation or an expert to assess if any modifications or improvements are necessary.
Consider operational conditions: Assess the operational conditions of the heat exchanger, including temperature, pressure, and fluid properties. Deviations from the expected operating conditions can influence pressure drop. Make sure the exchanger is operating within the intended range and investigate any anomalies.
Perform calculations and simulations: Utilize fluid dynamics calculations or simulations to model the flow behavior within the heat exchanger. This can help identify potential areas of high pressure drop and guide troubleshooting efforts. Consult with a qualified engineer or utilize specialized software if needed.
Conclusion
By following this detailed troubleshooting procedure, you can systematically identify and resolve issues with a tubular heat exchanger, ensuring optimal performance and efficient heat transfer.
About the author
Omari Hussein Sabuni is an experienced mechanical engineer at Kinyerezi Gas Power Plant, specializing in heat exchanger design, optimization, troubleshooting and providing practical solutions for various heat exchanger problems. He is skilled in analyzing thermal systems and developing innovative solutions to enhance heat transfer efficiency and adept at conducting feasibility studies, performing risk assessments, and ensuring compliance with industry standards.