Fouling costs and benefits of mitigation
In this series of articles we will look at how heat exchangers foul, how to understand the root causes of fouling, and how to mitigate the impact of fouling. The material presented is based entirely on the author’s experience and analysis of operating situations in the Oil & Gas industry. However, many theories and varied experiences exist across the industry and amongst researchers.
By Himanshu Joshi, Heat Exchanger Specialist
If decisions have to be made related to heat exchanger fouling – should any action be taken, what action, can the cost be justified – it is necessary to know how much the fouling issue costs and how much the action will cost. There are many components to the cost (economic losses) of fouling, but not all may be applicable in a given situation or some might dominate over others. It is important to quantify the major costs to decide what actions to take to minimize the costs. That action could be the use of mitigation techniques (parts 4 & 5), cleaning (part 6), or a redesign of the heat exchanger. All these actions have their associated costs which must be justified based on how much of the losses due to fouling can be recovered. If a heat exchanger fouls it loses its ability to deliver the required heat duty, and that loss of heat duty has many consequences. Table 1 describes the various types of losses and Table 2 lists the costs to consider when applying a mitigation technique.
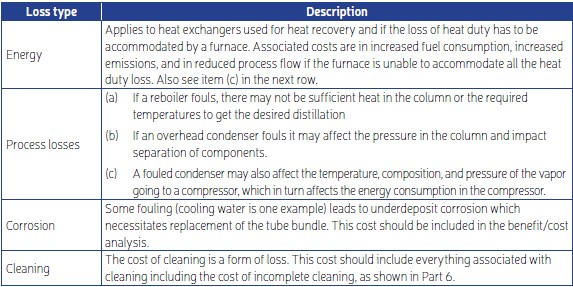
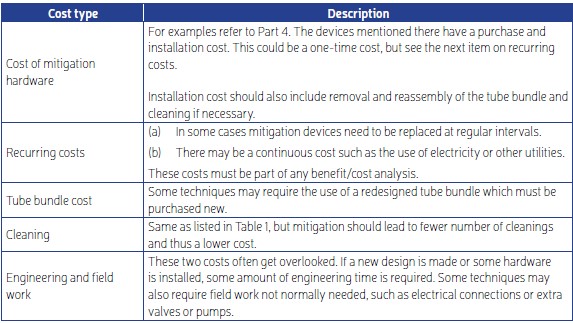
Benefit vs cost
To evaluate the economic benefit of an action against fouling, the first step is to add up all the costs from Table 1. This can be looked at as the cost of doing nothing, as it represents the situation as it exists. This cost should be projected over some future period, with the current cleaning interval being a good time frame to use. But one year, or six months for severe fouling, can also be reasonably used.
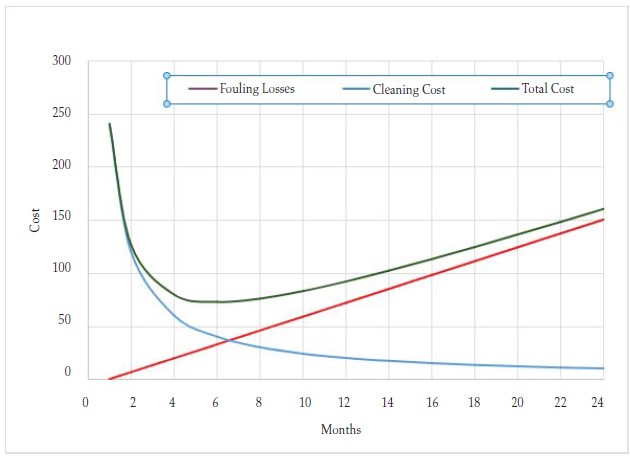
Next, evaluate the costs associated with all the relevant items in Table 2, remembering to include recurring costs. It is especially important to consider all costs when comparing alternative actions for mitigation. A simple indicator to compare two mitigation methods is the ratio of benefit vs cost, evaluated over the same time frame. A more meaningful calculation will consider a life-cycle cost, projected over as many as 25 years.
Optimum cleaning interval
If cleaning is the only action to be taken, the time to clean can be optimized by combining the costs and benefits as shown in Fig. 1. This analysis is relatively simple for a single heat exchanger but requires software when networks are involved, because of the Figure 1 shows that the more frequently you clean the higher the cost of cleaning (blue line) but lower the losses due to fouling (red line). The sum of these two is the total cost (green line) which shows a minimum at 6 months, the optimum cleaning time.
Summary
There are many types of losses when a heat exchanger fouls, and many types of costs when some mitigation action is taken. All costs should be considered when making decisions about mitigation actions, including cleaning. Such an approach will identify the most cost effective actions and allow for economically better decisions.
Upcoming in Part 9
We will look at design specifications and practices used to guard against fouling and provide some guidelines for good designs that minimize fouling.
Catch up on Fouling Focus!
Have you missed the earlier installments of this multi-part series? All articles are available in our online archive:
Part 1 – https://heat-exchanger-world.com/heat-exchanger-fouling-in-practice-understand-mitigate-1/
Part 2 – https://heat-exchanger-world.com/heat-exchanger-fouling-in-practice-understand-and-mitigate-part-2/
Part 3 – https://heat-exchanger-world.com/heat-exchanger-fouling-in-practice-understand-and-mitigate-part-3/
Part 4 – https://heat-exchanger-world.com/heat-exchanger-fouling-in-practice-understand-and-mitigate-part-4/
Part 5 – https://heat-exchanger-world.com/heat-exchanger-fouling-in-practice-understand-mitigate-part-5/
Part 6 – https://heat-exchanger-world.com/heat-exchanger-fouling-in-practice-understand-mitigate-part-6/
Part 7 – https://heat-exchanger-world.com/heat-exchanger-fouling-in-practice-understand-mitigate-part-7/
About the authors
Himanshu Joshi retired from Shell in 2021 after 34 combined years with ExxonMobil and Shell, during which he specialized in heat exchangers and fouling. He was part of a team that was granted a patent related to fouling deposit analysis at ExxonMobil, and led applied fouling R&D projects at both companies. He has made several presentations about the field aspects of fouling and fouling mitigation, and deployed many mitigation technologies in the field. He can be reached by email at alph.hmj@gmail.com.
About this Technical Story
This Technical Story was first published in Heat Exchanger World Magazine in June 2024. To read more Technical Stories and many other articles, subscribe to our print magazine.
Technical Stories are regularly shared with our Heat Exchanger World community. Join us and share your own Technical Story on Heat Exchanger World online and in print.