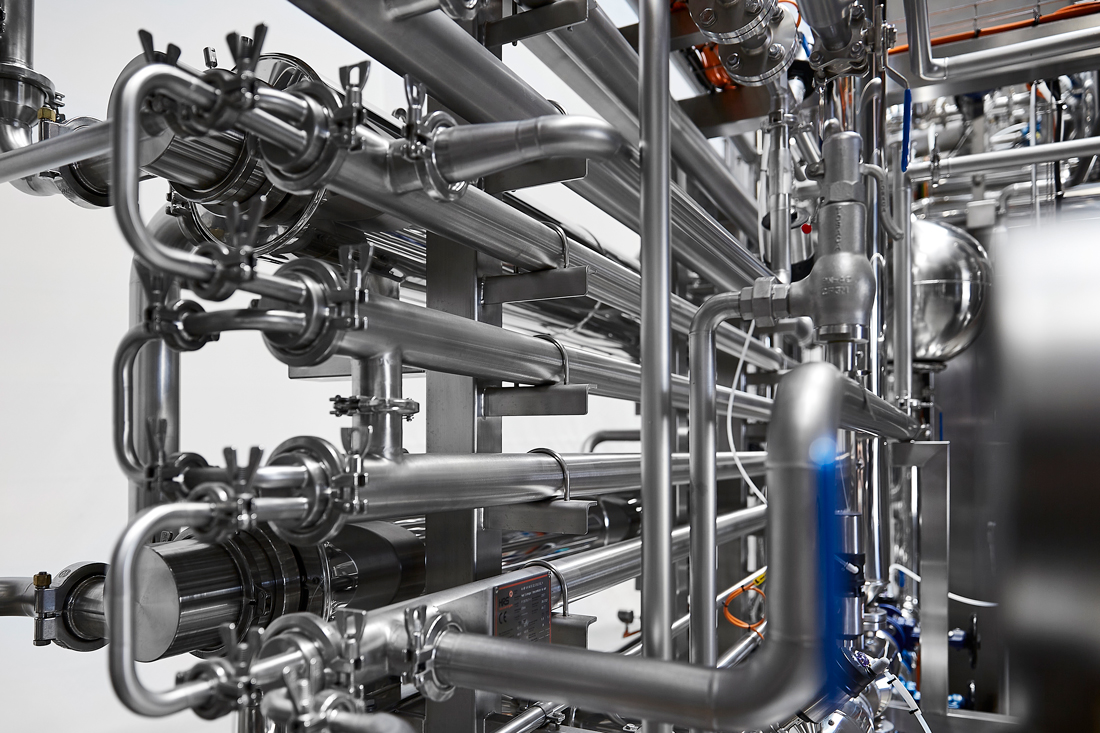
By Matt Hale, International Sales & Marketing Director, HRS Heat Exchangers
When it comes to choosing the right heat exchanger, the biggest factor is the nature of the materials being processed and the client’s requirements for the finished product – something that we refer to as the product identity.
Different materials have different handling requirements, and while the process being undertaken (for example cooling or pasteurisation) is also an important consideration, product identity is the most important consideration for both the client and our engineers. With materials handled ranging from simple fluids through to complex viscous liquids, emulsions and materials containing large particles which must remain intact, there is no ‘one size fits all’ solution. That is why HRS produces a range of tubular heat exchangers, from simple multi-tube designs through to scraped surface designs which are capable of dealing with high-fouling materials while maintaining product integrity.
Determine by viscosity
For the simplest fluids, such as milk, smoothies and juices, we have multi-tube designs including the MI Series and the MR Series. As materials become more viscous in nature (such as honey, soups and creams), we then move up through the range using tube-in-tube or annular space designs such as the DTA or AS Series respectively. For the most viscous materials with high fouling potential, you need a scraped surface heat exchanger such as our R Series or patented Unicus Series.
For materials containing particles or pieces, such as compotes or diced fruit, things become more complicated.