In this case study, TAPROGGE* explains how it was able to achieve up to zero-fouling operations at a dairy plant by using its KLAREN self-cleaning heat exchanger technology.
All text and images provided by TAPROGGE GbmH
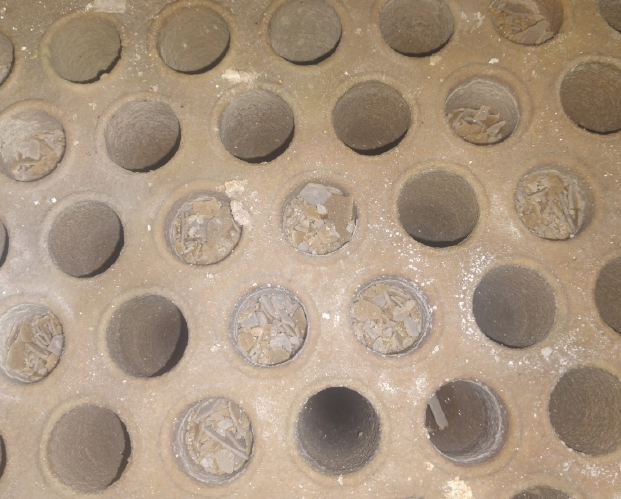

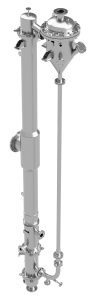
A dairy plant in the USA suffered from severe fouling of three condensers used for condensing the vapor of a multieffect falling film evaporator due to hard well water used for the cooling process. Hard well water is water that originates from a well and contains a high mineral content, especially calcium and magnesium ions. When hard water is employed as a coolant in a condenser, these minerals can scale on the surfaces, diminishing the efficiency of heat transfer and potentially causing operational issues.
Problem
The hard well water that is applied in the condensers has a hardness of 7-8 grain per gallon (gpg) and led to rapid scaling, reducing the cooling capacity significantly in a matter of days. One grain per gallon (gpg) is equivalent to 17.14 parts per million (ppm). Water hardness can be measured in gpg or ppm, but gpg is the most used measurement. Various conventional solutions (for example regular cleaning, optimizing process conditions, etc.) had been tried by the customer to prevent this fouling problem, however without success. Plant management decided to replace their fouling conventional condensers by self-cleaning fluidized bed heat exchangers.
Results
All three exchangers went into operation without any problems and were only opened once to twice a year for inspection. The units operate 85% of the time and are still running (as of 2023 from 1988) to the satisfaction of the customer. The plant expresses that they are satisfied with the performance and operation of the heat exchanger. Fouling has never been observed, contrary to earlier experiences with conventional exchangers that required a lot of maintenance on a regular basis. The self-cleaning heat exchanger technology helped the customer to achieve up to zero-fouling operations.
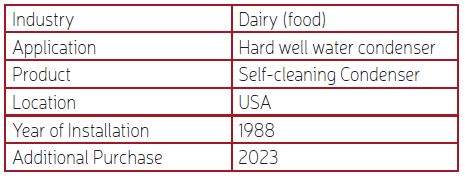
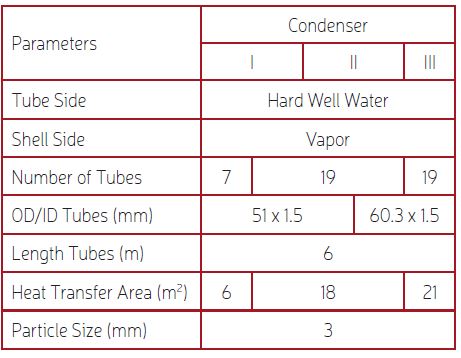
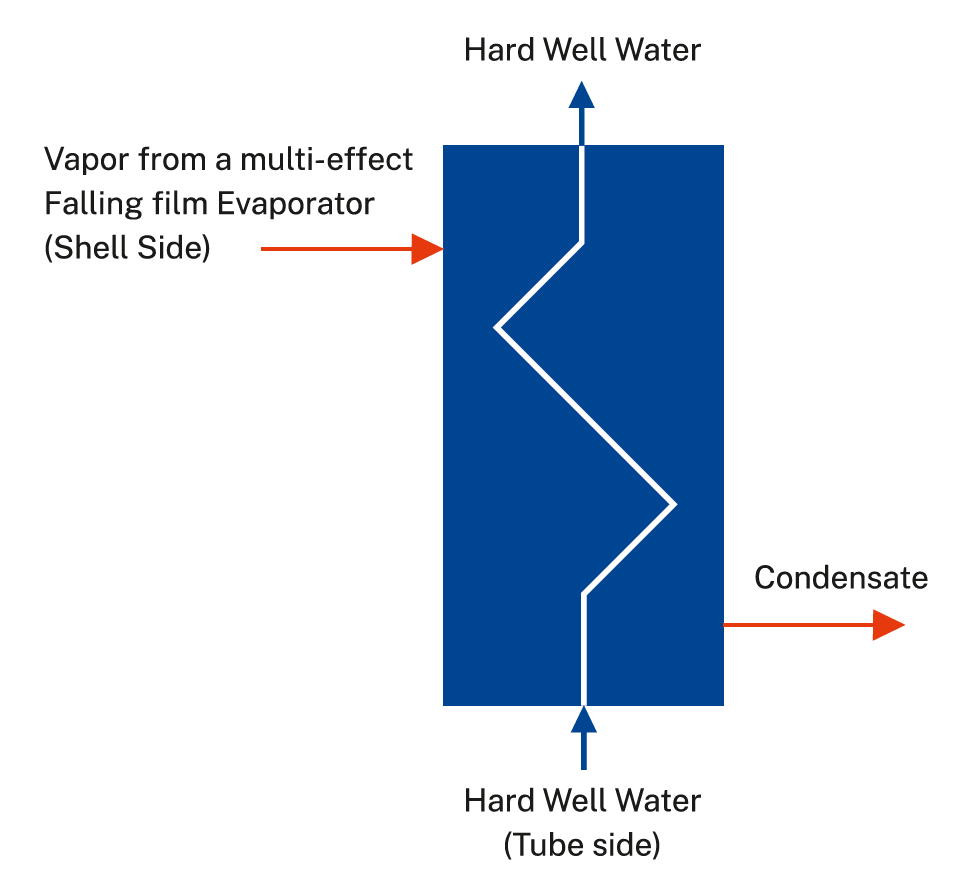
About this Technical Story
This Technical Story was first published in Heat Exchanger World Magazine in February 2024. To read more Technical Stories and many other articles, subscribe to our print magazine.
Technical Stories are regularly shared with our Heat Exchanger World community. Join us and share your own Technical Story on Heat Exchanger World online and in print.