While larger medium voltage process heaters are relatively new in hydrocarbon processing, the safety issues surrounding medium-voltage equipment are well known. Arc flash events are a prime example of a rare but potentially deadly situation that can be mitigated with the right technology.
By Michael Jones – Staff Engineer, Watlow
As process heaters become a popular alternative for larger applications that have historically utilized gas-fired heaters, it is important to look at the ways in which they incorporate arc flash mitigation features.
When medium- or high-voltage equipment is used for industrial applications, it carries with it certain risks. Arc flash is an example of a well-known electrical risk that requires certain best practices to be followed to minimize damage and injury.
When a new piece of medium-voltage equipment is devel-oped, special attention should be given to such risks. This is certainly the case for large electric process heaters, which are becoming more popular in hydrocarbon processing applications.
Clean ducts, improved air quality, better performance
Arc flashes typically occur when there is a short circuit in a system (due to, for example, a dropped tool, buildup of corrosion or conductive dust or the presence of pests). If the voltage is high enough, and if there is a path to ground or a lower voltage, the resistance of the air is overcome and results in an arc.
Arc flash events can result in significant damage. As the energy release increases, it can cause fire and injury. If the energy release is high enough molten conductor metal and high-pressure plasma energy can escape from the cabinet, posing a risk to personnel.
The potential arc flash energy is determined by several factors: Equipment voltage, available current and the duration of the event. As the equipment voltage increases, the potential for arc flash hazards also increases. Low voltage systems operating below 400 volts do not have the energy to cause a significant arc flash hazard. Equipment operating at voltages between 400 volts and 600 volts can cause arc flash hazards, but their capacity to cause massive energy release is limited. Equipment operating at medium voltage (above 600 volts) has a high capacity for energy release. The available current is determined by the feed equipment upstream.
While it may be practical in some cases to reduce the potential arc flash energy while limiting voltage or current, over-all project cost can make this difficult. This makes reducing the duration of the event the most practical approach. Reducing the duration of the arc event also reduces the area of damage. The area of impact is not limited to the explosive blasts. The arc flash produces intense heat and light energy. People in the vicinity of the blast can experience injury from these effects even if they are not exposed directly to the explosion. Equipment surfaces can absorb the energy and experience high temperatures from the radiant energy, causing damage and requiring repair. Although arc flash incidents are relatively rare, their potential for damage, injury and death makes them a huge concern. Some estimates put the incidence of arc flash events roughly between five to 10 per day worldwide, or 3,500 per year. According to a 2021 article in the journal Safety, there were over 2,000 recorded hospitalizations in the U.S. due to electrical injuries, including arc flashes. Of these, 1,900 were non-fatal and 166 were fatal1. Although the article did not qualify fatalities in terms of whether they were due to arc flashes or other events, it is clear that arc flashes are on the more lethal end of the spectrum. Are there special risks with regard to arc flashes when it comes to process heating? Yes and no. On the one hand, medium voltage process heaters are relatively new to many applications. Concerns about decarbonization, automation and safety have driven many to replace gas-fired heaters with larger electrical heaters (> one megawatt)2; these heaters thus represent a potential new source of risk, and manufacturers of these heaters must be aware of that risk. On top of that, many applications use arrays of large megawatt heaters, connected to multiple panels. This drives the need for a solution that can isolate the specific panel(s) where arc flash occurs, isolating faults from the main breaker/feeder where possible.
On the other hand, arc flash events are well understood, as are the strategies for reducing their effects. An understanding of these strategies should be “built in” to any technology for process heating.
1Casey, Tristan W., Hannah M. Mason, Jasmine Huang, and Richard C. Franklin. 2021. “Shaping Frontline Practices: A Scoping Review of Human Factors Implicated in Electrical Safety Incidents” Safety 7, no. 4: 76. https://doi.org/10.3390/safety7040076.
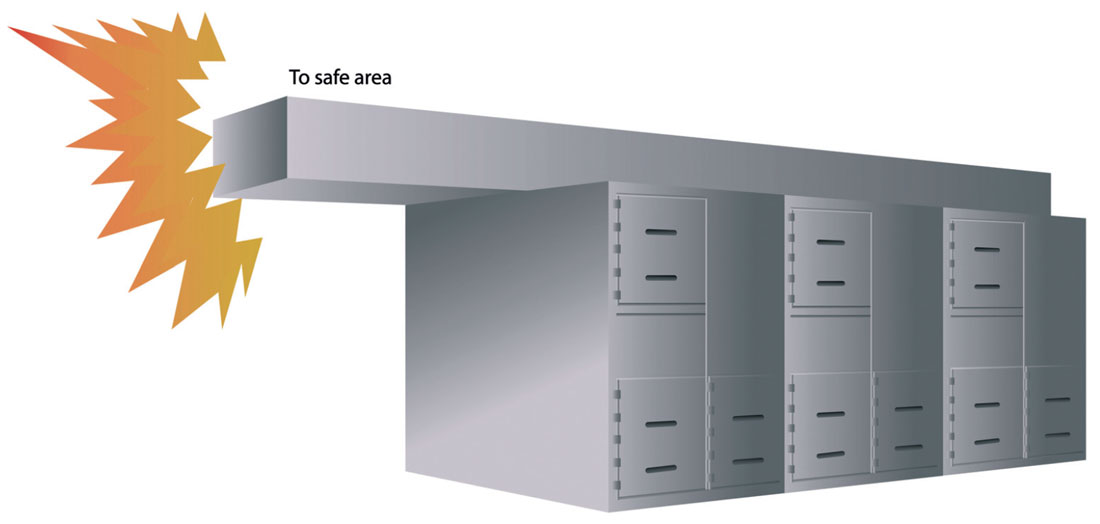
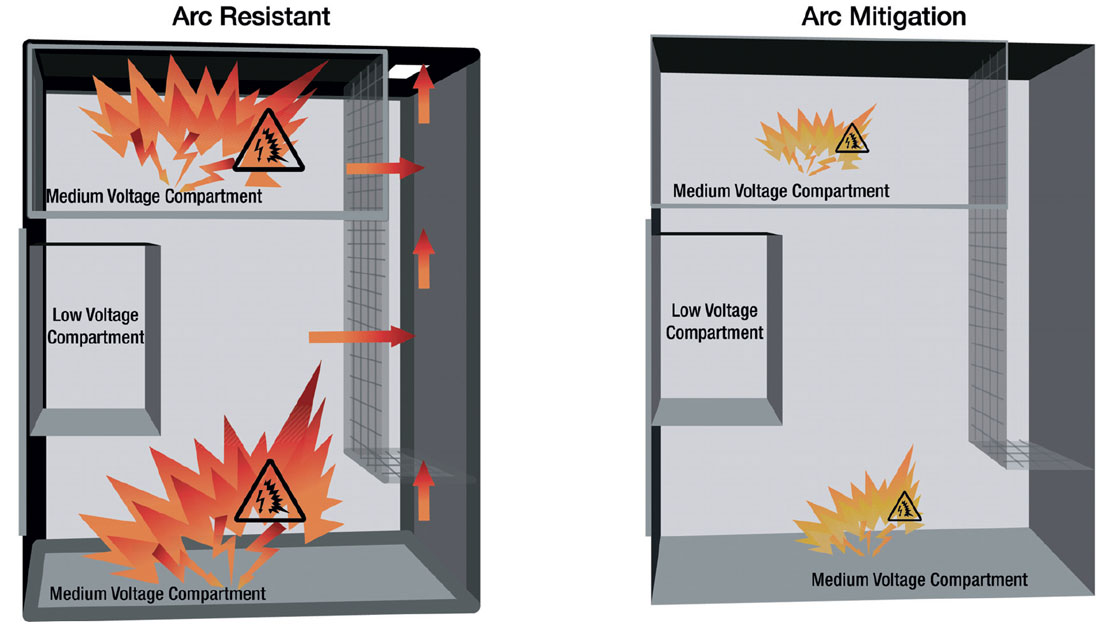
Reducing the effects of an arc flash event
Generally speaking, there are three main strategies for reducing the effects of any potential arc flashes that could occur with a piece of equipment:
1. Increasing the distance from the potential source of an event
2. Reducing the available fault current
3. Decreasing the duration of the event (i.e., how long the arc itself exists)
Ideally, all could be used in combination to ensure maximum safety, but this is often not practical when considering overall project cost.
That said, the duration of the event is the most practical influencer to reduce and has the largest impact on the total amount of energy released. Reducing the overall fault clearing time is often the best, most direct way to reduce arc flash hazards. This point can be illustrated through a comparison between two current approaches to limiting the damage wrought by arc flashes: Arc-resistant cabinets and arc mitigation technologies. Mitigation technologies make more sense economically and from a safety perspective, and thus should be incorporated into designs for and around medium voltage process heaters and similar equipment.
Arc-resistant cabinets
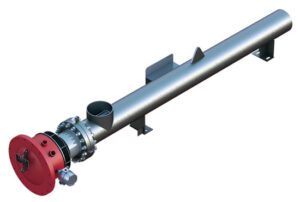
The idea behind an arc-resistant cabinet is to reduce exposure to arc events by encasing the system in a metal-clad cabinet with a venting system. Typically, the doors of the cabinet are the point of failure in an arc event: Rapidly heated air expands and builds up pressure inside the cabinet, eventually causing the doors to blow open and exposing those nearby to heat and blast. With an arc-resistant cabinet, the flash energy (more precisely, the heated gas and pressure) is redirected through a duct near the top of the cabinet. When the doors are closed and all covers are installed correctly, arc-resistant cabinets reduce the energy to which people and other pieces of equipment are exposed.
That said, arc resistance does not actually limit the energy from the event itself—it merely redirects it. There can still be substantial damage to the system itself, as well as significant risk.
But perhaps the greatest drawback is the fact that the system must be closed for the arc-resistant cabinet to work; it will not work, for example, with the doors open. This is a problem, as many arc events occur during maintenance, precisely when the doors are open. An arc-resistant cabinet will not afford any additional protection in these cases.
Of course, there are other issues as well: The size and weight of the cabinet, the certification needed (ANSI C37.20.7), and, naturally, the overall cost.
2Long, Dennis and Roly Juliano (2022). “Electrification and Medium Voltage Process Heaters Systems.” White paper, https://de.watlow.com/blog/posts/electrification-and-medium-voltage-process-heater-systems
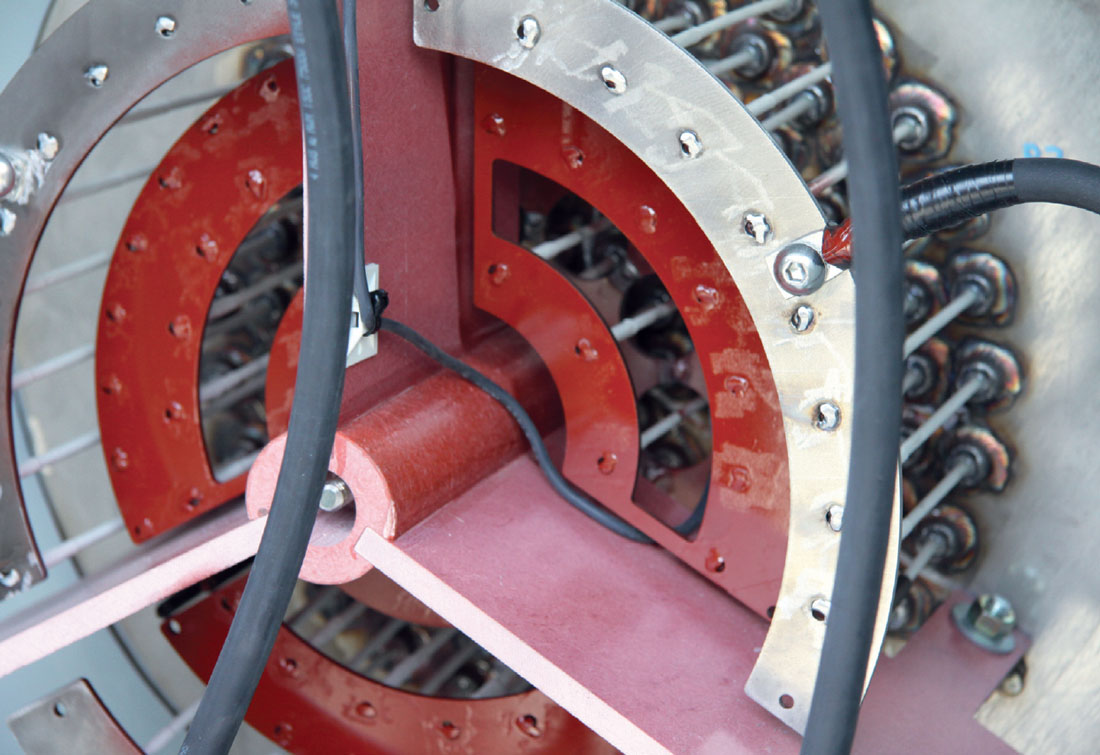
Arc flash mitigation technologies
Arc flash mitigation technologies (hereafter arc mitigation) take a different approach; instead of redirecting the energy from the event, arc mitigation seeks to reduce the energy of the event itself by limiting its duration. This is done by detecting the arc flash early and automatically tripping the appropriate circuit.
This can be done in two ways – sensing current (referred to as current arc mitigation) or sensing light (referred to as optical arc mitigation).
In optical arc mitigation, the light emitted by the arc within the enclosure builds quickly. That light can be detected by a photoelectric receptor or length of fiber optic cable, even in the early stages of the event. When detected, the signal is then sent to a protective relay, which trips the breaker automatically, without the need for human intervention.
One of the main advantages of this approach is that it is independent of the actual magnitude of the arcing fault current. This allows the system to detect arcing in an early stage of its development and trigger the break sooner, which in turn limits the duration of the event and hence the total energy produced. Current arc mitigation uses current transducers to sense an increase in current produced by the arc. If the transducers are not sized correctly, they may not shut the system down or may be unable to clear the event.
Even when current transducers are properly sized, optical arc mitigation offers an advantage in clearing time over current arc mitigation. Optical sensing can reduce clearing time and arc energy release by 50% over current transducers. However, a current arc mitigation is preferred over having no arc mitigation components integrated into the control system. If no arc mitigation is integrated into the control system, upstream equipment with undetermined clearing time will need to be configured to respond to an arc event.
Unlike the arc-resistant cabinet, arc mitigation also reduces damage to equipment (instead of simply redirecting the energy that escapes the cabinet).
It can function even when the doors are open and maintenance is being performed, and it does not require the heavy metal-clad cabinet with its larger footprint.
For example, in the POWERSAFE™ system developed at Watlow® for medium voltage process heaters, sensors can be placed within the thermal controller, SCR node and/or single contactor node, all of which are protected by a feeder/breaker. Up to 12 heaters may be run from a single feeder/breaker, with each heater controlled by its own hub or switching circuit node. When the sensor senses an arc flash event in any compartment, the feeder/breaker will shut down the lineup to limit damage caused by the arc.
Takeaways
Again, arc flashes are well understood, and industries using medium-voltage equipment should already be aware of strategies to increase distance from such events, reduce current or decrease the duration of the event (as well as the appropriate use of PPE). As medium voltage process heaters become more popular in hydrocarbon processing, they too must be designed with safety in mind. Arc mitigation technologies represent the best approach here, as they actually decrease the duration of arc flash events and hence the energy released, helping to minimize the damage and risk involved. Additionally, such technologies can achieve these things with minimum footprint and project cost.
About the author
Mike Jones is a New Product Development Engineer who has a passion for collaborating with end users and teams to bring solutions to market. Mike is enthusiastic about developing heating solutions that enable replacement of carbon-emitting heaters with heat generated through renewable sources. He currently leads the development and introduction of Watlow’s POWERSAFE™ Medium Voltage thermal system, a solution that helps end users reliably transition MW size gas-fired process heat-ers to electric.